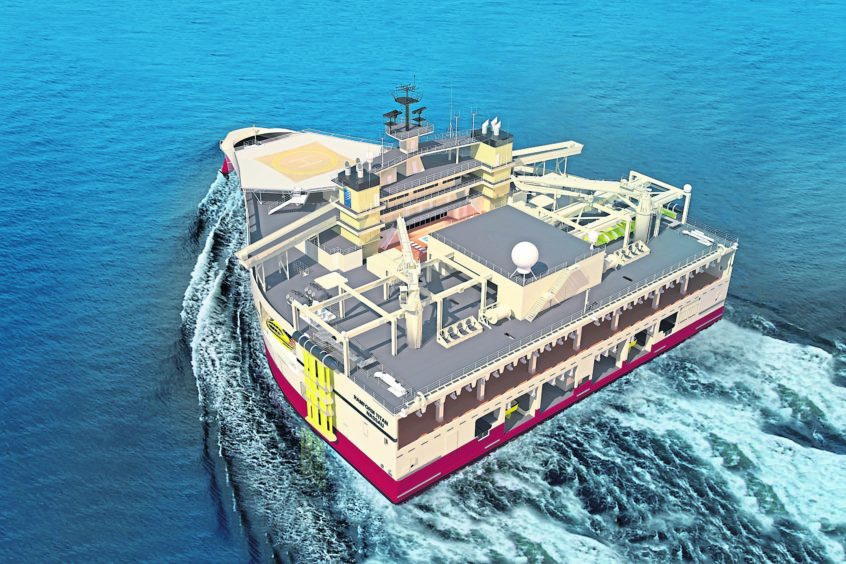
Despite the climate change crisis that threatens to engulf us all, the quest for new hydrocarbon resources goes on relentlessly. One of the key tools in that process is seismic survey – both 2D and 3D.
The technologies used to carry out seismic surveys continue to evolve and the latest big step is the decision by Shearwater GeoServices Holding and Equinor to develop new marine seismic source technology with support from the Research Council of Norway.
The objective is to bring about a step-change in productivity by completing surveys faster and reducing the overall cost and “external impact” of marine seismic acquisition.
Under the agreement reached in May this year, Shearwater will accelerate development of its marine vibratory sources, which provide full control of the emitted wavefield and are therefore fundamentally different from existing techniques.
The “non-impulsive” nature of the technology will bring environmental benefits, especially in sensitive, difficult-to-access areas.
There is growing anger in many parts of the world that classic seismic surveys based on airgun technologies are causing significant damage to marine life.
Klaas Verwer, VP of exploration technologies research at Equinor, said: “This new collaboration offers a great opportunity to develop an efficient source with less sound impact on the environment.”
Shearwater will hold exclusive rights to market the system while Equinor will have preferential access to the technology.
It is a classic Norwegian arrangement where Equinor teams up with a specialist service provider.
The quest for an effective marine vibratory alternative to the airgun has been going on for a considerable number of years.
The idea was apparently first proposed in 1994 and a set of prototype vibrators was built and tested in 1999.
From a geophysical perspective, these tests were regarded a success, but the technology was unreliable and prone to frequent breakdowns.
Then it all went rather quiet.
The project was put into abeyance for a variety of reasons, not least the oil price crash of late 1997 through late 1999 and the fact that large-scale 3D seismic was really only then coming into its own with a large fleet of advanced ships capable of on-board data processing.
Interest in marine vibratory reawakened around 2007 and, in 2013, Houston company Geokinetics claimed a major step forward to the goal of good environmental stewardship with its gear.
But what exactly is a marine vibrator and why might it be a better technology to apply than the airgun?
As the name implies, it is a seismic vibration source that’s used in the water.
In much the same way that Vibroseis trucks – first developed and then trademarked in the 1950s by Conoco – are used to acquire land seismic data, marine vibrators can be used to collect seismic data offshore.
Geokinetics said at the time of its push: “Offshore, where seismic companies acquire ocean bottom and transition zone seismic data, the source of choice for over 50 years has been the airgun.
“Before that, dynamite and other explosive charges were detonated in the water as the energy source.
“The airgun was hailed as a safer and ‘friendlier’ seismic source and was quickly adopted by the industry.
“Now, 50 years later, airguns are beginning to lose their status as an environmentally friendly source.
“A marine vibrator will probably never replace airguns as the energy source for marine seismic acquisition, just as land vibrators have not replaced explosives for land acquisition.
“However, there are a number of situations where a marine vibrator can be advantageous. Some of these advantages relate to environmental concerns, others involve seismic data quality and acquisition efficiency.”
A major difference between airguns and vibrators is the sound pressure transmitted into the water.
It has been likened to comparing a shotgun blast to the hum of an air conditioner.
The shotgun, like the airgun, releases all of its acoustic energy in a single pulse with a very high sound-pressure level, but with a very short duration.
In contrast, marine vibrators have a very low sound-pressure level, but it runs for a relatively long time.
It all sounds good.
However, in December 2017, Norwegian geophysical company PGS, which pioneered the use of the radical Ramform hull-form for seismic vessels, expressed caution.
It asked in a mini-paper why it was that marine vibrators had not yet been adopted for marine seismic surveying.
The company reasoned that it was, in part, because of a perception that their acoustic output was too low to yield useful seismic images and because there had been an unfavourable capital allocation of the upstream oil industry’s collective R&D budget to support development.
It claimed too that the various designs tried out over the past several decades had “suffered from similar flaws: operationally cumbersome, messy and inefficient hydraulic components, and narrow frequency bandwidth”.
But PGS also said that, with increased concern about the environmental impacts of seismic noise, this warranted further research into the benefits of more continuous sources like marine vibrators.
The activity of seismic surveys in areas designated as environmentally sensitive is regulated by a series of established received sound metrics.
These metrics include sound pressure level (SPL) and sound exposure level (SEL); together applicable to both impulsive (air gun) and transient (marine vibrator) acoustic noise types.
According to PGS, specific SPL and SEL thresholds are used to dictate how surveys may operate at various distances from either observed marine mammals, marine parks, commercial fisheries, and so on.
The company has itself been working on the challenge of coming up with something that works efficiently and is commercial for around 20 years, first developing a novel all-electric marine vibrator design in the late-1990s.
This development work led to the design of several vibrator alternatives, including via a joint industry project established in 2014 between ExxonMobil, Shell, Total and PGS.
None have been commercialised yet.
These competing design ideas include large units with relatively small water displacement and smaller units with large water displacement.
Frequency ranges of the emitted source wavefield start low (3-10 Hz) and extend up to several kilohertz.
Not to be outdone, in 2014, BP hooked up with the French company CGG to pursue the development of a vibratory seismic technology, since when there has been silence.
CGG has a good track record on the new seismic front.
Examples include the French group’s BroadSeis-BroadSource technology for true broadband marine seismic imaging and Sercel 508XT designed to drive crew productivity, operating flexibility and data quality to a new level onshore.
Doubtless BP and CGG will talk about the state of play of their collaboration in due course.
Regardless of which collaboration we look at, its seems commercial marine vibratory seismic will remain elusive.
Therefore the airgun will continue to rule everywhere offshore.
Recommended for you
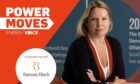