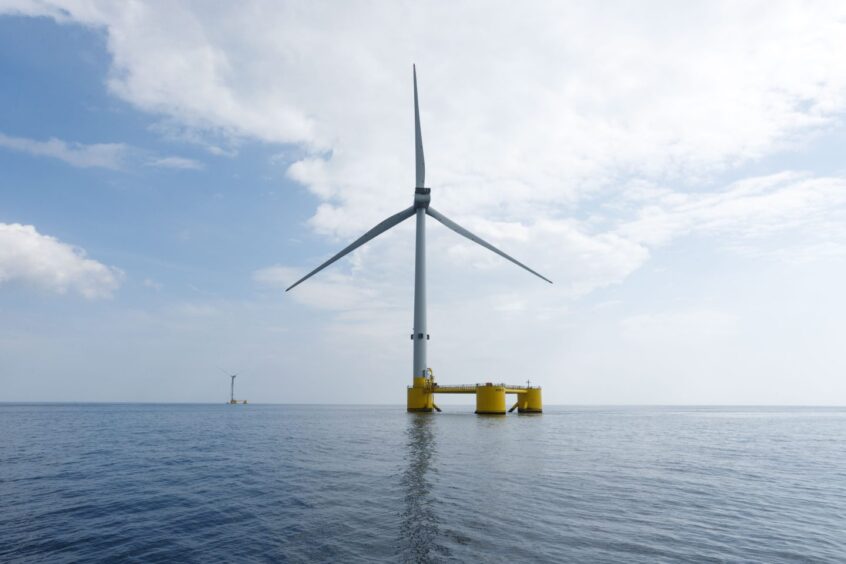
David Rennie’s comments around Hywind maintenance being a “lost opportunity” left me puzzled and asking the question as to whether or not he actually understands the floating turbine marketplace as well as he ought.
Of course, Scottish Enterprise’s head of low carbon energy and others have expressed dismay at the fact that Equinor is towing its Hywind Scotland turbines to Norway for heavy-duty workovers.
‘Oh woe is us’ they bleated. Why Norway? Why not here?
Well, there’s one factor that no one cared to mention and it is this. There is practically nowhere in the UK capable of receiving something with a draft of 80 metres or thereabouts and tethering them close inshore in a sheltered location next door to significant fixing-up facilities.
Well, there were a couple on the Scottish West Coast.
One was called Portavadie; an offshore fabrication yard on the shores of Loch Fyne where one can hide a nuclear submarine in 100 fathoms of water (180m) plus a bit more.
But Portavadie never built anything and its dock is now a marina.
There is Kishorn with 80m (260ft) in the approaches and where the Ninian Central concrete gravity base was built, but nothing else and so it was dumped. Today, it is back in business handling offshore floating production units, ships and whatever.
But Kishorn is not a runner for the kind of work Equinor is looking at. It simply does not have the facilities and access to the supply chains in Norway and the EU is fraught.
Then there’s another barrier, the Pentland Firth. Here are some numbers. Depths vary from 20m to 96m, with an average depth of around 60m.
Of course, there’s a huge deep gap between Orkney and Shetland, an awful place to be towing spar turbines in number.
Forget the East Coast. Too shallow and next to zero shelter for Hywind or any other spars for that matter.
So Norway it is, bags of sheltered deep water and excellent, ready facilities. You cannot ask for more.
Whilst in theory, it is possible to split the buoyancy and ballast sections of a spar hull for dry-docking, that won’t happen.
My presumption is that established offshore oil and gas practices will prevail. Let me explain.
No spar platform in the US Gulf of Mexico has ever been removed for overhaul. The oldest, Neptune, was installed in 1996, is still producing and is still held under American Bureau of Shipping classification.
So, whilst the pioneer Hywind spars are heading for Norway for overhaul, you can pretty well bet on this being the exception and that turbine head and equipment replacements will be carried out infield wherever possible.
It’s a logical conclusion to reach based on the oil and gas experience.
However, Rennie is spot-on questioning the shunting of pontoon/semi-submersible style units like Kincardine across the North Sea to locations like Rotterdam.
There are in principle ample locations around the British Isles with adequate room for parking such turbine floaters for overhaul and, if required, dry-docking.
The UK has a number of very large and underutilised graving docks. Harland & Wolff is the leader in terms of winning wind-related business. Time for all the others to step up to the opportunity and prepare for this new market opportunity.
But there’s an obstacle. The Great British Malaise.
‘Oh, say the potential investors to floater service centre hopefuls. We can’t risk our money unless you have some real biz in the bag first.’
The fact that, in 20 years or so there will likely be thousands of the things dotted all over our aquatory and the waters of North Sea neighbours plus Ireland, will somehow escape them.
I cannot blame Kincardine’s operator for sending one of its turbines to Rotterdam for repairs. It’s where the project’s six floaters were put together in the first place.
Consider this. You own the latest fancy car. Something goes wrong. You go to the dealer who sold you the machine.
Now, a wind turbine is a lot bigger, more complex and expensive than a car. But these machines are also series built. They are not one-offs like oil and gas platforms and oil equipment managers (OEMs) are key.
Of course, we don’t have OEMs. They’re on the other side of the North Sea. So guess who has the advantage? It’s not the UK.
This makes it all the more important for the UK PLC to get high-quality assembly and service centres for floating turbines built PDQ.
Recommended for you
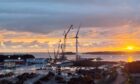