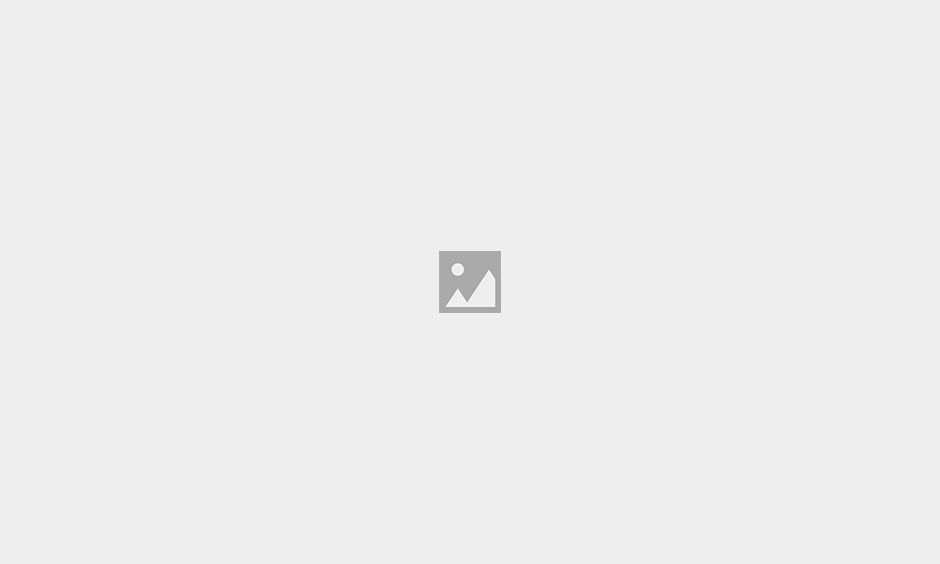
Electric submersible pumps (ESPs) located in production riser pipes as opposed to deep underground in wellbores offers a cost-effective means of extending field life, says Centrilift.
The usual location for an ESP is in the well, sometimes 20km or more from a platform, and it is accepted that ESP installations and workovers are costly exercises.
However, by installing an ESP in a riser costs are reduced significantly and operators can quickly realise increases in production.
Tiffany Pitts, the engineer who last year led the first installation of an ESP in a riser in the Gulf of Mexico, is now based at Baker Hughes Centrilift’s regional headquarters in Aberdeen and she believes the technology has real potential in the North Sea.
According to Pitts, installation of a Riser Lift ESP in well number one in the Anadarko-operated East Breaks field in the Gulf of Mexico last year immediately increased production, and the operator has estimated that it will ultimately increase overall recovery by 35%.
The well is a subsea tieback to a spar. When pressure depletion caused slugging and frequent loading in the well’s riser and subsea flowline, production fell significantly, leaving considerable reserves in the ground.
To recover the remaining hydrocarbons, some form of artificial lift was required. Gas lift was not an option as there was no suitable infrastructure available, and a traditional ESP installation would not be cost-effective as it would cost about $30-40million to hire a suitable intervention vessel and instal a power supply into the well.
The future of the well looked bleak. However, Anadarko senior completions engineer David Cocciolone was aware of Centrilift’s Riser Lift system, which would provide the artificial lift required for the well for less $4million.
The fact that this was essentially an unproven system did not deter Anadarko; it felt there was nothing to lose. Without an artificial lift solution the well’s productive life was very limited and the remaining reserves wouldn’t be recovered.
“Finding an operator prepared to take a lead on a technology can be a real problem in this industry, so Anadarko’s enthusiasm was very refreshing,” said Pitts.
The concept is quite elegant. Deploy the ESP with a simple low-cost workover unit and hang the pump in the riser. Cable requirements are minimal and the workover costs are vastly reduced. However, there are potential downsides.
“Riser Lift isn’t a replacement for traditional ESP deployment as there are performance penalties when compared with ESPs nearer the reservoir, and there is concern that installing equipment in the riser could lead to internal damage or wear,” said Pitts.
“However, in situations like East Breaks number one, it offers a real opportunity for operators to extend production and recover additional reserves.”
Centrilift reckons that the technology offers a cost-effective solution for continuing production of mature subsea tiebacks which have no form of artificial lift previously installed.
Pitts added: “With many subsea wells reaching the latter stages of their life in the North Sea, Riser Lift could be an important technology in the region.”
Anadarko saw an immediate production increase of 2,500 barrels of oil per day at East Breaks, with estimated ultimately recoverable oil up more than a third compared with before the retrofit. This deployment was the subject of a recent SPE paper .