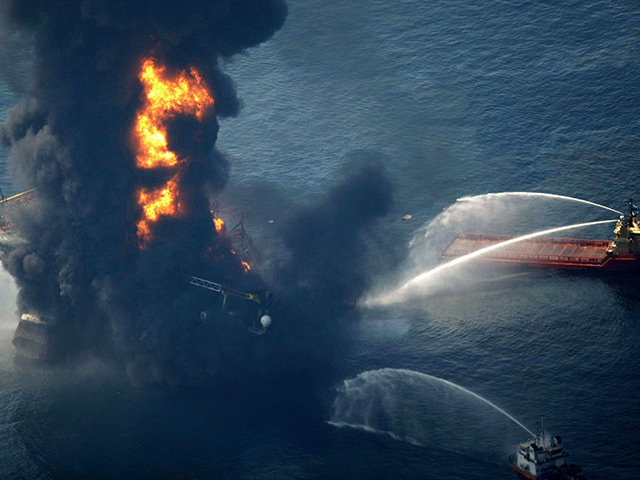
Imagine two airplanes flying toward each other on a collision course. In the modern world of commercial aviation, two planes with conflicting flight paths would trigger alarms in in the air traffic control tower. That’s because the safety of commercial aviation relies on the use of real-time data to avert disasters. The same can’t be said for the offshore oil industry.
Four and a half years after BP’s Macondo disaster in the Gulf of Mexico, the industry remains reluctant to use drilling data it collects from rigs to enhance safety.
Alarms sound on a rig only after something has gone wrong. David Pritchard, a Houston petroleum engineer and co-chair for the technical committee of the Deepwater Horizon Study Group, envisions a system where, much like with air traffic control, real-time data can be used to alert rig operators to potential problems before they become catastrophic.
“We have that same capability, we have that technology, we just don’t use it,” Pritchard says.
“What the industry needs is a proactive system of alerts as opposed to a reactive system of alarms.”
Incidents involving the loss of well control haven’t declined since the Macondo disaster, Prictchard says. In fact, they’ve increased, underscoring the need to change the industry’s thinking about preventive measures. Offshore oil production remains decades behind other industries, including the refining sector, when it comes to using real-time data to enhance process safety, Pritchard says.
That’s why he’s developing a software program that would function much like an air traffic control system for drillers. It would monitor key parameters and alert operators to any abnormalities, such as changes in pump pressure or fluid losses.
Discussions of the Macondo disaster typically focus on the events leading up to the fatal blowout on April 20, 2010, which killed 11 men on board the Deepwater Horizon, the Transocean rig drilling the well.
Pritchard, however, notes that there were other warning signs, dating to months before the accident. The well was being drilled so quickly, however, that no one stopped to analyze early signs of potential problems with the well design.
For example, the well experienced a kick on March 8, a month and a half before the disaster.
Although the warning signs were evident in the real-time data before the kick occurred, no took the time to analyze the information as it came in. While the kick may have been unavoidable, BP’s own investigation into the accident found that the emphasis was on moving forward with the project, which was behind schedule and over budget.
The kick was minor incident compared with the blowout that came later, but BP was forced to drill a sidetrack, which resulted in a two week delay at a cost of about $1 million a day.
Companies often are reluctant to slow down the drilling process to analyze data, Pritchard argues that being cautious is worth the extra time.
“If you take time to slow down, stop, look and listen, it always saves you money,” he says.
“In our industry, we don’t take that into account. If we begin to look inside and realize that can mitigate and often prevent things like kicks and fluid loses, that saves us a huge amount of time in the back side.”
Pritchard has received funding for his project and is developing the program using test well data provided by one producer. The program is a designed as a series of modules, the first of which Pritchard hopes to have available in the second half of next year.
In one case he analyzed, a company ignored rising gas levels in the well. When it blew out, it showered the rig floor with condensate, and the company lost 10 days stabilizing the well.
The company should have slowed down, analyzed the data coming from the well, and circulated gas out of the well bore before proceeding, Pritchard says. A few hours of circulation, he says, would have saved days spent re-stabilizing the well, and ultimately reduced the risk of a blowout.
“The system I’m building will have suggestions for re-establishing reliable well bore stability before you continue,” he says.
The challenge, he says, will be convincing upper management of his program’s benefits. Because of the huge cost involved in offshore drilling, many companies are focused solely on the short-term expense of delays, rather than the long-term savings of avoiding accidents. Just a few hours of proper corrective actions can save days of recovery efforts and wasted time.
“If we can begin to focus on the fact that real-time systems will save time and money, then we’ll change the model,” Pritchard says. More importantly, it also could save lives.
Until attitudes change, the industry is flying blind.
Loren Steffy is a managing director with the communications firm 30 Point Strategies. He is a writer at large for Texas Monthly, a contributor to Forbes and the author of Drowning in Oil: BP and the Reckless Pursuit of Profit and The Man Who Thought Like a Ship. Follow him on Twitter: @lsteffy; on Facebook or at lorensteffy.com.
Recommended for you
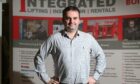