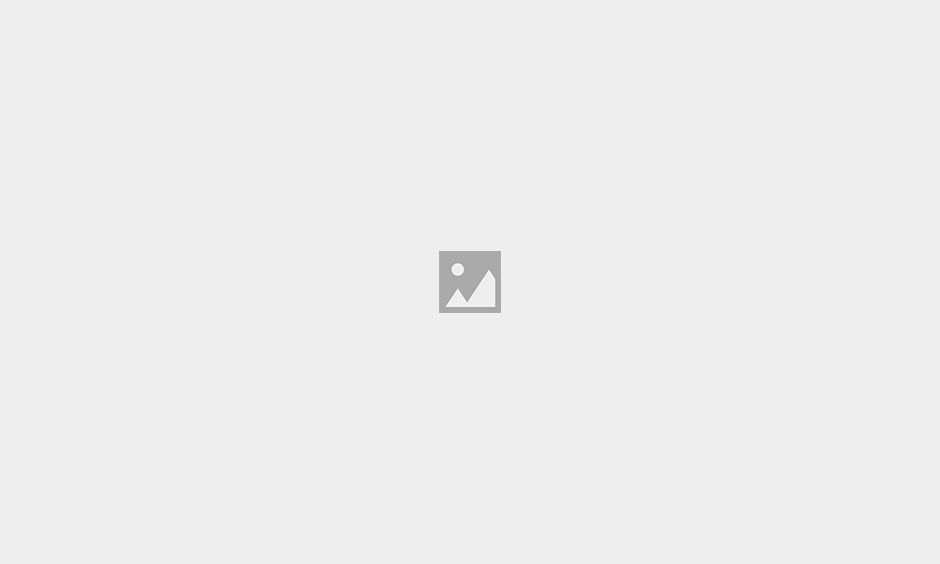
Aberdeenshire company SDS Limited has developed a subsea deployment system (SDS) for installing large subsea structures without a heavy lift vessel (HLV).
The firm’s founders, Arnbjorn Joensen (a naval architect) and David Paul (an engineer), say it offers potential cost savings of 60% on multi-structure installations and up to 80% on single structure installations compared to using a heavy lift vessel.
They say too that it can also instal larger structures in greater water depths in more environmentally hostile locations than is possible with current vessels.
Known as SDS, it is totally different to the Aubin low density gel-in-bag system discussed in the October 2010 issue of Energy.
Joensen and Paul, who set up the company at Westhill in 2008, say their device is “ideally suited” to meet the growing demand for installing larger structures in deeper water.
They claim it:
o Is low cost (OPEX and CAPEX)
o Is low tech and largely failsafe
o Is less weather critical (wave and ice)
o Offers potential to reduce the number of individual structures, tie-ins and interfaces
o Offers the potential for phased installation
o Involves minimal dynamic loading
There are two basic configurations of the submersible SDS concept – U-shaped and square.
The U-shape is a more compact design and typically has greater carrying capacity than the square shape SDV. However, this configuration requires a greater water depth since and structure being carried and positioned would be suspended below the SDV.
The square SDV is designed to accommodate the full footprint of any structure being carried between the hulls and cross/interface beams. This would result in a shallower draught than for the U-shape and would typically be used where there is a limited water depth at the load-out location or along the tow route. However, Joensen and Paul point out that this design has less carrying capacity due to the relative heavy cross / interface beams.
Potential applications cover installation of new offshore infrastructure, decommissioning and salvage. It is could be handled in water depths from 100m to 3,000m.
A typical installation would comprise the following steps:
o Load-out
o Shallow draught surface tow
o Ballasting and trimming
o Deep draught surface tow
o Submerged tow
o Positioning
o Set-down
o Ballasting
o Float-off
Load-out could be accomplished in a variety of ways, depending on the situation and depending on the available equipment and draught.
Load-out options include: direct lift; lift, submerge and float-over; float-over in a dry dock; submerge and float-over using a floating dock or submersible barge; and submerged docking.
Assuming an uneventful tow, once the DSV is in the correct position and orientation the structure being moved will be landed through the use of a system of control chains coupled with ballasting down/deballasting as necessary.