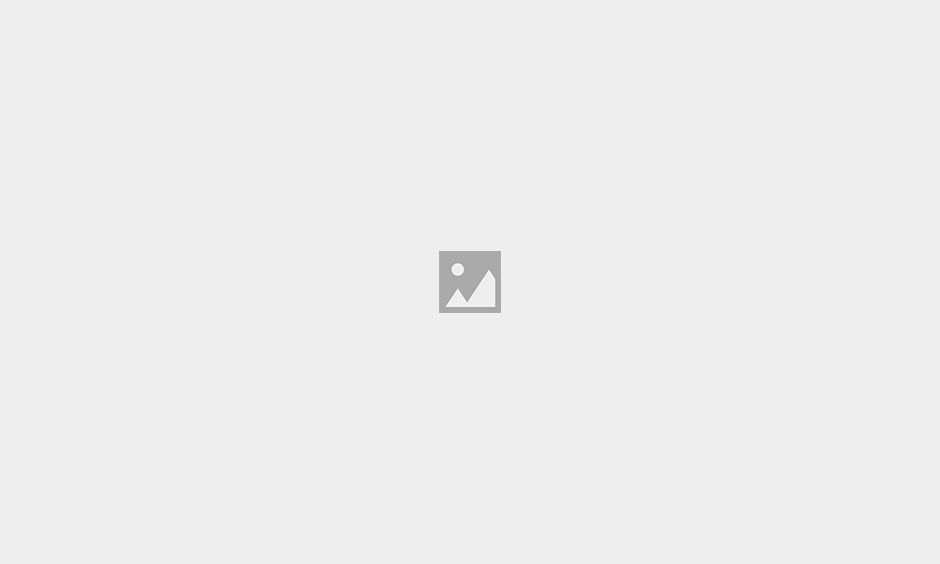
TWMA recycles tens of thousands of tonnes of waste from the drilling industry every year and reclaims many thousands of barrels of oil during the process which are returned to client petroleum companies for reuse.
This is a Scottish company and it is headquartered a Bridge of Don, in Aberdeen, with satellite operations in the UK at Peterhead and Shetland and internationally in Egypt, Nigeria, Norway, the US, Kuala Lumpur, Dubai and Libya.
TWMA says it is the only SME in the world to process cuttings offshore. This is based on its TCC-RotoMill.
A fleet of 10 such units is now operating in the UK and overseas, both on and offshore, using thermal technology to separate oil-based drill mud cuttings into constituent parts of water, oil and solids that can be recycled.
According to TWMA, its system:
Reduces the environmental impact of global oil&gas exploration and its impact on global warming.
Minimises waste.
Helps save marine life.
Removes hazards from hazardous waste streams and recovers oil, water and powder from drill cuttings.
Had processed approximately 50,000 tonnes of cuttings in the North Sea by the end of 2008, with 20,000 tonnes of solids saved from being sent to landfill.
Is recognised by the Department of Energy & Climate Change as “best available technology” for treating drilling waste.
Can process almost any hydrocarbon-contaminated substance.
When used offshore, prevents the need for about 15 crane lifts per cuttings bin, which is equivalent to more than 2,000 crane lifts per well, and associated risk to personnel.
Recovered more than 300 barrels of low-toxicity mineral oil and returned them to a client for reuse in just one project in the North Sea this year, significantly reducing the need for raw materials.
Is the only mobile offshore treatment technology for drill mud cuttings in the world.
A derivative of the RotoMill is the TCC-RotoTruck, which is a fully mobile variant. TWMA says this means the processing technology is can travel to virtually any location required globally by the oil&gas industry, with projects completed in Pakistan and the US, among others.
One aspect of TWMA that stands out is its commitment to research and development. Moreover, in the last year, it hired an environmental team leader with a strong background in environmental protection – including five years with Sepa (Scottish Environment Protection Agency). His name is James Shannon and his brief is to develop new approaches and harness research opportunities appropriate to TWMA’s mission.
As a result, the company is partnering several research projects with the aim of increasing recycling yields and especially finding imaginative applications for the “powders” derived from processing drill cuttings on and offshore.
Indeed, the company is working on a so-called “Interface” project with the University of the West of Scotland to discover potential uses for said powder, such as in the construction industry.
Another significant piece of work is assessing the carbon footprints of processing drill cuttings offshore versus onshore.
Though much talked about, carbon footprinting remains poorly understood both in the home and the corporate world. Companies are gradually being coerced into taking action, largely through legislation and pressure from environmental pressure groups.
The petroleum industry possesses an enormous carbon footprint, though the upstream side of the business claims that its contribution to greenhouse-gas emissions is relatively small; nonetheless, it is being forced to clean up its act, at least in Europe and notably the North Sea.
Significant for the North Sea is how to deal with drill cuttings, whether the result of exploration and appraisal activity or the drilling of production wells, including in-fill boreholes. Tightening regulations – with OSPAR as a powerful catalyst – are pushing the offshore industry towards “zero” discharges, though this may ultimately prove unattainable.
Basically there are two approaches to handling cuttings – process and disposal offshore and transhipping to the beach for cleaning and disposal in landfill.
Each carries a price, but what is that price in carbon terms? TWMA decided to find out through a pilot study carried out this summer by a student working on an Environmental Placement Programme via the Business Environment Partnership.
BEP was established in 1998 to provide free and subsidised assistance with environmental management to small to medium-sized firms throughout Scotland. It places students within Scottish businesses to undertake projects with an environmental focus. In this instance, it was Tracey Elrick, from the Scottish Agricultural College, who did the legwork.
Core aims of the project were to establish the comparative carbon footprint for one of TWMA’s portable TCC-Rotomill units treating drill cuttings on a standard offshore platform versus that of a typical skip and ship-to-shore operation whereby cuttings are transported and treated at an onshore treatment facility – and then to develop a carbon calculator to enable TWMA and its clients to establish the carbon footprint for any well within the North Sea. So what were the findings?
The carbon footprint of a skip-and-ship operation for a standardised well is about two times larger than processing using a mobile unit at source in the North Sea.
However, when like-for-like carbon impacts are removed from the equation, leaving only that which is different, the footprint increases to about 400 times greater for a skip-and-ship operation.
On the basis of modest estimates of cuttings produced on the UKCS annually, if all cuttings were treated offshore, the research suggests the following benefits are possible:
Diversion of 28,000 tonnes of residual powder from landfill.
6,000cu m of oil reused in drilling operations.
6000cu m of recovered water not discharged to foul sewer and thus treated by wastewater treatment plants.
One outcome of the work is that Elrick won the north-east heat of BEP’s competition for the best project but then couldn’t attend the finals because she was away at the time so unfortunately was ruled out of contention. That doesn’t mean that shipping cuttings ashore for cleaning is about to cease – far from it. With that in mind, through the National Industrial Symbiosis Programme (NISP), a Heriot-Watt University student is undertaking project work as part of his/her thesis.
Government-funded NISP aims to work with business to identify sustainable resource management solutions for companies. The project aims to identify potential reuse avenues for the residual powder where cuttings are processed onshore.
TWMA is also working through the Scottish Environmental Technology Network (SETN) to investigate water quality parameters from its Peterhead facility.
SETN aims to improve the competitiveness of Scottish SMEs in the environmental sector, including areas such as contaminated land assessment and remediation, waste management, resource recovery, water and wastewater treatment, sustainable urban drainage systems and environmental management.