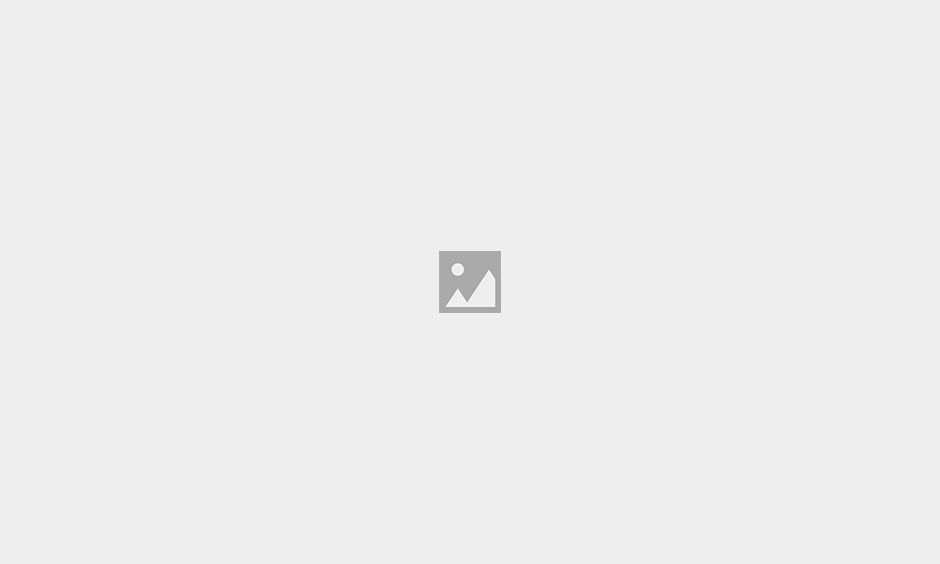
Economic exploitation of stranded reserves often calls for the use of long subsea tie-backs in deep water, but this can present significant challenges with respect to flow assurance and the associated requirements for insulation of pipelines and subsea hardware.
VerdErg, a Guilford-based company specialising in custom engineering of subsea hardware, is examining the potential of a new high-performance material for non-jacketed subsea insulation to tackle this challenge in water depths of up to 3000m (10,000ft).
Subsea insulation options can be broadly divided into pipe-in-pipe and non-jacketed insulation.
Pipe-in-pipe insulation uses low-density material sandwiched between two pipes and provides good insulation performance, but it can be costly to instal and is not suitable for all parts of the subsea system – for example, manifolds, jumpers and other items of hardware require the flexibility of non-jacketed insulation.
Non-jacketed insulation is lighter and cheaper to instal than pipe-in-pipe due to the absence of an outer pipe, but generally uses higher-density materials to provide the strength required to withstand water pressure.
This increased strength is often achieved at the expense of insulation performance.
According to VerdErg’s corporate development officer, Ron Tucker, as the industry moves into ever deeper waters, it is reaching the limits of what can be achieved with pipe-in-pipe insulation.
For example, a major issue with pipe-in-pipe is the weight of the pipe as it is laid: the pipelay vessel holds on to the outer pipe while the inner pipe is hanging within it – the deeper the water, the greater the weight, and this can cause the pipe to become overstressed.
Tucker said: “There is a maximum installation tension that a vessel can handle, and this effectively limits the water depths at which pipe-in-pipe can be installed. Non-jacketed insulation is lighter and easier to instal, but many of the higher-density materials available do not offer the thermal performance required for longer tie-back lengths at greater depths.
“A typical U-value (overall heat-transfer coefficient) for pipe-in-pipe insulation is 0.5W/m2K, whereas for non-jacketed insulation, this is around 2.5W/m2K – this represents a 500% difference in performance between the two techniques. It is the potential for filling this gap in performance that we are investigating with our feasibility study.”
Project partner Aspen Aerogels, a US-based company established in 2001, produces thermal-insulation materials for a range of different industries, including the oil&gas sector.
This company has an “aerogel” material that is currently used for pipe-in-pipe insulation, and the feasibility study, which is supported by the UK’s Industry Technology Facilitator, is looking at the thermal and mechanical properties of the material and its potential for non-jacketed insulation use.
Tucker: “The aerogel material has a proven track record for pipe-in-pipe insulation, but will need some pre-processing in order to make it suitable for non-jacketed application.
“The material will absorb water under high pressure, so we need to form a barrier, and we are also pre-crushing the material to improve mechanical strength.
“Although pre-crushing will affect insulating properties, testing indicates that the crushed material has a thermal conductivity of around 0.030W/mK, so it still performs considerably better than other non-jacketed insulation materials that we are aware of.”
The project is supported by four operating companies, and its funding was secured with help from the Aberdeen-based ITF.
ITF’s operations director, David Liddle, said of the VerdErg work: “Subsea insulation is an important enabling technology for the economic exploitation of many remaining reserves around the world, so it’s great to see work like this being undertaken. The project is focused on the insulation of subsea pipelines and hardware such as valves, connections, trees and manifolds, but may have particular benefits with respect to subsea hardware, so I am looking forward to the results of the study with interest.”