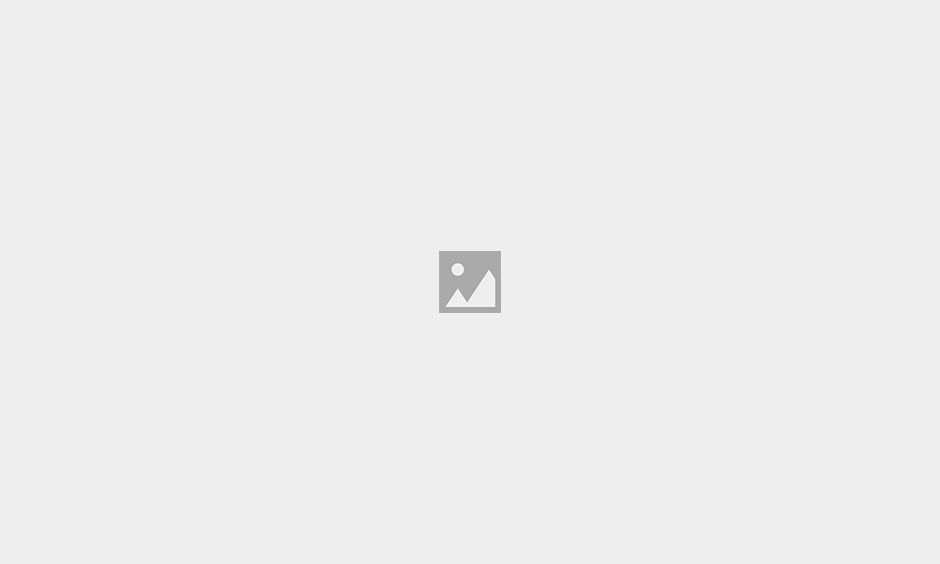
Here at Energy we enjoy highlighting the development of new technologies, and it is always a struggle to create sufficient space for them.
The emphasis tends to be on those that are cutting their teeth rather than with an established track record, which is pretty much where Expro Group’s ViewMax sideview downhole camera has progressed to. Indeed the device this year won a coveted 2008 Offshore Technology Conference ‘Spotlight on New Technology’ award, and that demands some track record.
This is a device that provides a high-resolution image of the inside of the pipe or open hole when run in a transparent fluid such as water or gas, or when fluids are displaced with nitrogen.
Expro says the video images, stationary and movies, are easy to use and interpret when fishing, diagnosing well integrity and production behaviour. ViewMax incorporates a second camera in Expro’s downhole video patented backlight camera lighthead. The second camera is pointed sideways and can be rotated, allowing unobstructed and undistorted views of the wall of the pipe or open-hole formation.
The ground-breaking technology has completed several hundred missions and is capable of functioning at pressures up to 10,000psi and temperatures up to 257F (125C) in a small 2
Deployment successes include on a coal-bed methane project onshore US. An operator of a shallow 640m ((2,100ft) coal-bed methane well in the San Juan Basin used a sand hydro-jet tool to create holes in its seven-inch casing rather than perforating the casing with conventional perforating guns.
After hydro-jetting the holes, the operator wanted to gain more information on the sand hydro-jetted holes, including the depth control precision, the size of the holes, the effective penetration and the elliptical nature of the holes.
The operator decided a downhole camera with the ability to view to the side would be the best tool to evaluate the conditions and brought in Expro with its ViewMax camera to assess the results. The camera inspection revealed that, in fact, there were three holes sand-blasted in a single plane. The holes were very spherical in nature and placed within six inches or less of where thought to be. The camera allowed the operator to partially look into the holes and examine the unexpected bevelled characteristic of them. It showed, too, that some holes had pieces of coal and/or sand grains blocking them, along with fluid movement into the wellbore.
A downhole camera which can look both down, to the side and rotate 360 degrees brings significant advantages to operators as it allows them to see much more than was possible with a conventional downhole camera. Thus far, it would appear that Aberdeen-headquartered Expro has that market to itself.