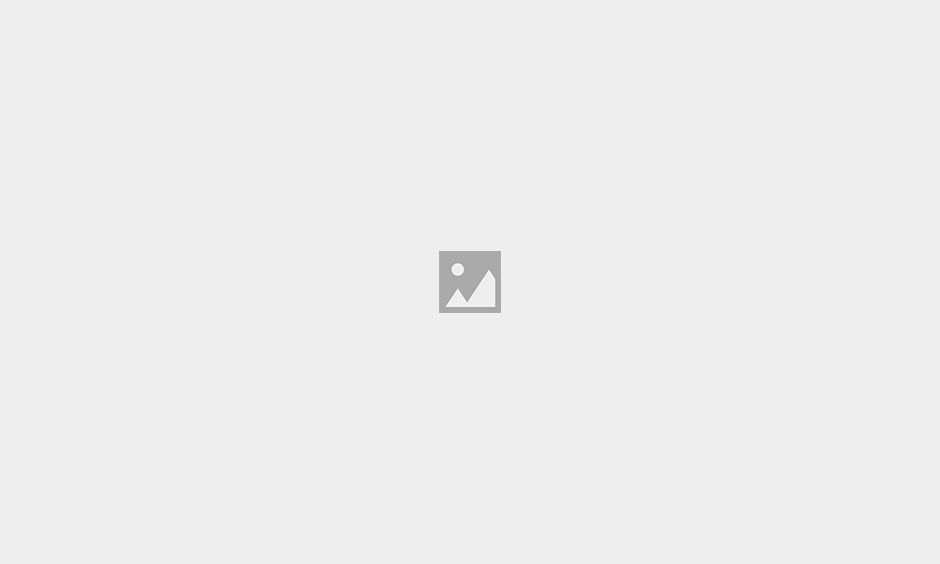
The huge investment of time, effort and more than £4billion over the past four years to reduce the risk of major incidents offshore is producing tangible results.
Figures recently published by the HSE have confirmed that, in the past year, the number of hydrocarbon leaks – a critical measure of asset integrity performance – fell by 20%, to a record low.
The HSE will also shortly publish a report on the progress made by the offshore industry in response to the issues identified in the KP3 report published in October, 2007, which gave the stark warning that “more must be done.”
Work on improving asset integrity and general safety offshore was already under way long before the publication of the report. But, since then, it has been stepped up and refocused, and the industry has united as never before in its bid to make the North Sea the safest place to work in the worldwide oil&gas industry.
Oil & Gas UK was invited to contribute to the progress report and has included evidence of major and measurable improvements in not only physical asset integrity – that is, the state and maintenance of plant and equipment offshore – but also in its efforts to improve leadership, communication and sharing of best practice. That effort has not been slowed by the economic downturn, and when 80 managing directors gathered for a Step Change in Safety leadership day in March, they reaffirmed their commitment to continue to invest directly in safety, asset integrity, skills and training.
They have also acknowledged that “safety is never done” and that the current efforts will continue throughout the life of the industry.
For example, as they begin to overcome the safety-critical asset integrity issues, they are now moving on to also deal with fabric integrity issues, with corrosion being a particular challenge in the rough North Sea environment.
John Forrest is chairman of the Asset Integrity Workgroup of Step Change in Safety, the organisation set up to achieve the vision of making the UK oil&gas industry the safest place to work in the world.
He explained that the industry had made a major effort in the two years before the HSE report and had produced all sorts of guidance and standards, and organised numerous workshops and seminars, but realised that the returns were not as good as they should have been.
“We weren’t using the full capability of what the industry had and realised we had to get all of it working more effectively for us, and while continuing what we were doing before, we have shifted the emphasis,” said Forrest.
That has involved engaging with the entire North Sea workforce, from boardroom level down, and making sure everyone in the industry understands the issues surrounding asset integrity and can play a role in improving it.
“We are encouraging the leaders to get out there more proactively and in a concerted way, acting across the industry, and it has really made a big difference,” Forrest said.
Last year, 25 workshops for managing directors and those who report directly to them were held and were attended by more than 400 senior managers.
However, that has not diminished the effort to engage with the workforce and, last month, more than 100 safety representatives attended a special network meeting to share their experiences and insights, learn from best practice and discuss problems and issues arising across the industry.
A further 200 delegates from across the industry attended a Share Fair which promoted effective collaboration through the sharing of best practice and learning across all industry sectors.
Step Change now has a dedicated workforce engagement work group, and its leadership team has been extended to include representatives from both the RMT and Unite trade unions to ensure that the needs and concerns of the offshore workforce are addressed.
Key to achieving more sharing and learning to attain a consistently high standard across installations has been the introduction of sophisticated monitoring arrangements to provide measurable indicators of performance for safety-critical systems.
“We wanted to try to measure effectively what we are doing, and we have done more of that and are now beginning to see some quite encouraging signs from some of the measurements we have put in place across the industry,” said Forrest.
Step Change in Safety has always worked closely with the HSE and is currently taking steps to address one of its concerns that engineers were not being afforded the authority they merited. To help overcome that situation, site visits by those engineers, accompanied by senior managers, have been initiated industry-wide.
“That does two things,” said Forrest.
“First of all, it reinforces the authority and importance of those individuals, but it also places more emphasis on the technical eyes getting out to site and providing a more rigorous review and audit.
“These are the people who can spot possible problems and deficiencies.”
Looking back at the last two years and the progress made, Forrest added: “The KP3 report was a wake-up call for the industry. We have come a long way since then, but everyone in this industry recognises that there is no room for complacency.
“More needs to be done, and more will be done.”
Recommended for you
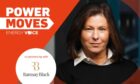