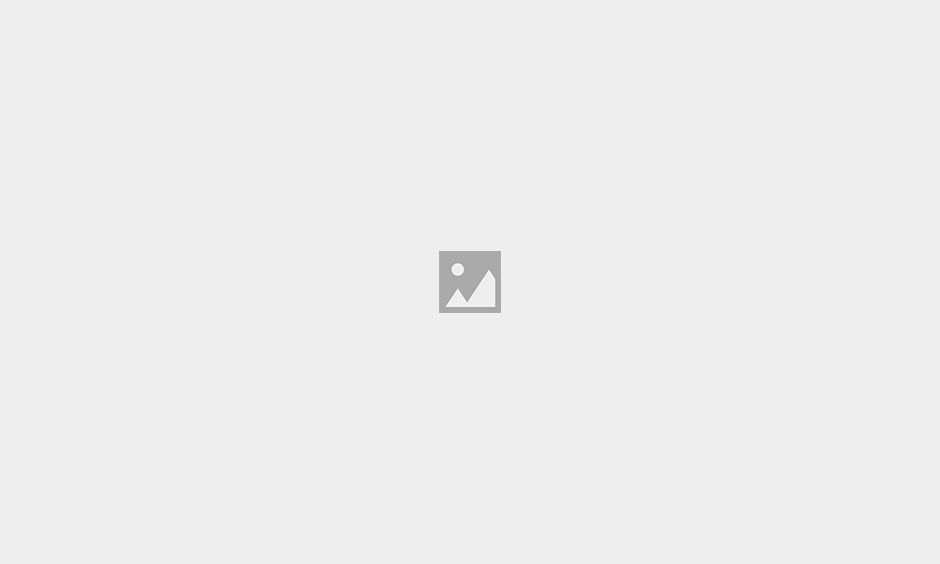
“If we knew what we know, how much more successful could we be?”
This was the famous knowledge management mantra of the 1990s. In a sentence, it focused minds on the huge opportunities that companies were missing in failing to harness their own latent knowledge to dramatically boost growth and profitability.
The intervening years have seen some of the larger oil & gas companies successfully adopt knowledge management concepts and solutions.
Chief among them are Schlumberger and Shell, regularly identified by the Most Advanced Knowledge Enterprise (MAKE) – a panel of global Fortune 500 senior executives and leading knowledge management experts – as leaders in the field.
Furthermore, MAKE’s 2010 final 50 featured a considerably higher number of oil & gas companies than previous years, demonstrating a positive trend of increasing knowledge management within the industry.
However, the challenges facing the sector – both new and existing – have created an environment where it would be advantageous, perhaps even necessary, for companies in the wider oil & gas sector to embrace knowledge management practices if they are to grow their businesses.
The list of obstacles is a long one, featuring as it does meeting regulatory and environmental standards, managing increasingly complex engineering solutions and maintaining margins in the face of increased competition, to highlight but a few.
Knowledge management can assist in tackling these issues, but before its benefits are outlined and its implementation discussed, it is essential to first explain what it is.
There are, in essence, five main aspects to knowledge management: creation, collection, storage, dissemination and application, plus the effective management of knowledge that is outdated and superseded over time.
It has significantly evolved since first being identified as a discipline in 1991, and is now more focused on enabling highly skilled and experienced employees to easily collaborate on current issues and projects via knowledge management systems, rather than just being an exercise in capturing and embedding the use of corporate knowledge.
The wider the network of individuals that can be linked in to collaborate on issues, the faster resolutions and solutions are developed and disseminated across an organisation.
The most obvious benefit of implementing such a system is that it brings talent and information together to improve innovation, while developing new ways of working more efficiently, effectively and safely.
There cannot be many, if any, oil & gas companies that have not placed these objectives high on their corporate agendas.
A number of other key benefits can also be identified, including:
Better service to customers: information dissemination and feedback creates better and more responsive services
Higher quality: codified technical know-how ensures a higher quality product or service is continually delivered
Learning and development: forums and tools that encourage employees to learn and develop new skills and competencies
Increased efficiency: knowledge required to deliver in the most efficient way is captured, optimised and reused
Better operational risk management: through ensuring staff always have access to, and make use of, the most up-to-date information
Returning to the MAKE final 50 list, trends would suggest that more engineering and technology companies are beginning to adopt knowledge management practices.
There are a number of reasons that could be suggested for this, but the two that stand out would be the increasingly complex nature of manufactured products and the move by many manufacturing organisations towards delivering complimentary consultancy and engineering services around their products.
The move by manufacturers into the service arena – where there are increasing opportunities to build long-term relationships with clients, delivering higher margins and providing a cushion against commoditised pricing – is reliant on the ability to effectively deploy an organisation’s corporate knowledge.
For example, successful manufacturers, such as Rolls-Royce, are increasingly focusing on the delivery of service in addition to the basic product.
Clear parallels can be drawn with the oil & gas industry. The challenges facing the sector’s exploration and production segments demand innovative applications of engineering products. The know-how and services that wrap around these products will give companies the edge over more product-focused competitors.
Staying with innovation, studies conducted by the American Productivity & Quality Center show that best-practice organisations use knowledge management to become more efficient innovators.
While knowledge sharing in itself may not lead to significant innovation, it does make the sharing of ideas and insights more efficient, enables people to find the information and content they need and hence accelerates the innovation process. Less time is spent relearning what others across the organisation already know and more time is freed up for creative individual and collaborative problem solving.
The key to achieving a pragmatic knowledge management solution lies in the development and implementation of a simple, yet comprehensive framework. The framework must address the people, information and technology elements across all parts of the organisation.
This need not be overly complex as the framework by its very nature should be able to flex to meet each part’s needs, while retaining a common core that supports common knowledge management practices.
Good knowledge management is about people easily utilising, generating and contributing information via relevant processes, using simple, yet powerful technology solutions.
Whilst the challenge is not purely a technology one, a core knowledge platform is required with an easy to use and secure means of access, providing services such as search facilities, collaboration capabilities, taxonomy (knowledge asset classification) management and content management to store the underlying knowledge assets.
All the major technology vendors sell solutions that can be combined to deliver knowledge management solutions and, in addition, there are numerous third-party products that can be used.
The key point is having a clear view of what types of knowledge management technology components are required, how these will support the overall process, the roles of the users across the organisation and hence the overall framework.
For example, how will users access the solution, what types of knowledge will be stored, how will users collaborate and how will knowledge assets be maintained?
A key challenge faced by growing and geographically dispersed companies is identifying who is best placed to contribute and provide the mechanism for them to do so. Additionally, teams of individuals come together over the lifetimes of projects and contracts. Having a solution that can respond to this is an important consideration.
A good example of this is ensuring that new team members know how to access not just the current explicit knowledge of a project or contract, but also the tacit knowledge that exists within everyone in that project or contract team.
Social networking extensions to knowledge management solutions will help to answer the “who knows or is likely to know what” question and can be invaluable for “on-boarding” and maximising the value from new team members.
Enabling the building of horizontal networks across organisations, from the perspective of specific project or contract teams or more broadly through “communities of practice”, will accelerate and more comprehensively leverage an organisation’s knowledge.
It will also help engagement with extended networks within an organisation, build broader networks more quickly, effectively solve problems, create solutions and identify risk.
In essence, knowledge management is primarily a culture-change challenge. It is getting people to submit what they know, allowing others to easily access and reuse it, and enabling collaboration to further develop it.
When it’s implemented in the right way, there is no doubting the fact that it can make a very significant improvement to the long-term development, sustainability and profitability of a business.
Andrew Deane is a director in Ernst & Young’s advisory practice
Recommended for you
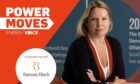