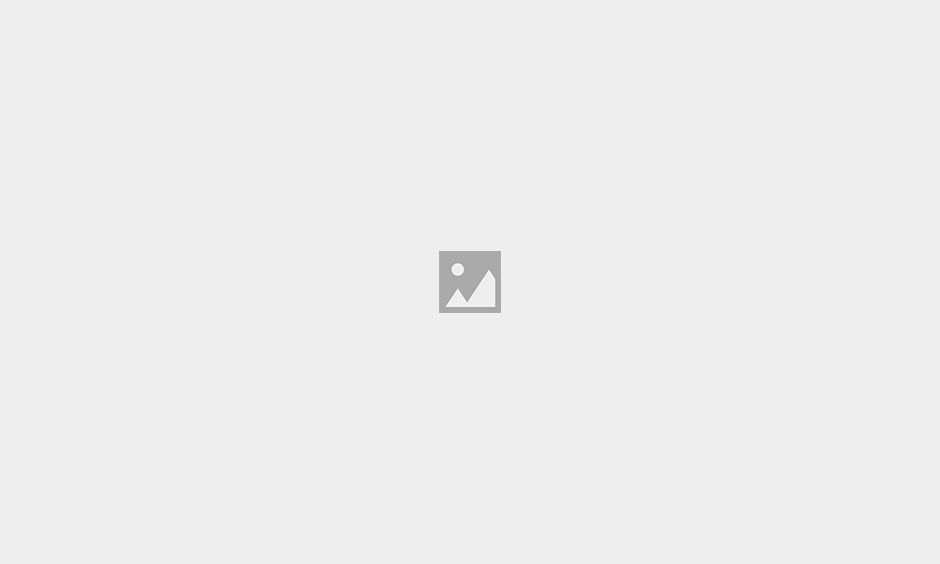
In recent years, we have seen a huge surge in compensation claims from people suffering the painful effects of hand-arm vibration exposure, often dating back many years.
Hand-arm vibration, or vibration white finger, as it was previously known, arises from exposure to vibration, mostly from hand-held power tools.
This is particularly prevalent in the oil&gas, manufacturing and construction industries, with 3,000 new cases identified each year (HSE), and it can cause long-term health problems if it is not properly managed.
Figures from the Health and Safety Executive suggest that about five million workers in the UK are exposed to hand-arm vibration at work, with about two million exposed to levels of vibration which present clear risks of developing debilitating conditions. If companies are to tackle the issue and the threat of potential litigation, it’s vital they know what the risks are and how to manage them, particularly in the wake of the Control of Vibration at Work Regulations 2005. These require employers to take specific action when the daily exposure to vibration reaches a certain level.
Hand-arm vibration is vibration transmitted from work processes into workers’ hands. It can be caused by operating hand-held power tools such as power saws, drills or grinders.
The health problems arising from hand-arm vibration fall into two main areas: sensorineural, through damage to the insulating material around nerves which, in turn, affects nerve signals, and vascular damage, which affects blood flow to the hands.
Early symptoms include tingling, loss of sensation, reduced sensitivity to temperature or blanching. For some people, symptoms might appear after only a few months of exposure, but for others, it may take years. Either way, they’re likely to get worse with continued exposure to high levels of vibration and may become permanent.
My work as an occupational hygienist involves recognising, evaluating and then controlling health hazards arising from work, with the aim of protecting employees’ health and wellbeing and helping employers to control these risks.
We can help companies to reduce the likelihood of litigation by assessing their workplace and helping to resolve potentially dangerous issues such as hand-arm vibration.
Identifying the risk potential involves looking at the acceleration levels of the tools the individual is using. Companies often rely on data from manufacturers to work out the risk, but the older the tools get, the more the vibration increases. Other factors such as temperature and posture also have an impact, with cold and damp conditions increasing the risk.
Since 2005, employers must establish if their employees are likely to be exposed above the daily exposure action value (EAV) and, if so, they need to take action.
The solutions we offer to clients might include simple spreadsheets to help them work out what each individual does in a day and where the risks lie. We can also develop “trigger times” for tools using a simple, effective, traffic-light system approach.
The Control of Vibration at Work regulations also require employers to provide information and training to employees, and they must also carry out health surveillance and checks where there is a risk to health which will detect any damage at an early stage. Failure to comply with the regulations can lead to both civil prosecution by an individual and criminal prosecution by the HSE, which usually results in heavy fines.
For the employee who is left with the effects of hand-arm vibration, it can impact on the rest of their life – making everyday things like driving, using the TV remote control, typing, texting and hobbies such as golf impossible.
It’s therefore essential that companies, particularly those working in oil&gas, construction, research, fabrication, engineering and manufacturing, know their responsibilities and take action now.
The Health and Safety Executive website has some useful information and calculators to help employers work out risks – visit www.hse.gov.uk for details – or contact us at Abermed to discuss how we can help your company.
Julie Zeiler is one of very few qualified and experienced occupational hygienists in the UK. She joined Abermed after a 13-year career in quality, health, safety and environment (QHSE) in the oil&gas industry. For more information, visit www.abermed.com