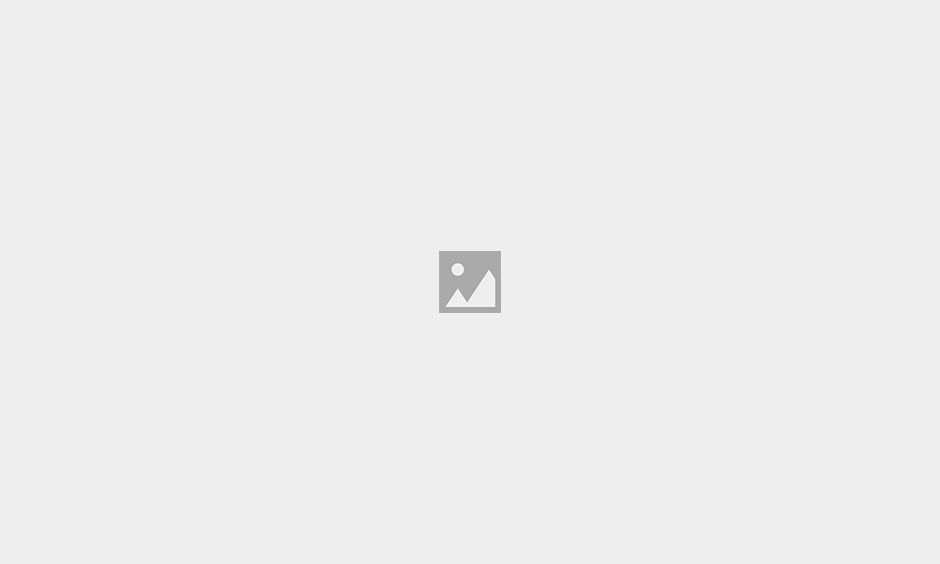
It took 34 years for the in-service fleet of LNG carriers to reach 100 vessels and a further eight years for it to break through the 200-vessel barrier. Now, the 300-ship mark has been reached just over two-and-a-half years later, according to LNG World Shipping.
On December 29, 2008, on its delivery by Samsung Heavy Industries (SHI) to K Line and PT Meratus Line, the 155,000cu m membrane tank vessel, Tangguh Jaya, became the 300th member of the current fleet of gas carriers engaged in the deepsea movement of LNG.
It happens that the 200th ship in the LNG carrier fleet, the 145,000cu m Maersk Qatar, was also delivered by SHI – on April 15, 2006.
Tangguh Jaya is one of a fleet of seven LNG carriers being built in Korea for the carriage of LNG from the new Tangguh LNG export plant in Indonesia’s Papua province for carriage to customers in China, Korea and the west coast of North America.
The seven-ship fleet comprises two 145,700cu m LNG carriers built by Daewoo Shipbuilding & Marine Engineering for Sovcomflot/NYK, two 155,000cu m vessels from Hyundai Heavy Industries for Teekay and three 155,000cu m ships from SHI for K Line. The sisters are being delivered over the period November 2008 through May 2009.
The Tangguh LNG plant is scheduled to start operations Q2 2009.
According to LNG World Shipping, there are a further 89 LNG carriers on order worldwide for delivery through 2011.
However, the pace of LNG carrier ordering has slowed in recent years due to delays in final investment decisions for further new LNG export projects. As a result, the pace of LNG carrier construction that has taken place over the last 30 months is unlikely to be equalled for some considerable time.
It remains to be seen how much damage the deepening global recession will have on the current order book and whether it will lead to further delays and perhaps cancellations.
The global LNG fleet has experienced a period of not only rapid growth, but also change. For example, while Maersk Qatar is powered by a steam turbine propulsion system traditionally favoured by LNG carrier owners, Tangguh Jaya has a dual-fuel diesel-electric propulsion (DFDE) system. The vast majority of conventional size LNG carriers ordered during the past three years have been specified with DFDE systems.
Meanwhile, on the offshore service vessel front, Energy can report that Norwegian company Bergen Oilfield Services (BOS) has relaunched the BOS Angler, which it claims to be the world’s first “geophysical toolbox” vessel.
Bergen says that E&P companies realise that to achieve the best prospect imaging solution, a combination of new and proven existing exploration tools is required. It says it is ahead of the game, both in terms of vessel offering and management approach.
That apparently means not just seismic, but a blend of exploration tools to deliver data and images for exploration success.
As a result of the upgrade, BOS Angler is equipped for multiple streamer surveys and prepared for OBS (ocean bottom survey) and other seabed operations.
The vessel is rated DP II Ice Class survey vessel and, says Bergen, is already attracting interest for work in Arctic and other northern exploration latitudes.
While much OSV construction has migrated to the Far East, development, design and manufacture of propulsion systems has remained fairly much a European game.
This is reflected by Swiss-Swedish power and automation company ABB securing orders totalling $30million for electric propulsion, power-generation and power-distribution systems aimed at maximising the fuel efficiency of a batch of OSVs building in China.
ABB will provide an integrated electric propulsion solution for each of the vessels. The equipment, including generators, switchgear, transformers, drives and motors, will be delivered to the Fujian Mawei Shipyard on the south-east coast of China in 2010 and 2011.
According to the company, electric propulsion systems equipped with variable-speed drives consume significantly less compared with their conventional diesel-mechanical counterparts, and their exhaust emissions are significantly lower. They also allow more flexible use of space on board. The variable-speed drives allow the speed of the ship’s propeller and associated machinery to be controlled with greater precision than more conventional systems, whether diesel-electric or diesel-mechanical.
ABB says this means that the equipment is subject to less stress, and maintenance costs are lower, and that electric motors themselves are highly reliable and virtually maintenance-free.