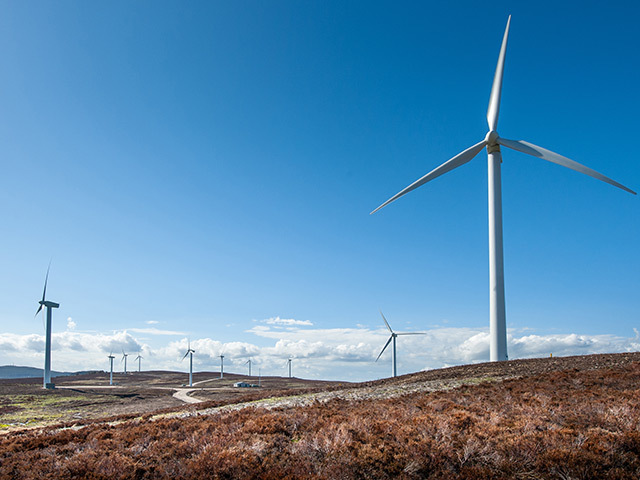
Whether it is imposed upon a company externally or driven from within an organisation, audit – that ubiquitous marker of corporate performance – is often a troublesome process.
Whether you find yourself ticking boxes to satisfy a certification body, client or parent company, or even if you are genuinely striving to improve, all too often a truly quality driven approach to auditing is missed. This need not be the case.
Having spent a large portion of my career working for Asian companies and spending months if not years on various sites, plants and offices across Asia, I have witnessed first-hand how a successful auditing process can enhance performance and help us challenge the status quo.
So why in the UK do we consistently fail to get the most from this process and how can we re-think it, to make it a meaningful tool for success? That includes in the renewables industry.
In most cases I believe management acknowledge that auditing forms a valid part of their review matrix, ensuring that processes and procedures are being followed as expected and showing whether goals are being met. However, when audits do not report back any problems or significant findings, there is a tendency to think that everything is rosy, perhaps even that audits are no longer necessary.
This is when vital clues to the wellbeing of an organisation are lost, as are opportunities to improve.
In economically tough times, company management come under increased scrutiny to measure all costs and strive for reductions, making auditing an area that, on paper, appears ideal for cutbacks.
After all, if our audits are not revealing any issues, we could easily reduce their number, duration or worse still, remove the need for the programme entirely.
However, if we step back and look at the bigger picture, with the idea of continuous improvement at the forefront of our minds, we see that the reason no shortcomings were highlighted is not because the corporation is functioning at its best but because the audits themselves were ineffective.
So what constitutes an effective audit strategy? Firstly, management must support the ethos of continuous improvement and distil this culture throughout the organisation.
If cost reduction is sought, it is best found in smarter, effective and more efficient ways of performing operations, not in cutting the true mechanism that feeds this programme; auditing.
If an internal audit programme is working then all processes can be improved – real cost reduction may be possible, while improvements are still applied.
Secondly, management should address who they assign the audit roles.
Often it is personnel who have a day job and don’t want to carry out these activities in the first place.
If an individual is being asked to do something they are not motivated to do; they will not be performing at their best, they won’t challenge assumptions and most importantly they will want to get it over and done with as quickly as possible, with minimum follow on impact to themselves.
Their work from their day job is still waiting for them remember!
Good effective auditors would be those who have vast experience across the organisation and ideally similar experience across various organisations, thus bringing some of the best practices to bear.
Granted, such persons can be found within an organisation, but they tend to be senior managers and directors, who often don’t get involved in audits and would most likely not have the time to perform them, not forgetting that it would hardly be value for money!
The last option that management are left with, is to have a team of dedicated in-house auditors, who utilise other employees to form part of audit task groups and we’ve already mentioned some of the problems with this above.
As the “team” mainly perform just a handful of audits per year (sometimes members may do just one per year), it does call in to question whether they have the competencies required to identify deficiencies and drive performance.
Further shortcomings of this model include: Lack of support and formal audit training. Often there are no mentors and skills learned previously are soon forgotten if unused.
A lack of knowledge of the subject matter, especially in technical processes, leaves auditors unable to challenge entrenched behaviour and overall unrefined audit techniques which focus on quick easy targets, such as administrative errors, leaving other serious issues overlooked.
Outsourcing your internal audits may be the solution.
Outsourcing utilises the services of professionally chartered auditors with the necessary background, technical knowledge and vast experience. You are able to access the right individuals with the right skills at the right time, thus not requiring to use a less knowledgeable employee just because they are available, who may not possess the appropriate competencies.
In general, the outsourced audit solution, for both internal and external audits, should provide a more cost effective approach, especially if it drives improvements throughout your business through process efficiency, improved safety, reducing waste, contractor management and ultimately achieving assurance. It often does it in less time too!
The FQM audit team comprises a number of senior subject matter experts from various disciplines and industries. Combining that with an auditor training programme and a strong desire to share a lifetime of knowledge, they mentor your team and raise their competency.
Chris Docherty is director of FQM Ltd, a health, safety, environment and quality consultancy and training organisation.
Recommended for you
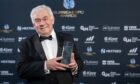