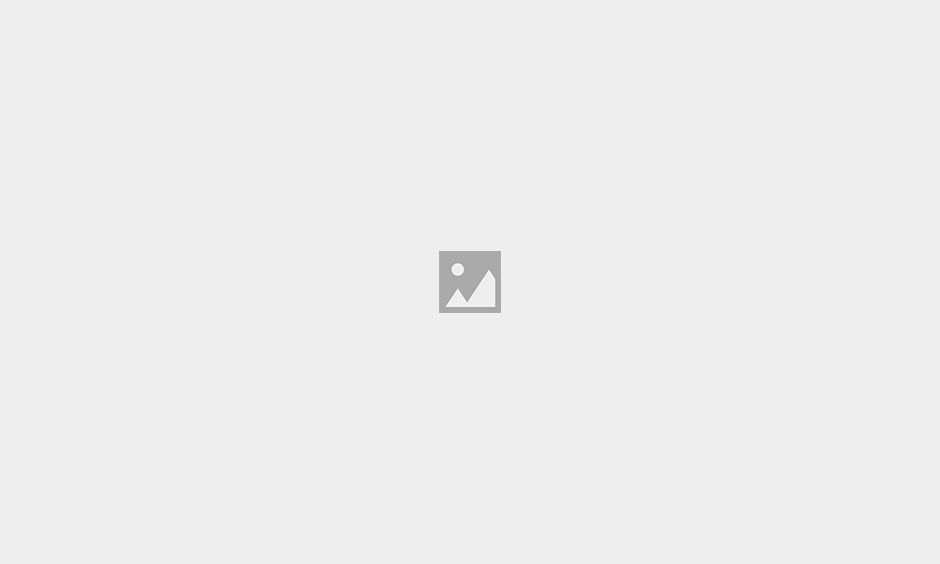
Cyclotech boss Hadfield said: “Every tonne of sand has got to be put through treatment to reduce the number of parts per million (ppm) to the baseline minimum, and you try to use reservoir energy as far as you possibly can to achieve this.
“The biggest issue with sand is that it wears things out very quickly … fills things up and you get corrosion underneath it. So, aside from the environment, there is a huge maintenance issue.”
Hadfield says there is a need for the industry to take a more systematic approach to this nuisance.
“When all is said and done, one should have a very organised approach … generally speaking, they still don’t, although it is recognised as a problem in its own right.”
If sand is a problem on platforms then what are the implications for subsea processing, which is a “holy grail” of the offshore industry?
Hadfield is clear. Sand is a huge issue for subsea processing because getting down to empty separators on the seafloor, for example, is a challenge.
He points out that a jetting technology used by Cyclotech for cleaning out process systems aboard platforms came out of a subsea initiative with Shell, which was then taken upstairs.
“If separators fill up on the seafloor, if injection or export pumps have a sand problem, it becomes a very expensive task to go and maintain.”
Highlighting some of the earlier trials, notably offshore Norway, Hadfield points out that, as built, Troll Pilot’s separation system did not include a sand-handling system.
This is despite the view that the handling of associated sand should be a key feature of subsea separation systems.
“Sand is a huge issue to resolve; you can’t discharge anything on the seabed as you can’t see and measure what it is you are discharging. If you have sand filling up your subsea separator … a big tank on the seabed in the case of Troll Pilot … then what do you do with it?
“You could, first of all, try and inject it back into the reservoir, fraccing formations to receive it, but that requires a lot of power.
“Today, the solution tends to focus on taking out the sand and piping it back to the host facility in such a way that it doesn’t settle in the pipework. But once on the host installation, it’s back to the same issues that one would ordinarily have.
“With the conventional platform, one is talking about at-sea dispersal of produced sand. In the case of Captain, they ship it ashore in containers for final cleaning and disposal. But most in the North Sea clean it and discharge it overboard.”
Hadfield continues: “Even re-injecting produced water requires the removal of sand first otherwise the injection well would get clogged up rapidly.
“So sand appears almost everywhere and is a factor both environmentally and economically. Sand is a big thing and much neglected.”
That said, Hadfield acknowledges that more attention is paid to sand at the project development phase than in the past, so that is a step forward.
“It’s the most complex of all separation issues. People dry gas in their sleep, oil and water separates in a big tank; these days, produced water is cleaned and disposed of in a fairly standardised process, but sand? If you looked at the number of boxes where you could address sand on a topsides flow diagram, you would probably have 30 different boxes all over the place.
“Then there are many different kinds of sand. There are no universal solutions.”
Hadfield’s view is that new-generation North Sea players such as Fairfield and Taqa are taking sand awareness to a new level. Moreover, they want to get moving on contracts within just a few months, and they deal direct.
Use a main contractor tasked with looking after the fields of traditional operators and getting to a contract could take up to 18 months, Hadfield maintains.
“This was not possible historically with the majors. To have a proposal and delivery of goods within the same calendar year used to be unheard of,” said Hadfield, adding that this was encouraging the company to be more service-orientated and less capital equipment-focused, especially out of Aberdeen.