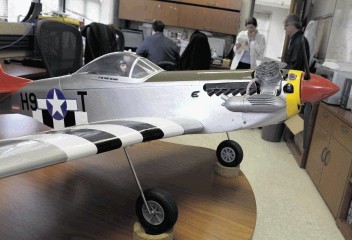
Here we go again . . . All-Energy is back in Aberdeen and, hopefully, it won’t suffer the meteorological battering handed out by Mother Nature last year.
When conceived at the turn of the Millennium, the decision was deliberately taken to overtly avoid the renewables tag line.
This was deemed critical if the oil and gas supply chain was to become engaged in new energies.
By and large that appears to have worked and, even though renewables investments in the UK have taken a hammering of late with several major offshore wind projects especially pushed back, the oil and gas supply chain has gained market share, which is good from my perspective.
However, the world of renewable/sustainable energy is richly varied; with many technologies under development. It’s not just wind, wave, tidal and biomass. There is much else besides.
And it is on one aspect of the “much else” that I have decided to concentrate on; not the state of Scottish, UK or EU mainstream renewables.
The topic is naval aviation fuels.
For centuries, alchemists of old sought to convert base metal to gold. They all failed; it proved impossible.
For not as long, scientists and eccentrics have sought an energy nirvana based on super-electrolysis of fresh water. They failed too . . . thus far.
However, improbable as it may seem, the US Navy may have cracked this particularly hard nut by simultaneously extracting carbon dioxide and hydrogen from seawater.
The gases are then converted to liquid hydrocarbons by a cheap iron-based metal catalyst in a reactor system.
Moreover, the fuel created has been used to fly a model aircraft fitted with a totally conventional two-stroke internal combustion engine.
But why is the US Navy dabbling in this way via its Naval Research Laboratory (NRL)?
The answer is simple. The USN is anxious to make its high seas fleets fuel-autonomous, starting with carrier-borne aviation. Carrier groups especially are rendered vulnerable because their aircraft and escorts use hydrocarbon fuels while the “flat irons” and associated submarines are nuclear-powered.
So what if they could carry equipment capable of converting seawater into fuel . . . and sustainably?
Not only would it transform the US fleets’ ability to stay at sea indefinitely, the technology under development could revolutionise the production of liquid hydrocarbon fuels; in essence rendering them renewable.
That would be dramatic indeed and may simultaneously challenge both the conventional petroleum and renewables (notably bio-fuels) industries as we currently know them.
Of course, like so many other apparently promising energy systems, is the US Navy’s seawater-to-fuel concept scalable? Is it the game changer that is already being claimed.
Here’s how it works.
Using an innovative and proprietary NRL electrolytic cation exchange module (E-CEM), both dissolved and bound CO2 are removed from seawater at 92% efficiency by “re-equilibrating carbonate and bicarbonate to CO2 and simultaneously producing hydrogen.
The gases are then converted to liquid hydrocarbons by a metal catalyst in a reactor system. In turn, the liquids produced can be used for petro-chemicals feedstock or undergo further formulation to make jet grade fuels.
Dr Heather Willauer, NRL research chemist, says the lab really has developed a “game changing technology”.
Apparently, this is the first time technology of this nature has been demonstrated with the potential for transition, from the laboratory, to full-scale commercial implementation.
CO2 in the air and in seawater is an abundant carbon resource, but the concentration in the ocean (100 milligrammes per litre (mg/l) is about 140 times greater than that in air, and one third the concentration of CO2 from, for example, flue gas from a power station (296mg/l).
Two to three percent of the CO2 in seawater is dissolved gas in the form of carbonic acid, 1% is carbonate, and the remaining 96 to 97% is bound in sodium bicarbonate.
NRL says it has made significant advances in the development of a gas-to-liquids (GTL) synthesis process to convert CO2 and H2 from seawater to a fuel-like fraction of C9-C16 molecules.
In the first patented step, an iron-based catalyst has been developed that can achieve CO2 conversion levels up to 60% and decrease unwanted methane production in favour of longer-chain unsaturated hydrocarbons (olefins).
Hydrocarbons from this process serve as building blocks for the production of industrial chemicals and designer fuels.
In the second step these olefins can be converted to longer chain compounds by controlled polymerisation.
The resulting liquid contains hydrocarbon molecules in the carbon range, C9-C16, suitable for use as a replacement for petroleum-based jet fuel.
NRL says the cost of jet fuel using this process is in the range of $3-$6 per gallon and that, with sufficient funding and partnerships, this approach could be commercial in seven to 10 years.
NRL operates a lab-scale fixed-bed catalytic reactor system and the outputs of this prototype unit have confirmed the presence of the required C9-C16 molecules in the liquid.
This system is the first step towards taking the NRL technology and engineering it into commercial, scalable modular reactor units,
The process efficiencies and the capability to simultaneously produce large quantities of H2, and process seawater without the need for additional chemicals or pollutants, has, according to NRL, made these technologies “far superior” to previously developed and tested membrane and ion exchange systems for recovery of CO2 from seawater or air.
This really does look like a game-changer; maybe endlessly sustainable.
Recommended for you
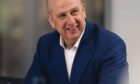