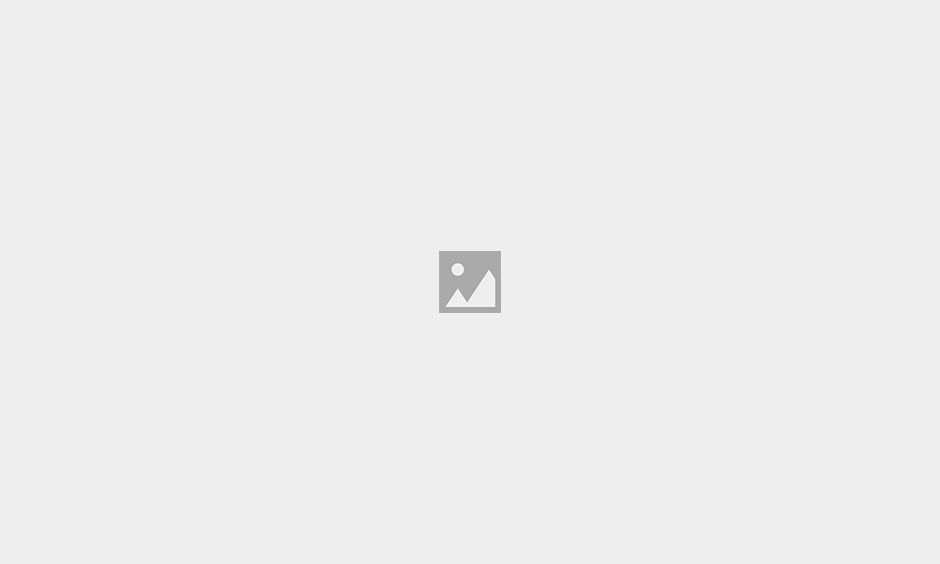
It’s a sobering fact that if you lose your hearing it’s gone for good – time and quiet won’t bring it back. Regardless of your age, if your working environment has dangerous levels of noise, you are in danger of permanently damaging your hearing.
That’s the bad news, but the good news is that measures can be taken to minimise noise damage offshore. Employers don’t want to risk losing their workers and legislation is in place to enforce the control of noise at work.
The Control of Noise at Work Regulations 2005 (the Noise Regulations) aim to make sure that workers’ hearing is protected from excessive noise at work that could lead to hearing damage or to experience permanent ringing in the ears, known as tinnitus.
This legislation stipulates that companies must undertake health surveillance. Not doing so is both illegal and it leaves companies wide open to prosecution should an employee suffer from any work-related health problems.
At places of work where there is more than one employer involved – such as offshore installations – each of those employers will have a responsibility to look after their own employees.
As you might expect, the UK Noise at Work regulations cover a number of work procedures. These regulations reduce the levels of acceptable noise in the workplace and places greater emphasis on audiometry, which checks the hearing of all employees.
This meant major changes to employers as they needed to look at measures to reduce noise overall, as well as sending their exposed workers for hearing surveillance.
The Control of Noise at Work Regulations 2005 allowed employers three years to start implementing its regulations – and the three years were up at the end of December, 2008. So it’s more important than ever that companies implement their programmes to measure and control noise risks at work.
This starts with risk assessment, which will identify noise hazards. The risk then needs to be controlled – where the most obvious solution is to eliminate the risk altogether, but obviously this isn’t always possible.
Lesser methods include substituting it for something less harmful, shielding, enclosure of the process, ventilation or personal protective equipment. Systems of work, job rotation, limiting the number of exposed people and training can all also reduce health risks.
Actions taken can be simple and not costly if the identified noise risks are low, but where risks are high, they need to be managed by a prioritised noise-control action plan.
Where necessary, hearing protection needs to be provided and used. Any other controls should be properly used, and information, training and health surveillance should be provided. Reviews need to be carried out if changes are made that could affect noise exposure.
Companies must be able to prove that risks have been controlled, which is why health surveillance is essential to ensure that any possible damage to workers is picked up. It must be undertaken using a qualified professional; everything must be recorded, and the process must be repeated at regular intervals. The Control of Noise at Work Regulations 2005 state that health surveillance is required for all employees regularly exposed above the upper exposure action values detailed within the regulations.
Health surveillance to check levels of hearing is undertaken using audiometry. The assessment consists of completing a questionnaire, which asks the employee about any past or current problems associated with hearing. An examination of the ear is carried out to check the condition of the ear canal prior to audiometry.
A hearing test is carried out with the employee seated in a soundproof booth (or, if the test is carried out externally, a quiet room). Headphones are placed over the ears and the person is asked to listen for the quietest sound they can hear over a series of different frequencies, at differing decibel levels. They are asked to respond to the various sounds by pressing a button to let the examiner know that they have heard each presenting sound. A graph is produced from which the results are gathered. The results are categorised and regular and timely reviews are carried out as necessary.
The categories are as follows:
Category 1: normal hearing – acceptable hearing ability.
Category 2: warning level – mild impairment.
Category 3 or unilateral hearing loss (UHL): poor hearing. UHL is where the hearing level in one ear is significantly lower than the other ear.
Category 4: rapid hearing loss – audiogram is passed to an occupational health physician for further advice.
At all levels, the importance of wearing hearing protection at all times in noisy areas is emphasised.
Health surveillance screening helps to detect early hearing loss in order to allow actions to be taken to prevent further deterioration, and it can be a useful tool to check the effectiveness of measures taken to protect employees’ hearing.
Oil&gas industry employers are working with occupational healthcare providers such as Abermed to protect offshore workers’ hearing.
Craig Anderson is an occupational health adviser at Aberdeen-headquartered Abermed, which specialises in providing medical and occupational health services to the international oil&gas industry. For more details, see www.abermed.com