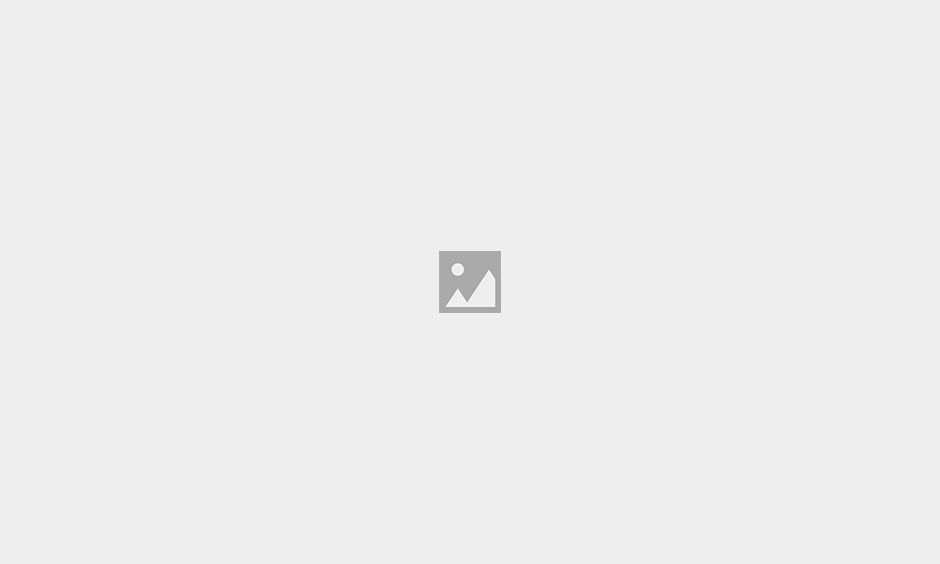
SPECIALIST cutting provider Cutting Underwater Technologies (CUT) has successfully completed a series of tasks as part of the Frigg field decommissioning project.
The Scottish unit of the company carried out work valued at seven figures in several phases on the Frigg DP1 and QP platform jackets for contractor Saipem UK, as well as the DP2 jacket and topsides work on the MCP01 for Aker.
The task was carried out over a number of campaigns in 2007, 2008 and 2009, staged to meet the client’s timeline and support-vessel availability, and required significant investment in bespoke machinery to accomplish the work.
Frigg has proved to be a invaluable experience, both in terms of the firm evolving its equipment and building a track record for future North Sea decommissionings.
In particular, on the final phase of the DP1 jacket dismemberment, CUT used its innovative diamond wire cutting technology to make the 73 separate cuts into the jacket structure. The cuts ranged in size from 24 to 72in and utilised five diamond wire-cutting machines with capacities of up to 74in to complete all the cuts.
The work required the construction of custom-built deployment baskets for the 36in and 50in diamond wire cutting machines (DWCM), adjustable to allow different angles of approach to match the angle applicable to each individual cut.
Extensive trim trials and work-class ROV skid fitment trials were carried out in advance, and the bespoke approach ensured additional accessibility and buoyancy, which delivered reduced cutting times and costs to the client.
Additionally, for Saipem UK, the firm carried out eight cuts as part of the removal of the QP jacket over two mobilisations. Working in some 99m (325ft) of water, CUT sliced through the primary piles (1,372mm outside diameter x 47.3mm wall thickness) as well as the slightly slimmer insert pile.
Each cut was completed using a single wire at an average cut time of 3.6 hours per cut.
CUT UK sales and marketing manager Duncan Griffiths said of the Frigg task: “The versatility of our approach is helping our clients develop innovative solutions to their decommissioning strategies that save time and money while minimising environmental impact.
“Our work for Aker MC was unique in that the DP2 jacket was refloated in one section after buoyancy tanks were fitted to the jacket legs.
“To facilitate the installation of the floatation tanks, two under-driven piles which formed an obstruction were severed. Then, once the tanks had been installed, a further 16 cuts to the corner and inner piles were completed. A standard 64in DWCM was used to carry out all the cuts”.
Besides working in-field, CUT was also awarded the contract to carry out the cutting associated with the piece-by-piece demolition of the jacket at Stord, in Norway.
CUT was formed 10 years ago by Italian parent Tecnospamec and continued success has seen the firm expand rapidly, with operational bases now well established in Norway, the US, Singapore and, most recently, Brazil.
Contractor clients to date include Acergy, Aker Solutions, Allseas, Global Industries, Heerema, Saipem UK, Subsea 7 and Technip.
CUT UK recently moved to a new HQ facility at Aberdeen Science and Energy Park comprising 10,000sq ft of workshops; R&D and test facilities, including a trial and test tank, and 7,000sq ft of office space over two floors.
Besides the North Sea, this facility also services the wider European market, including Mediterranean and Caspian Sea markets, plus Africa, South and Central America and the Middle East.