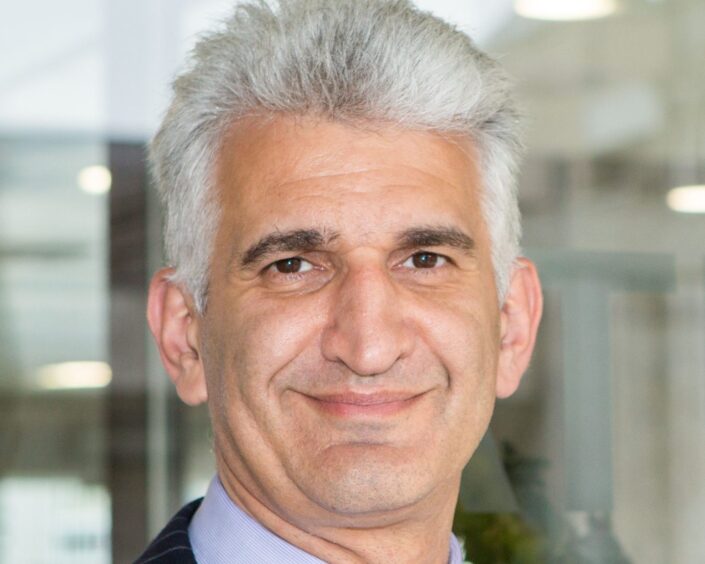
What makes a successful oil and gas project? By that I mean one which lives up to expectation in terms of cost, schedule and production.
The North Sea is a great place to look for answers. Its oil and gas industry is admired globally for delivering extraordinary feats of engineering in some of the harshest conditions on the planet – projects which have lit and heated our homes for decades.
Nonetheless, that does not mean the industry always gets everything right and can’t improve its performance. It can.
There isn’t a company out there that’s got all the answers, but by sharing experience and learning lessons across the industry, we can give ourselves the best chance of success.
The North Sea Transition Authority (NSTA) looked at almost 30 projects delivered in the last decade, and we noticed significant variation in delivery. So, we asked companies to do some soul searching. Why were some delayed, while others were early? Why did some balloon over budget, while others came in below the expected sticker price? Where there any common themes?
We distilled the many lessons learned down to six key ones. I revealed the lessons during a recent webinar attended by 100 industry professionals and asked them for their thoughts and experiences.
But, before going through them in this article, it’s worth noting that this process has real bottom-line value.
For example, two oil and gas projects carried out by teams whose work and behaviours most strongly corresponded with the lessons came in under budget by a combined £600 million. Three projects undertaken by teams whose approaches did not reflect the lessons were £2 billion over budget in total and suffered cumulative delays of more than four years.
What’s more, you can apply most of these lessons to any large-scale project, including maintenance, emissions reduction and even renewables.
Six lessons
One: Companies must have a robust governance system in place which enables them to identify and manage risks and uncertainties.
Many risks are foreseeable and if you spot a big one, then delay making a final investment decision.
Common sense? Perhaps. Yet, we’ve seen examples where the desire to approve and get on with a project was so strong that it clouded people’s judgement. They made an FID without mitigating the risk, leading to significant delays and overspend.
Two: Effective governance must be built on competent and professional project management.
Part of that means backing up important decisions with high-quality data and robust analysis. Managers need to be able to interpret the outputs and communicate them effectively. This supports informed decision making throughout the organisation across the project’s lifespan.
Three: The careful recruitment of a small core team can help maintain a consistent culture of ownership.
Establishing a tight-knit core group of people with the right mix of technical and personal skills, who stay together throughout the project, supports successful delivery by cultivating familiarity, trust, ownership and collaboration. Resist the temptation to disrupt, no matter how strong.
Four: Collaborative cultures ensure all stakeholders are integrated into the team and are heard.
This is all about harnessing the experience of the wider organisation, with the supply chain front and centre. This is especially important as corporate knowledge and experience changes over time.
People retire, transition to other industries, work in hybrid pattens and are based in different geographical locations. It has been proven time and again that bringing suppliers on board right from the start of planning helps address complex issues. By “on board”, I mean properly integrating contractors – get them into your office.
Five: Assess all options for reducing subsurface uncertainty.
The subsurface is a massive part of what this industry does – and does well. But we’re sometimes too optimistic. There’s a definite tendency to focus on the upside of subsurface work. Consider the downside as well. Not to the point where you talk yourself out of doing anything but do consider it.
Six: Articulate and maintain a simple, consistent, precise and coherent definition of the project.
Imagine stopping a team member during a project and asking them to write a simple summary of what the project is and what it hopes to achieve. Do you think they could do it? Do you think a different team member would write the same thing, more or less? If not, that might be a problem.
It is very important to communicate what is required, why it is required and when it is required to the project team. The project definition must be written in a way that can be consistently interpreted and understood by a diverse technical team. At all costs, avoid the use of ambiguous jargon and generic phrases such as “fit for purpose”. What does that even mean?
You may consider any or all of these to be blindingly obvious. And yet our analysis and digging showed clearly that these key pieces of advice have not been adopted across the industry. Taking them for granted and complacently thinking, “well, we would just do that, naturally,” is a big mistake. Follow them as closely as possible and give yourself the best chance of success.
John Spiteri is senior project advisor at the NSTA