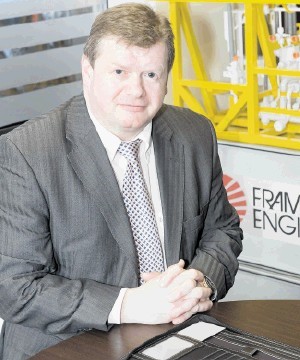
NORWEGIAN company Framo Engineering has been immersed in the development and manufacture of robust subsea, enhanced recovery and marine technologies since 1983.
The group has three business streams: swivel and marine systems, metering systems and pump and subsea systems, with the aim to offer flexibility to field developments, both brown and green field and shallow and deep water.
The company is a leader in its field. Tony Laing, general manager of Framo Engineering UK, said this had been achieved by a clear market focus and a high level of investment in people, plant and processes that are second to none.
Later this year, Framo will be opening its new facility outside Bergen. “Horsoy” will be a centre of excellence with two subsea test docks and a live hydrocarbon loop.
It will be coupled with indigenous detailed engineering skills, encompassing process, mechanical design, power, umbilical and controls, and capturing the depth of experience over the whole field life.
The company also works closely with operators, and believes this is critical to being a leading systems supplier.
Framo Engineering is the largest independent swivel systems and fluid transfer supplier for floating production units, and operates closely with Teekay in Oslo on turret production mooring systems.
This year, the company was awarded a contract for the BG Knarr project in the North Sea and projects in the global market, such as Brazil.
According to Mr Laing, the swivel and fluid transfer market is an exciting one and highlights the opportunities available in deep and shallow water, creating flexibility for the process host.
Framo Engineering metering systems are synonymous with well testing and process management.
Mr Laing highlights that the core metering technology, introduced in 1999, has continued to be developed to address the process needs, including high pressure (15K psi) and high temperature (400F).
However, today’s metering systems are more than just a process intelligent instrument; they also provide a robust means for carbon accounting and fiscal accounting. Operators throughout the North Sea are using metering technology successfully to optimise productions.
“In the North Sea market we have frame agreements as a result of developing close relationships with many operators,” said Mr Laing, adding that Framo Engineering makes a major contribution to the industry as the leader in subsea processing systems.
“We have delivered 26 of these and believe we’re the only manufacturer with seabed pumps operating worldwide; and we have just short of 1.5million operating hours of experience across these systems.
“However, from this experience it is clear that it is not just the pump technology but the whole system that makes the difference, that is the power system, controls and umbilical, all normally within the scope.”
The boosting technology covers a wide envelope, from water injection, multi-phase, and high boost for deepwater applications, and also hybrid, which is specifically designed to address gas carryover from separation applications.
Highlighting gas compression, Mr Laing added that, traditionally, operators leaned towards drying the gas by separating out water content, then boosting it. But that means they still need liquid pumps, a gas compressor and a separator.
In the subsea context, this approach is considered by some to remain unproven and too expensive.
Framo has taken a different approach by developing wet gas compression where the wet gas itself is boosted, creating “a true wet gas compressor”.
“What we’ve done is combine technologies from our experience of centrifugal (single phase) and heli-coaxial (multi-phase) and created contra-rotating equipment. It is unique to Framo,” said Mr Laing.
There is an industry perception that processing boosting systems are for deepwater applications; not so. For example, it is appropriate to the North Sea, including marginal brown field developments.
“If you can boost that extra bit you can maximise reservoirs and, furthermore, you can potentially widen the choice of candidate host facilities,” said Mr Laing.
He stressed the need for achieving the correct energy balance during production; it is often about not necessarily looking at a single solution and combining artificial method to achieve both capex and opex value.
For example, not just assuming gas lift as the only option, which can be operationally expensive.
However, by using gas lift from the reservoir to subsea wellhead, but then employing subsea booster pumps to deliver it to the host facility, significant cost savings are possible. Similarly ESPs can be teamed up with booster pumps located on the seabed.
Mr Laing said seabed pumps were very reliable, typically enjoying run lives of 8-10 years. They are also easy to repair or replace.
“Realistically, in the event of any upset, you can change out a seabed pump in a dive shift,” said Mr Laing. “You don’t have to intervene down a well, it’s very fast-track, you can do it with very simple intervention tooling, which is part of the system scope.”
They are also excellent for aquifer support – maintaining pressure to enable hydrocarbons production.
Framo did exactly this for the UK Continental Shelf Columba E terrace field four years ago, and last year provided its fourth system to Petrobras in Brazil for the Albacora field.
Continuing the energy balance theme, in the multi-phase context, Premier Oil’s Brenda field development is another example.
“They have what we call a MulitManifold – a compact process manifold solution – which uses the core Framo technologies, including our multi-selector, which enables production metering without valve isolation and complex controls.
“That, together with a multi-phase pump and Framo controls, is the central hub of that operation.
“That makes it a complete production process and well managment system.
“Brenda is about energy balance where they’re using a combination of gas lift and multi-phase pumps. They could have used gas-lift only, but in simple terms they would have ended up producing the gas and liquid phase.
“They could have used just multi-phase pumps, but they would have got performance ‘x’. They could have used ESPs and got performance “y”. But a combination of gas lift and multi-phase pumping allows the operator a longer-term, consistent approach to production.
“And that is the key – achieving optimal energy balance. The Framo MultiManifold process management system portfolio has grown, we have delivered over 60 systems between topside and subsea; the latest subsea system (manifold, controls, metering and scale squeeze) in the North Sea was delivered to E.ON for the Huntington field last month.”
Meanwhile, Framo has a very active tender book, in all three business streams, right across the global market.
“We’ve had a number of inquiries lately, including from super-majors who have not been much engaged before. That’s encouraging,” said Mr Laing.
“Just before the summer, we were awarded the Jack St Malo pump project in the Gulf of Mexico. That’s a great project for us and I think it will set the stage for Framo involvement with many more projects.
“But I still see fantastic opportunities on the UKCS for Framo systems to enhance oil and gas recovery – for large operators and small independents and from mini-fields in the North Sea to large, low-pressure reservoirs in the West of Shetland sector.
“We’re looking at a great future.”
Recommended for you
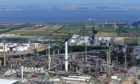