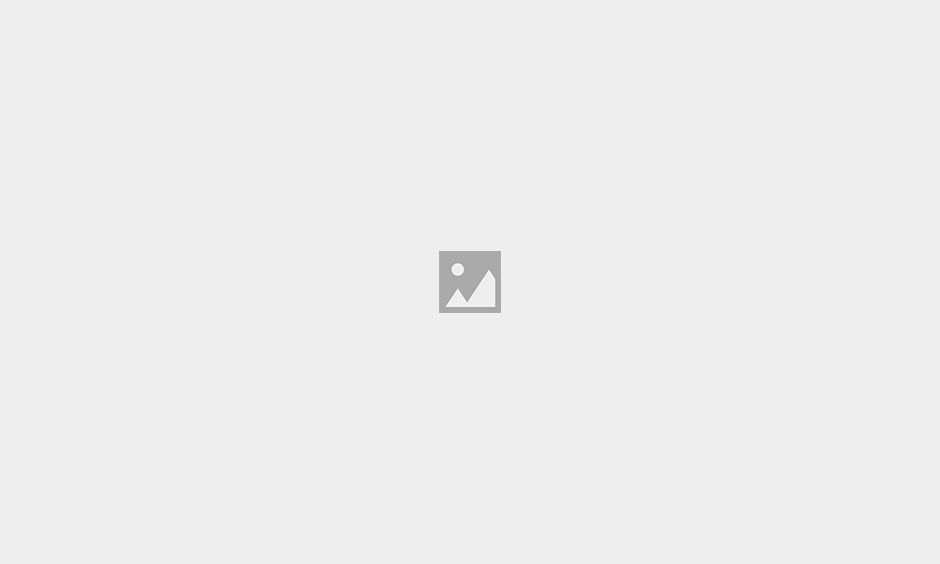
A 34m long blade from SSP-Technology is currently freely suspended inside the Riso Experimental Research Facility for Blade Structure in Denmark.
Since 2008, the blade has been subjected to every form of twisting, turning, pulling, wearing and tearing imaginable. This has led to the development of a completely new test method for improving blade structures and blade design, which combines the loads acting on the blade. The method is already in use in the industry.
Wind turbine manufacturers currently use specially designed wind tunnels, high-calculation capacity computer programs and engineers who, almost before the blade has been designed, are able to predict how it will behave down to the smallest detail.
However, testing the finished full-scale blades in the most realistic way is still essential in order to develop the most reliable and cost-efficient wind turbine blades.
The overall objective of the EU-supported programme, which currently has 10 industry partners, is to jointly develop an experimental platform for testing the blades of the future, as well as to develop new methods that provide designers with reliable tools for achieving the best possible results.
Until now, loads were applied to the blades by casting a clamp around the blade and then subjecting the clamp to vertical and horizontal pulling. However, this does not reproduce the actual loads to which the blade is subjected. Loads that could not be taken into consideration with the old test can now be applied to the blade in a far more realistic way.