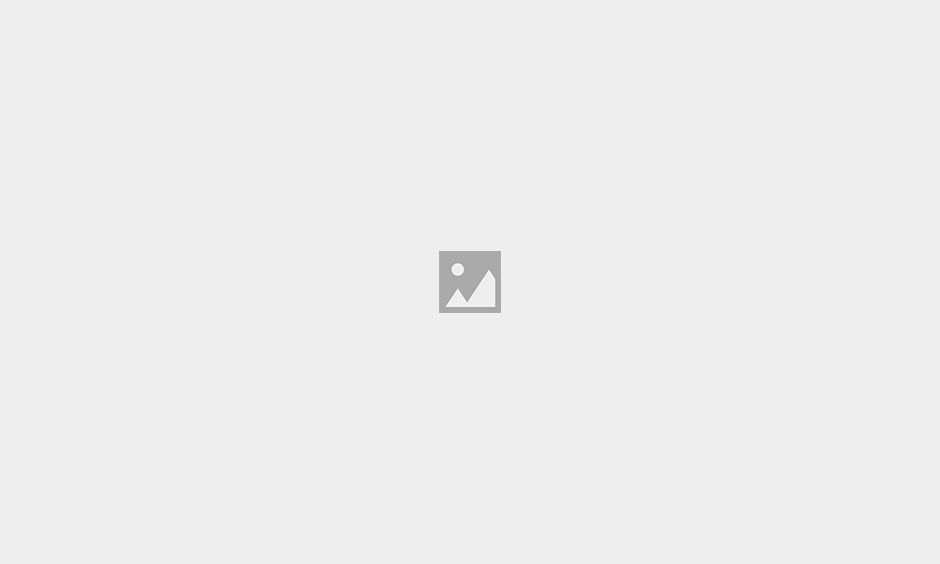
Sand is part and parcel of hydrocarbons production. At best, it is a costly nuisance, but unchecked it is potentially dangerous and must be rigorously managed. But how, as this aspect of production management has traditionally been less of a priority than some others?
Andrew Kinsler, of Aberdeen company Sand Monitoring Services, says sand management is a much-vaunted piece of terminology used in the oil&gas industry, but what does it mean and what use is the practice to operators in the North Sea in particular?
Firstly, sand is defined as “a detrital grain between 0.0625mm and 2mm in diameter” – a hard and abrasive material that is larger than silt but smaller than a granule.
According to Kinsler, it is, therefore, of little surprise that, since 1993, at least 18 dangerous incidents have been directly attributed to produced sand during operations. These occurrences are mainly related to flowline failures, but a significant number are also associated with production vessel and control valve failure.
In addition, sand poses risks through vessel deposition, affecting plant performance, requiring vessel entry to dig out the accumulated sand. Furthermore, sand deposition can decrease corrosion inhibitor efficiency, thereby increasing corrosion/erosion effects.
So what can be done to deal with sand production, especially as we move into a new era of technological challenges?
Kinsler says that this is where sand management comes into play.
Broadly speaking, this covers a wide range of disciplines and services that are subdivided into four areas of specialisation:
Prediction (geo-mechanical studies).
Prevention (sand control, such as sand screens).
Monitoring (such as real-time detection).
Handling (online sand removal from vessels).
Sand management is the process of identifying, evaluating and mitigating against reservoir sand production and its associated problems, bringing together a disparate group of technologies and professionals to find solutions to sanding tendencies.
Kinsler said: “Personally, I would like to see more input from integrity management and corrosion specialists into the ‘sand network’ as the consequences of sand production has a direct impact on their workscope.
“It could be concluded that sand management is all about safety-critical operations and offsetting production against integrity.
“While, historically, this may be the case, if the principles of sand management are used correctly, it can be an active component in the production optimisation process.”
This is where Kinsler says that having a sand management strategy (the documentation relating to the overall sand management philosophy) provides a safe operating envelope in which to increase production via a controlled mechanism of sand risk assessments (SRAs) and active monitoring, including monitoring technology and inspection data.
“An example of the application from the UK Continental Shelf sees operators utilising the sand risk assessments as a prerequisite for the production optimisation group’s drive for production uplift through planned pressure drop programmes. The SRA comprises data inputs from a variety of sources, including current production conditions, ultrasonic thickness (UT) pipe wall thickness measurements, sand probe data and erosion models. The net result of these data inputs is the prediction of sand production and erosion rates at the proposed tubing head pressure (THP).
“Evidently, the SRAs represent a safety-critical feature and provide a go/no go stop point for the operational process. The SRA cannot be issued without each criterion being met and satisfied through due process control. The key element of the SRA is the integration of data into a single process to systematically control operations.”
The role of a specialist such as Kinsler’s company is to take responsibility for the SRA production. On completion of any testing activity, the resultant data is analysed and correlated with production, probe and sampling data.
From these inputs, the level of risk posed from sand production levels at the tested THP is assessed and evaluated. If the substantiated risk level is within accepted values, then the well operating guidelines can be amended to reflect the revised production conditions.
Looking to the latest trends in the sector, the new challenges of deepwater developments, extended-reach drilling, heavy oil and HPHT fields, combined with unconsolidated sands, means solutions are needed – and now.
“It happens that these challenges can be met by a mix of good old traditional engineering, dedication and a modicum of technological input. Enabling a group (or an individual) to facilitate the implementation of sand management will create a focal point that can make a real step-change improvement in safe production uplift. The end benefits of an active sand management process are not necessarily achieved through unique or bespoke processes, but rather through sound engineering practices and the use of a formulaic approach. It is not rocket science, and proper application can save operators a fortune.”