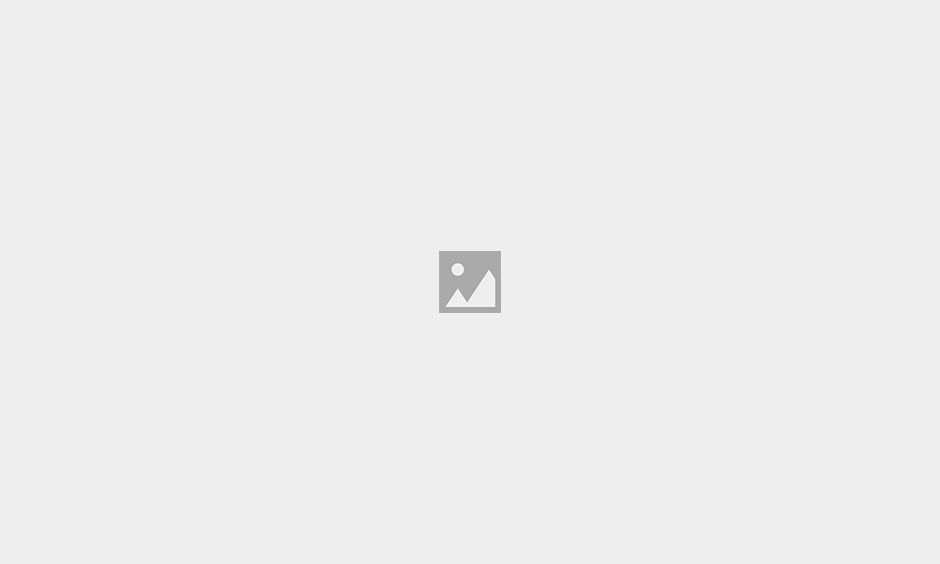
Transocean, owner of the destroyed semi-submersible drilling unit, Deepwater Horizon, had safety problems on at least three out of 14 or so other rigs working in the Gulf of Mexico, according to reportage in The New York Times.
Moreover, Transocean was sufficiently worried to commission risk-management specialist Lloyd’s Register to investigate the safety culture of its North American operations just a month before the disaster in April this year.
According to the NYT, Lloyd’s Register examined the safety culture aboard the Deepwater Horizon, Development Driller II, Marianas and Discoverer Clear Leader, plus at Transocean’s HQ in Houston.
The review was commissioned in response to “a series of serious accidents and near hits within the global organisation”, according to the NYT.
Among LR findings disclosed by the “Grey Lady” were:
Nearly 40% of workers interviewed on the four rigs said that past problems were typically investigated by company officials strictly to attribute blame.
Some 43% of workers on the four rigs expressed fears of reprisals for reporting problems, with about 54% of Deepwater Horizon workers citing such fears.
Various claimed the company was systematically deferring maintenance to save money.
LR’s investigators visited the four rigs in March and apparently concluded that many crew members and front-line supervisors were too readily promoted without sufficient on-the-job experience to appreciate hazards.
Documents obtained by the NYT also point to possible reasons for the Deepwater Horizon’s sinking following the April 20 explosion.
They are said to indicate problems with the Deepwater Horizon’s ballast system, which was responsible for keeping the rig afloat and stable. Had the semi-submersible survived the fire, the oil spill might have been less serious.
Further, the NYT said the documents also show the severity of the maintenance issues that allegedly plagued the Deepwater Horizon, and indicate that Transocean personnel knew what their consequences could be.
LR’s team identified at least 36 pieces of equipment in poor repair on the Deepwater Horizon that “may lead to loss of life, serious injury or environmental damage as a result of inadequate use and/or failure of equipment”. They also refer to an inspection of Deepwater Horizon that was conducted just before the disaster which found various problems with hydraulic relays that controlled the rig’s watertight doors, two of which had to be opened and closed by hand, the NYT reported. BP used Development Driller II to drill one of the two Macondo relief wells near the Deepwater Horizon site, while Discoverer Clear Leader was used for oil containment.
In a statement issued to Energy, LR said: “The reports in question (quoted in the NY Times on July, 21, 23 and August 4), produced by Lloyd’s Register EMEA and ModuSpec USA, were commissioned by Transocean in November 2009 and March 2010, respectively, to proactively understand their safety culture and assess the equipment on the Deepwater Horizon. They are confidential documents.
“We are co-operating fully with Senator Lautenberg’s US Senate subcommittee investigation and other official inquiries and will be explaining the content and the context of those reports in due course.
“We are unable to make any further comments, which could prejudice these investigations.”
Another piece of work commissioned by LR, and also carried out by ModuSpec but in partnership with the Athens Group, reveals major problems with the commissioning of new rigs.
The report, The State of NPT on High-Specification Offshore Assets, found that more attention to the commissioning stage and more resources allocated to training were the primary opportunities to reduce non-productive time on rigs in the late stages of construction and commissioning.
Key findings regarding the impact of NPT include:
Delays to the departure of newly built rigs from their builders cost between $12.2million and $73.6million for every rig delayed, based on an average day rate of $400,000.
Operating, “go live”, date delays cost survey operators between $48.4million and $2.4billion (based on $80 per barrel multiplied by output capacity multiplied by delay duration).
In 2009, the average annual cost of NPT for almost half (46%) of respondents was $26million to $125million.
As for the causes of NPT, the report cites:
Construction yards lack the experienced personnel to fulfil responsibilities under the turnkey model (the report cited the five major offshore yards, which went unnamed but are thought to all be located in the Far East).
Some 79% do not believe the yards did a better job of commissioning topsides in 2009 than in 2008, but 21% think they got worse.
In 2009, the four major shipyards delivered a total of 15 new-generation drillships and semi-submersibles. Unfortunately, the increased number of deliveries did not translate into better quality because the shipyards did not have enough qualified personnel to effectively determine whether or not quality equipment had been received, whether the equipment was installed properly, or to reliably integrate the highly automated systems.
Taking back control of commissioning was the number-one priority of drilling contractors and operators. However, crews were found to lack the right skill sets and/or had received inadequate training.
There were difficulties in recruiting, training and retaining qualified personnel to perform topsides risk-management, risk mitigation and problem-solving.
Dissatisfied with the quality and effectiveness of final commissioning for well control, drilling and mud systems in 2009, the report says drilling contractors and operators took remedial action over and above what was defined in the EPC (engineering, procurement and construction) contracts.
The majority, 63%, employed greater oversight, but 31% went even further: 19% left commissioning out of the shipyard contract and budget entirely and 12% performed a second commissioning process after delivery – at an additional cost, of course.
“Through this report, the industry has clearly identified the causes and costs of non-productive time for their high-specification offshore assets,” said Richard Sadler, CEO of Lloyd’s Register, on a visit to the Offshore Northern Seas show in Stavanger last month.
“Drilling in deep water is clearly a challenge.
“It is likely to become even more challenging as new shipyards enter the offshore construction market – diluting the skills of the workforce – as the technology becomes ever more complex, and as we venture into increasingly hostile environs to recover the remaining energy reserves.”