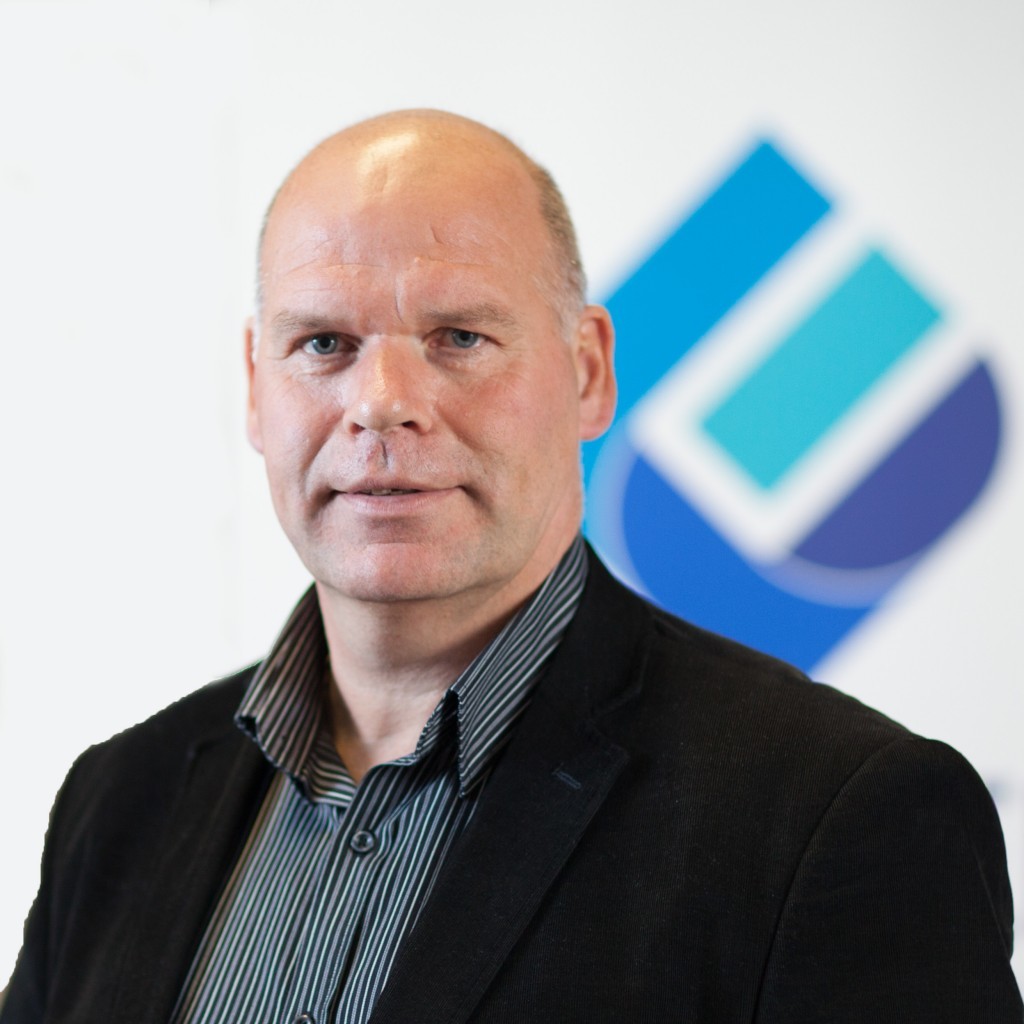
Decommissioning has been on the oil and gas agenda for many years, although to the majority within the industry it was something not to be concerned about “now”. It would be carried out “mañana”, and by someone else.
From the majors through to the smaller independents and the supply chain, everyone has been forging ahead with the development of new wells and maintaining existing ones, too busy to think of the day these fields would become unprofitable.
There is now a dawning realisation that the vast majority of wells within the North Sea and other brownfield areas across the globe are now at, or near, the end of their lifetime and need to be abandoned.
However, this is not just a case of pumping cement, cutting the pipes and clearing the seabed.
Safety considerations, legislation and environmental impact all need to be taken into account, and even after the wells have been successfully abandoned, liability does not stop there.
If leaks develop post abandonment, the obligation to go back and reseal the well remains.
This may not be easy, or even possible, depending on the source of the leak and difficulties with regaining access. Therefore doing it right the first time should be everyone’s priority, when planning and executing the decommissioning phase of these wells.
Whether the wells are platform based or subsea, each will have its own unique challenges when the time comes to decommission.
From a subsea perspective, my main concerns are the conditions and state of the equipment on the wells, along with the availability of the equipment that was used for installation and during the periodic workovers and interventions on the wells.
Over their lifespan, subsea wellheads and xmas trees have had to endure the environmental conditions externally, and the varying production conditions internally.
Questions need to be raised, such as has the cathodic protection worked effectively and preserved this equipment over the years? Has the equipment’s design lifespan been stretched? Will the equipment stand up to the stresses and strains that it will be subjected to during the abandonment?
These are all legitimate concerns that could lead to issues with the equipment’s integrity during the re-entering and abandoning process.
Dual bore risers, LRP/EDP configurations and wellhead tooling were all available and in good use during the installation phase but often left lying in disrepair, forgotten about whilst the wells were flowing, too costly to preserve and maintain over the years.
Now this equipment is to be brought back to life to allow access to these subsea wells, so that they can be abandoned in a safe and methodical manner.
In some cases the equipment may be beyond repair or even scrapped, therefore various components could be obsolete and not available to rebuild!
Equipment exists which belongs to either the operators or the original manufacturers that could be refurbished for this work.
However it is in short supply, and over the years the interfaces with this type of equipment have changed due the different operators’ or vendors’ requirements and preferences.
Therefore compiling a system which can handle single or various wells is problematic, costly and time consuming. Well operators should work together to share resources, be that equipment, DSVs or rigs, to assist in keeping costs down.
Every party has its own cost restraints, timelines and agendas which can make collaboration more difficult.
There are various ways to decommission wells, the main driver being the condition or status of the well(s) themselves.
There are many considerations which must be taken into account to ensure each well is correctly abandoned, but this must also be done as cost effectively as possible – there is no financial upside to decommissioning.
Light intervention costs are closer to rig based abandonment costs than they normally would be, due to the current market.
Supply chain companies are cutting their rates and have engineering and workshop capacity to assist with getting equipment ready and available for this work.
Well operators need to take this into consideration and take advantage of the current situation, but even if they begin to act now, in many cases it will take a minimum of 12 months before operations offshore can commence.
Finally, with the current industry downturn, valuable experience will be lost to the industry forever.
Knowledge of outdated equipment and systems may be no longer accessible. This must be taken into consideration whilst assembling teams and planning and executing the abandonments, to ensure their success and that they are carried out in a safe, environmentally friendly and cost effective manner.
Ross Mack, is subsea manager at Exceed, in Aberdeen
Recommended for you
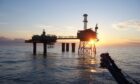