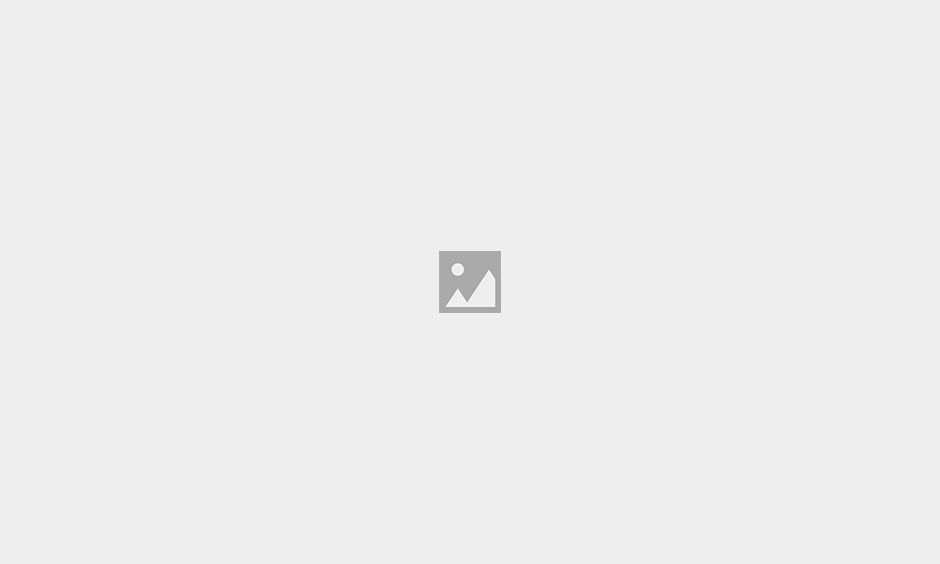
StatoilHydro has teamed up with Chevron and Petrobras to develop a new compact deepwater separation plant for seafloor installation known as Tordis.
Existing technology elements, therefore known quantities in terms of their presumed behaviour, will be assembled in an entirely new way.
StatoilHydro says the new equipment will be far lighter and smaller than the existing solutions. Such equipment is considered key to success in deep waters such as in the Gulf of Mexico and off Brazil, according to Olav Kristiansen, who plays a lead role in the CompactSep JIP project at StatoilHydro’s research and development centre in Trondheim.
Seabed processing allows tasks such as separation, pumping and compression to be performed deepwater rather than on the platforms. Among its various advantages is that water separation is accomplished essentially at the subsea wellhead instead of aboard a platform or floating production unit, thus saving on costs and so forth.
The project aims to develop a plant that will work in water depths down to 2,500-3,000m, which is where a number of apparently spectacular hydrocarbon discoveries have been made.
Traditional separators are too heavy to be lifted down into such deep waters. They will also get a bulky wall thickness due to great external pressure. Reducing the weight and dimensions is crucial.
Initially, under the JIP, the partners will build a three-metre high by six-metre long demonstration rig for extensive laboratory and function tests using model fluids and real fluids, both under low and high pressure.
Kristiansen says the first tests will take place in StatoilHydro’s research and development laboratory in Trondheim.
The entire separation system will then be tested in a high-pressure rig at the SINTEF research foundation in Norway, where larger high-pressure facilities exist.
Then, StatoilHydro’s research and development centre in Porsgrunn will step into the frame. Full-scale testing of the plant using real gas and oil type will be performed here. Parts of the system will, at the same time, be tested with well stream on the Gullfaks C platform in the North Sea.
The research project is managed and performed by StatoilHydro as a joint industry project (JIP) with the three companies as equal partners. The contract is based on the existing technology co-operation agreement recently signed with Petrobras and Chevron. The project, with a current cost limit of some £5million ($10million) will run until 2011.
The project takes its name from the existing Norwegian North Sea Tordis field, where a full-scale separation facility has enabled an increase in oil recovery by 55%, according to StatoilHydro, adding 35million barrels to recoverable reserves.
Tordis IOR entails:
Platform modifications on the Gullfaks C platform in order to change to low-pressure production were made in phase 1. Increasing the oil recovery by some 16million barrels, this phase was implemented in 2006.
Phase 2 comprises the subsea separation station. Installed in 2007, it is the world’s first commercially operated subsea processing system. It measures 19m high by 40m long by 25m breadth. Its subsea template weighs 1,250 tonnes.
Located in the Tampen area west of Bergen, Tordis came onstream in 1994 and was later retrofitted with the full-scale IOR system that is now the subject of the new miniaturisation joint industry project.