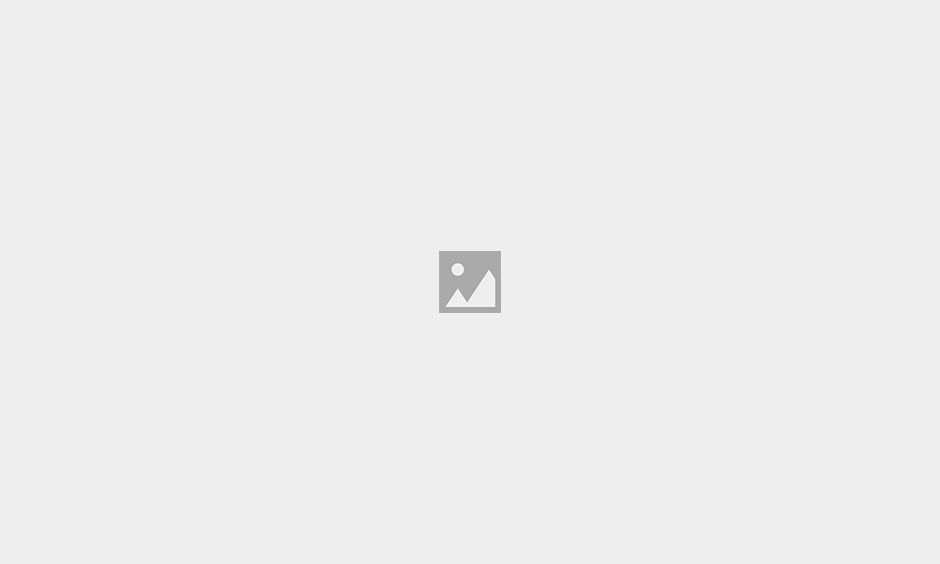
Burntisland Fabrications is the sole surviving active offshore fabrication yard in Scotland geared up to building large structures for the oil&gas industry.
Although the Nigg facility is being used for a variety of oil&gas-related engineering and prototype renewables fabrication projects by Global Energy Group, plus it was used for integration of the Beatrice demonstrator turbines.
But why did BiFab boss John Robertson stick at it and, moreover, lead a successful management buyout of the Fife yard in 2001, given the poor state of the North Sea at that time?
“We’ve always believed in what we can produce; always had a strategy within the company to cover a wide range of products – even in oil&gas – including large fabrication, to jackets, to process modules, to pipework,” he told Energy.
Despite being relatively successful on all chosen fronts, including a decent enough stream of oil&gas-related work, Robertson admits that the current market is hard to predict because of the impacts of recession negating at least some of the stimuli to promote offshore windfarm construction, and rapid cooling of the offshore industry since the oil price collapse from near $150 per barrel to current levels.
Beatrice was the turning point for BiFab in terms of offshore renewables as it provided valuable experience in solving the challenges of turbine jacket development and manufacture.
But then there was a long wait, with offshore wind investment grinding along in bottom gear and eventually clicking into second, and then coming dangerously close to stalling.
But with the first large commercial order for jackets – Ormonde – plus the Alpha Ventus win, the prospect of further orders now that the UK Government has delivered critical stimuli via its 2009 Budget, significant facilities investment and design refinement, BiFab appears ready for the big time.
Work has started on the Ormonde contract, with the first of the jackets scheduled for delivery in May, 2010, with the last loading out in October that year.
With thousands of structures to be planted in the North Sea, Robertson is very clear about the scale of the opportunity.
“We see a possible requirement for around 8,000 structures over five or six years,” he said.
“The tonnage of steel with piles per jacket will be around 800 tonnes.”
That amounts to a massive 6.4million tonnes of business opportunity. And even if he is a million or two tonnes adrift in his sums, Robertson is still signalling a huge opportunity that British companies must grab.
Not to would be stupidity on a grand scale.
“This is a huge opportunity. The alternative energy potential for Scotland and the UK is probably greater than what we have experienced in oil&gas.”
Robertson is right at the front – at least in UK terms – and he’s going for gold. But he has concerns.
“We bought into this in the early days and we’re expanding … operating Burntisland, Methil and Arnish. However, I feel that, despite the work that’s been ongoing to date, and the animation and the ambition to have the best manufacturing facility in Europe, we still struggle to get the message across to Government.
“I thing there is genuinely a misunderstanding at this time of the scale of the potential that’s out there.”
However, there is at least one individual in “the system” who has twigged, and that is Brian Nixon, head of energy at Scottish Enterprise, as he has direct experience of the fabrication sector in a prior life.
Robertson said: “I have a concern that if we don’t move quickly, we’re not going to have the infrastructure in place to maximise the opportunity for the UK.
“If you look at turbines, they’re coming from overseas, blades too. The only opportunity we have at this time is substructures and tower fabrication.
“This threat is real, and even China is getting UK work, with the monopiles for Greater Gabbart having gone to China. Nobody in the UK builds monopiles at this time.
“That makes us the only player at this time with a substructure solution. We’re also playing to our strengths from the oil&gas sector, which is very important. I think Scotland and the UK need to, wherever possible, capitalise on our skills from the oil&gas sector and transfer those to manufacturing for offshore wind.
“The other area where we can be of tremendous benefit is our experience in O&M (operations and maintenance), and that’s probably it for us (UK) – other than maybe increase the breadth of the supply chain and possibly attract turbine assembly into Britain.”
Robertson agrees with the Energy view that the UK could successfully operate about six strategically located offshore wind fabrication and integration facilities.
“Remember, if there are to be 8,000 structures over even 10 years, that’s 800 structures a year. The BiFab proposal only takes us up to 100.”