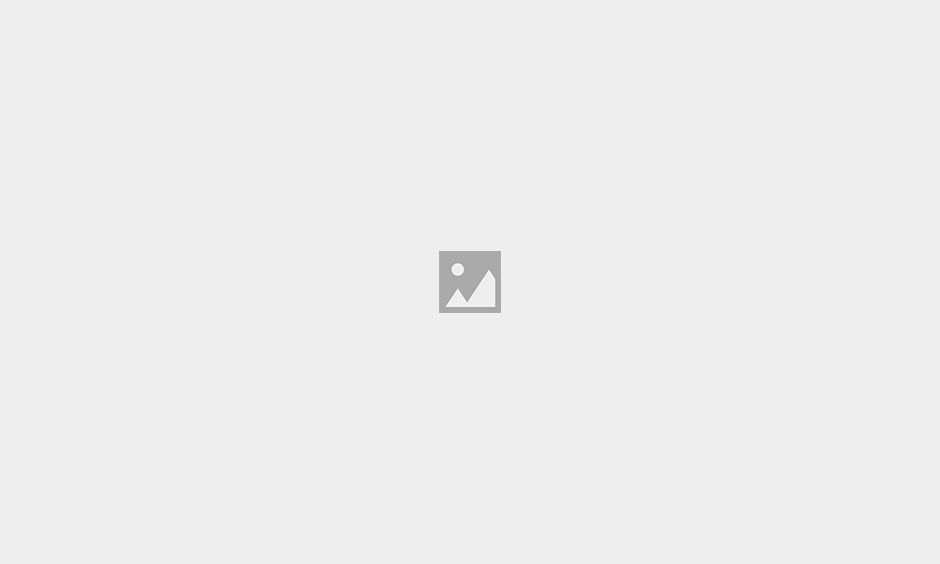
A new method which simplifies drilling operations in unstable formations and thereby saves time and costs has been successfully tested by Statoil on the Brage field.
The Norwegian major says the “liner drilling” solution, developed in co-operation with Baker Hughes, makes it possible to operate with a well liner attached directly to a steerable drillstring.
In conventional drilling, work has to halt while the string is pulled from the well and a liner set to prevent the borehole walls from collapsing. However, setting liner while drilling gets around that problem.
In order to enhance the profitability of mature fields, of which Statoil has many, the company has put a great deal of effort into improving recovery rates, and it turns out that liner drilling can help. It has been applied successfully onshore over the past several years, with Baker Hughes playing a major role in its development and success.
The system that Statoil is working with was “developed in-house” and especially helps overcome the challenges of drilling in zones with lower pressure and difficult shale/coal layers, and in formations with varying flow and pressure regimes.
Normal drilling operations usually run into trouble while drilling from the high-pressure formations into the low-pressure layer. Severe mud losses, with simultaneous hole collapse, kick and stuck pipe are the common result.
The new technology is known in the trade as steerable drilling liner (SDL). It was subjected to extensive testing on land before being tried out in the North Sea on Brage.
After a further test in the Statfjord field this month, Statoil says SDL will be ready for use on other fields.
There are various permutations of SDL now operational or under development, including a coiled tubing-based concept.
Meanwhile, on the other side of the Atlantic, Statoil says it has become the first operator in the US Gulf of Mexico to adopt riserless mud recovery (RMR) technology. This drilling solution reduces discharges to sea and is therefore regarded as environmentally more responsible than alternatives.
The cost of mud itself and the transportation of it to the drillship are also significantly reduced.
RMR has so far been successfully deployed on the Discoverer Americas drillship on the Statoil-operated Krakatoa prospect.
“RMR allows us to circulate the mud, reducing the total mud consumption and discharges to sea to a quarter of the amount compared with conventional methods,” said Tore Grønås, Statoil’s superintendent for the Discoverer Americas drillship.
“In addition, this technology allows us to push the drilling depth deeper for the shallow casing string, which again reduces the overall drilling time per well.
“Minimising the number of casing strings down to the reservoir is crucial for success, especially within deepwater drilling where you may run out of options. With RMR technology, we have the opportunity to reduce the required number of casing strings and thereby reduce the total well cost by several million dollars.”
Statoil currently has two drilling units in operation in the Gulf of Mexico. RMR technology has been used successfully by the company on the Norwegian Continental Shelf in 19 operations so far.
The RMR system has been qualified and field proven down to water depths of 1,525m (5,000ft) and is currently being tested and qualified for use in even deeper waters.
RMR technology is used prior to installing the drilling riser – in other words, at the start of the well.