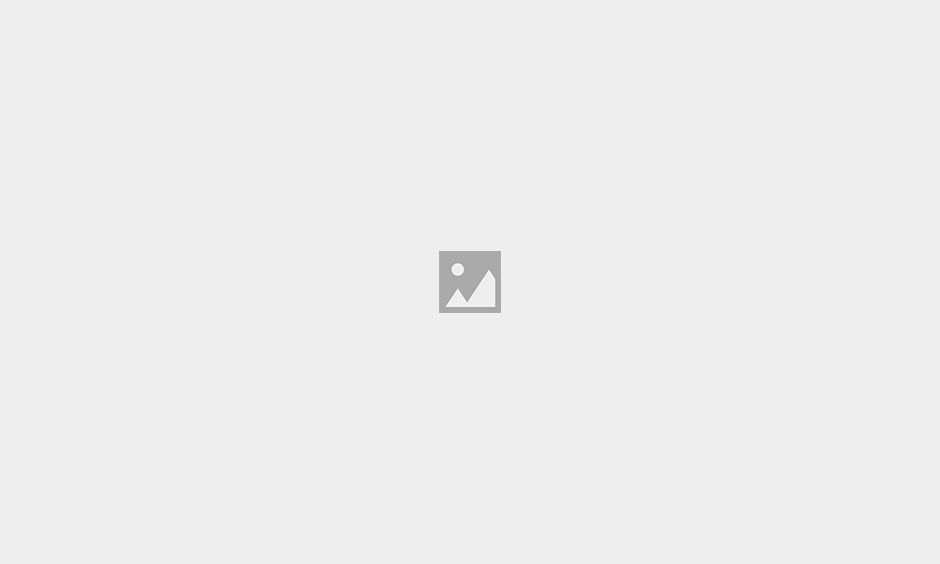
Lewis Limited, of Aberdeen, is a subsea engineering company specialising in bespoke design-and-build and operation of riserless and lightweight subsea well-intervention equipment. That includes lightweight risers to surface for coiled-tubing intervention as well.
The roots of Lewis lie in the fact that its MD, Drummond Lawson, previously ran Schlumberger’s light well intervention unit prior to it being divested to Well Ops, which is a unit of Helix Energy Solutions.
“At that point, I saw an opportunity to set up a business that, in its early stages, would support Well Ops and, in parallel, would develop specialist technologies for light well and riserless subsea well intervention,” says Lawson.
“That’s how we’ve ended up where we are today.
“We have developed our own technology, filed three patent applications to date, with more on the way, and we are currently building the first of our own equipment that we have designed and developed ourselves. This will be ready by the end of this year.
“That’s a very high angle emergency disconnect package which is designed to achieve release at angles way beyond what existing connectors can currently cope with.”
For those in the offshore industry who understand this sort of thing, Lawson is talking about a release angle of 17.5 degrees, versus the more usual less than 10 degrees. But light well intervention is where he really wants to steer the company, which currently has a head count approaching 20 people, turned over £1million in its last financial year and is, according to Lawson, heading for £2million in the current year.
A big lever in terms of expansion is that Lewis – the firm is based on Aberdeen’s Balgownie Technology Park – has taken on 8,000sq ft of workshop space less than five minutes’ drive away.
“Until now, we’ve had to outsource all of our workshop work to others and then supervise. That will allow us to bring this in-house and enable greater quality and cost control over our products.”
But what makes Lawson think such a small firm can compete against big brands such as Expro, which is spending millions on rigless deepwater well intervention systems and will be high- profile at this month’s SPE/ICOTA conference in Aberdeen?
“The biggest difference is that we are basing our system designs on existing technologies,” he says, pointing out that he was directly involved in developing the systems currently used by the Helix vessel, Seawell.
“One of the guys here has worked aboard Seawell and operated both of those systems. We have a very broad range of in-house experience, including from a guy with a background in the salvage industry, where he designed and operated equipment down to 4,000m and has brought some very valuable experience across from that industry.”
His name is Patrick Crawford, son of the renowned Scottish salvage partnership, Alec and Moya Crawford.
Lawson: “Based on a combination of the prior experience that we have in being involved in the two systems aboard Seawell, coupled with Patrick’s experience, plus experience we have through other people, we’re confident we can build systems in a shorter time than what Expro is doing.
“The biggest difference between ours and Expro’s systems is that we currently intend to keep the wireline unit on the surface. So we’re looking at putting well and pressure control subsea but keeping the wireline equipment on the surface. Expro is putting its wireline winch and a carousel arrangement subsea, which hugely increases the complexity of the system subsea.
“The equipment will be deployable from any DP (dynamically positioned) class II or III OSV (offshore support vessel) … generally it’s DP III in the North Sea and DP II outwith.
“The way we’re designing our systems is that each is bespoke to the customer and vessel which it is going to be operated from.
“For example, our parent company, Marine Subsea (it acquired Lewis in February, 2008), is building two vessels that are sisters to Island Offshore’s Island Constructor, and we have done the FEED for the systems to go aboard these new Ulstein-designed vessels.
“The systems for which we have done the FEED are designed to operate in the range 80-2,500m subsea. But we’re not building those systems until there is a confirmed client wanting to use them aboard the vessels.”
Lawson agrees that oil majors, especially, have been slow in getting to grips with subsea well intervention.
“The way I see it is that the oil companies want to maximise ultimate productivity … subsea wells tend to recover half to 60% of what a dry riser well can produce, so you’re looking to 30-40% of reserves in place being recovered by a subsea well, compared with 45-55% with a platform-based well.
“That’s also why those wells that are producing less tend to get sold on to the smaller players. Smaller players tend to have greater focus on ultimate recovery than larger players. But, having said that, the larger players do design the completions in the wells and the drilling of the wells generally for the ultimate recovery that you’re going to achieve at the end of the day, even if the drivers from the senior management of the business during the life of a well don’t always dictate that that’s how its going to be run.”
Lawson says operators are also keen to sustain maximum production rates, but also reduce costs, and that this aligns with the whole purpose of light well intervention.
“You want low cost, maximise recovery and improve ultimate recovery. It seems to be that there is a very close match between all the objectives of light well intervention and all of what I see as being the major objectives of the oil companies. And yet there is this big gulf.
“Where that seems to be coming from is the fact that the people who hold the purse strings are generally the asset managers, and their heads are on the block if they don’t achieve set objectives. They want to minimise risk so that, if well intervention is required, they will use a rig.
“They see a rig as the safe bet. It might cost them more, but they know the job’s going to get done.
“As for light well intervention, there’s always this niggle at the back of their minds that, if they run into a problem, they’re going to have to get a rig anyway.”
But then there’s the rig rates issue – $600,000 per day versus bare vessel for about $80-150,000 per day – or $250,000 per day if an intervention vessel of the kind Island or Marine Subsea can offer.
Lawson reckons the kind of equipment that Lewis is developing offers the potential for piloting a major intervention by sending in a suitably fitted run-of-the-mill OSV to go and find out what the key issues are so that a campaign can be mapped out and the best vessel/rig option chosen.
“Potentially, a multi-level approach like this could be a more efficient method for dealing with large fields in areas such as West Africa, Brazil, and so forth.”
There is already that need in West Africa.
“Currently, you’re looking at somewhere in the region of 250-300 wells which are of an age that subsea intervention is starting to become of interest to their operators. The way we look at it, subsea wells will usually require intervention from about five years and older.”
So does this mean that Lawson and his team are already spoiled for choice and could even be swamped with opportunities?
“The biggest difficulty from our point of view is that the number of people looking to enter the market and wanting to work with this kind of equipment is growing rapidly and we’re now wrapped up in confidentiality agreements left, right and centre … quite rightly.”
It’s a nice problem to have in recession-hit Britain.
Recommended for you
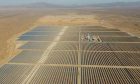