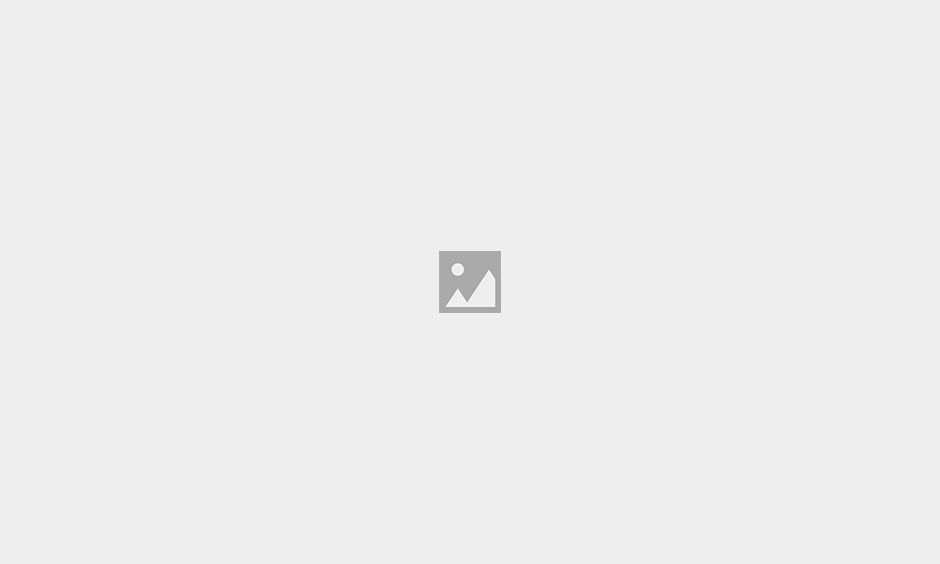
Valhall is a sea of lights and a hive of activity as hook-up operations gather momentum on what is one of the largest offshore brownfield projects ever attempted – anywhere.
While there is nothing in the North Sea that can ever eclipse the progressive rebuild of Ekofisk – a process that seems never-ending, there is a fundamental similarity between the two projects in that the Valhall (operator BP) and Ekofisk (Conoco-Phillips) reservoirs are chalk and are suffering subsidence as they deplete.
To mark Offshore Northern Seas 2010 and the close ties between the UK and Norway, we review Valhall, a major redevelopment that was, in fact, started more than six years ago and designed to extend field life to the middle of the century.
BP’s submission of the field’s redevelopment plan to the Norwegian government in Q1 2007 was considerably later than expected, with the result that the completion date also slipped significantly.
A delay to the submission of the plan for development and operation, or PDO, was due to BP’s decision to have a single lift on the topside of the new platform, rather than several, to increase efficiency.
In a nutshell, the purpose of the by then $2.3billion (NOK 14billion) project was to build a new production/accommodation platform, mothball a proportion of the existing infrastructure pending eventual decommissioning and arrest reservoir subsidence in order to extend field life to 2049.
The redevelopment had been expected to cost in the region of $1.64billion (NOK10billion). The company is coy about the current capex projection, but it is believed to be significantly higher than the $2.3billion figure of early-2007.
Valhall was producing just short of 100,000 barrels of oil equivalent per day at the time the redevelopment plan was submitted.
The field, located on block 2/8 of the Norwegian North Sea, was discovered in 1975 and came onstream in 1982.
It is described as an over-pressured, under-saturated Upper Cretaceous chalk reservoir located in the North Sea about 290km offshore southern Norway in 69m (226ft) of water. The field lies in the most south-western corner of the Norwegian Continental Shelf.
While original oil in place reserves are now estimated at some 3billion barrels, recoverable reserves at the time of the initial development were just 250million barrels. However, more than 500million barrels have now been produced and at least the same amount remains to be recovered. Ultimate recovery could be as high as 2million barrels.
The development by original operator Amoco (the US company was acquired by BP) comprised three platforms, since when two further units have been added. One is the accommodation unit (QP), while the others handle drilling (DP), wellheads (WP), production compression and water injection (PCP), respectively.
These platforms are bridge-connected. In addition, the field has two unmanned flank wellhead platforms, one in the south and one in the north, both about six kilometres from the field centre.
The new platform will take over the functions both of PCP and QP, as well as solids handling on DP. Activities on PCP and QP will cease once PH is in full swing, and the two redundant platforms will eventually be aid up in situ.
Production through DP is expected to continue until the mid-2010s. When it is no longer economic, the wells will be shut in and the platform deactivated.
Plans will then be drawn up for decommissioning these three platforms, or at least that was the original idea. The situation has changed somewhat since then, with life extensions granted for some of the original infrastructure for strategic reasons.
Oil from Valhall is exported by a 38km pipeline from PCP to Ekofisk and gas by a 24km line from WP to the Norpipe line. With the exception of the gas export line, all these lines will be re-routed to PH and remain in use.
PH – the new production and hotel platform – has a design life of 40 years. It is sized for production of about 120,000 barrels of oil and 143million cu ft of gas per day; water handling capability of 200,000bpd; a topsides weight of some 16,000 tonnes, and jacket weighing in at 7,500 tonnes.
It was Aberdeen’s Wood Group – in particular, subsidiaries Mustang Engineering and JP Kenny – together with Stavanger-based Fabricom, that won front-end engineering design work for the redevelopment.
This contract initially focused on design, procurement and project management services. However, it had an option to extend for the full project duration and to include construction management assistance.
The award was a feather in the cap of Wood Group, which also had heavy and highly relevant involvement in BP’s phase one Clair field development located West of Shetland. One result of this experience is that, as with Clair, heavy use has been made of high-grade alloys, duplex stainless steel and titanium. The topsides fabrication contract went to Heerema in The Netherlands while, predictably, the jacket was secured by the Aker Kvaerner (now Aker Solutions) Verdal yard in Norway.
An important aspect of Valhall planning was that it would be powered from the beach in line with Norwegian government policy on emissions. It was Nexans Norway that secured the contract for the high-voltage direct current (HVDC) and fibre-optic cables from the coastal town of Lista to the Valhall field, while ABB secured the HVDC converters, including the onshore station at Lista.
Both pieces of work started out as FEEDs. Options for the engineering, procurement, construction and installation (EPCI) were exercised later.
Taking power from shore replaces offshore gas turbines and the Valhall system is designed to deliver 78 megawatts of power, plus reduce the field’s long-term carbon footprint.
One of the aspects of Valhall that has had to be taken into account is the annual rate of subsidence. It has been as much as 25cm a year, although that rate is said to have moderated.
Like Ekofisk, this has proved a major headache and is a key reason why the existing infrastructure will be gradually phased out over the next several years.
It is for this reason that the new platform now being hooked up was designed with an extra 10m (35ft) clearance. By taking this approach, BP has spared itself the challenge of keeping already ageing installations in acceptable condition. Original infrastructure also took account of a modicum of subsidence at the time, based on what had already happened at Ekofisk.
Maintaining reservoir pressure through water injection is standard practice for enhancing oil recovery but, in the case of a chalk reservoir, it also helps to slow subsidence, at least in the long term. That has, indeed, happened, and the rate of subsidence currently stands around 12cm a year – apparently.
There is a substantial subsea aspect to Valhall and it was Subsea 7 that secured the work package at the heart of which was the procurement, fabrication and engineering of new pipeline infrastructure, with fabrication carried out at the company’s Wester Site at Caithness, including a 238km four-line bundle, which was installed last year.