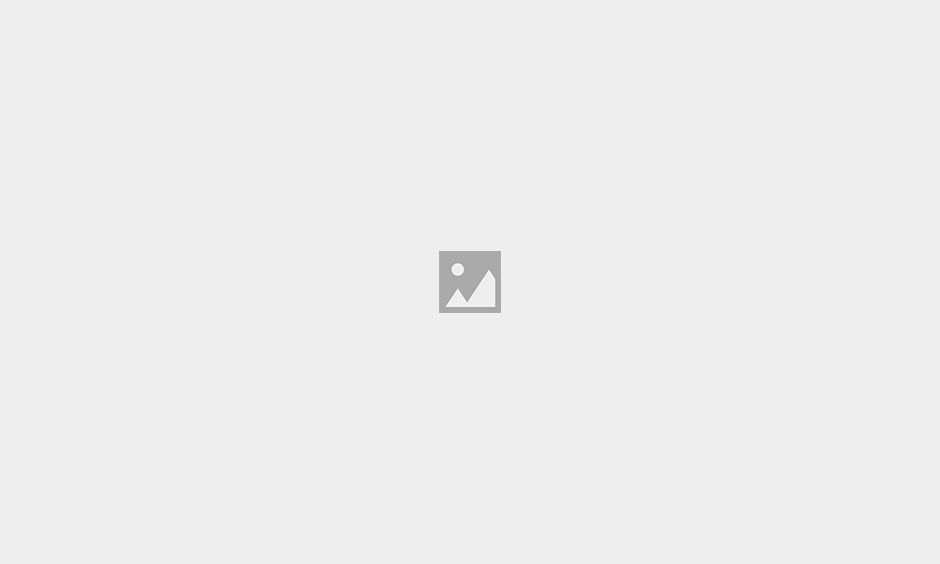
The global population of floating production units is growing rapidly, with Brazil, US Gulf of Mexico and West Africa out in front in terms of their application.
There are currently some 300 FPUs in use today and a further 200 or so are in-build or likely to be ordered over the next four years alone. Most utilise flexible riser systems.
However, one of the greatest challenges associated with this form of production technology is reliability of the risers. They are critical as they transport hydrocarbons from subsea production hardware to the vessel.
No system is foolproof, but a significant problem with flexible risers, to date, is assessing their integrity in situ. How do you do it reliably and in real time?
Just recently, a partnership between Aberdeen SME Flexlife and AGR Field Operations successfully performed the world’s first diverless, non-invasive subsea ultrasonic examination on a number of flexible risers in the North Sea.
The combination of Flexlife’s ultrasonics-based imaging system and AGR’s Neptune pipeline inspection technology enabled a set of six flexible risers to be inspected in real time and a set of high-resolution ultrasonic images to be produced.
The results were recorded using proprietory AGR software and delivered to the client in real time.
Behind the trial is a two-year story. Flexlife was set up by Stuart Mitchell, Carl-Petter Halvorsen and John Marsden in April, 2007, as an engineering consultancy seeking to develop and offer specialist integrity-related services related to oilfield flexibles. And the system just tested in partnership with AGR is the first tangible result of that effort thus far. The decision to team up with AGR Field Solutions – also Aberdeen-based – was made last year.
In essence, Flexlife has come up with an ultrasonic scanning technology capable of “seeing” into the annulus of a riser, so allowing the outer metallic layer (known as armour wires) of flexible risers and flowlines to be imaged in situ.
Annulus flooding/water-related penetration damage, together with armour-wire damage or corrosion, can be detected and assessed anywhere along the length of a riser in real time.
This, in turn, enables the remaining likely life span of individual riser pipes to be calculated and appropriate further inspection and remediation programmes to be worked out.
Flexlife says this marks the first time in the 40-year history of unbonded flexible pipe that this has been achieved.
Breaches of the outer cover (sheath) and consequent flooding of the annulus of a flexible riser or flowline accounts for more than a third of failures. Clearly, pre-emptive surveys of riser systems and seafloor flexibles can reduce the risk of major leakage of hydrocarbons, and the issues that go with.
Flexlife’s team told Energy that they saw a sizeable international market for the scanning system and that it had attracted considerable attention, including from leading lights such as Petrobras, which is the world’s foremost user of floating production units and associated riser systems.
Moreover, the UK’s HSE and its Norwegian counterpart are keenly interested as this is exactly the kind of real-time, non-invasive technology which can have a significant impact on the way such bodies address the policing of riser-integrity issues.
While Flexlife pioneers ultrasonics, Wood Group subsidiary MCS and Aker Solutions offshoot Qserv have carried out what they describe as an innovative pipeline integrity service on the Mutineer and Exeter fields offshore Western Australia for Australian oil&gas major Santos.
The contract marked the first time their vacuum testing technique had been used outside of the North Sea, where it is regarded as a tried and tested technology and has saved operators millions of dollars.
It was following a UK study commissioned in 2001 on the causes of flexible-pipe damage that MCS identified that annulus testing of flexible pipes was a valuable measure in monitoring integrity.
It subsequently joined forces in 2007 with Qserv to develop an advanced range of vacuum testing equipment.