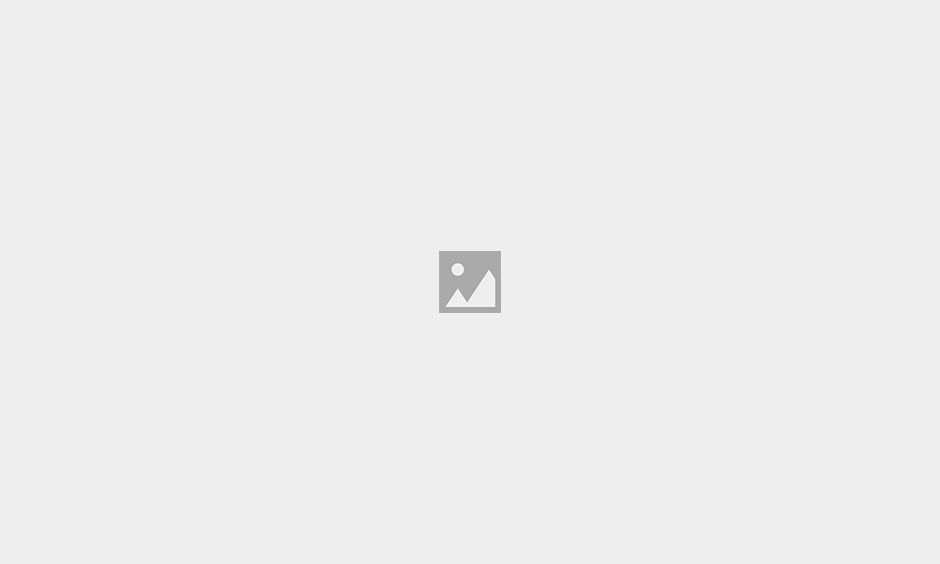
Our review of the offshore wind turbine foundations market has drawn a response from engineer Roger Taylor, of Inverness, who has developed an innovative foundation and foundation installation concept package that has been previously aired in Energy.
Taylor raises issues that he feels the still-infant offshore wind industry does not have a proper grip on – and there are many.
In his view, for example, currently dominant monopile foundations are feasible only in water depths up to 25-30m, supporting turbines of 2-6 megawatts power output.
Moreover, he deems the method of installation to be complex, weather-dependent and expensive.
Adding insult in the context of UK hopes, he reinforces Energy’s view that the construction of piles and the installation work is mostly going abroad.
Over and above that, health-and-safety issues have yet to be fully considered and will become more of an issue if production increases.
Taylor agrees that steel jackets can work for larger turbines in deeper water, but says their cost is prohibitive and that the method of installation is totally weather-dependent throughout the whole supply chain, with serious cost implications.
“Maintenance, health and safety, access, end-of-life removal all add to the cost,” he says.
“If jackets are delivered by pontoon to the North Sea, most of the fabrication work will end up in Poland/Estonia, where construction costs are much cheaper.
“As water depths increase, steel jackets become more impractical, expensive, and will never be produced in sufficient quantity to meet the UK Government’s renewable energy targets by 2020.
“The industry desperately needs new technology which can provide cost-effective foundations, combined with a fully integrated delivery and installation method which is less weather-dependent, requires no heavy lifting on site and provides access to the nacelle/blades for major repairs or turbine renewal.”
Which is where Taylor reckons that the DTI 50 concept – his idea – has a place. Naturally, he is keen to push his idea, but it happens to be one that could turn out to offer considerable benefits over the currently limited offerings identified in the October issue of Energy.
The DTI 50 is a concrete gravity base foundation that Taylor claims would be cost-effective and could be mass produced at several UK sites, not least in the Cromarty Firth at the currently mothballed Nigg facility.
It incorporates a delivery and installation method using custom-built, relatively simple, self-propelled, dynamically-positioned pontoons that could also be built in the UK.
The design is currently being put through proof-of-concept evaluation for possible future deployment with a very large new turbine design that is currently under development.
Taylor says DTI 50 offers a standardised approach to foundations that is capable of supporting the largest turbines and of installation in the deepwater Round Three sites offered by the UK’s Crown Estate.
Taylor insists that DTI 50 offers an “inherently safer construction and installation operation that is less weather-dependent” than currently favoured jackets and monopiles, and has built-in scour protection.
This includes an apparently simple method of raising and lowering the turbine tower on site, allowing access to the turbine nacelle and blades from cranes mounted on the installation pontoon.
Because of the use of concretes similar to those employed in a number of North Sea oil&gas platforms, Taylor points out that DTI 50 offers virtually no maintenance on foundation or main support column.
Decommissioning and repositioning would be relatively easy compared with other current foundation offerings.
Taylor told Energy: “Having built the infrastructure required to mass produce foundations and deliver complete units, costs drop dramatically, with significant savings even over monopiles in shallow water.”