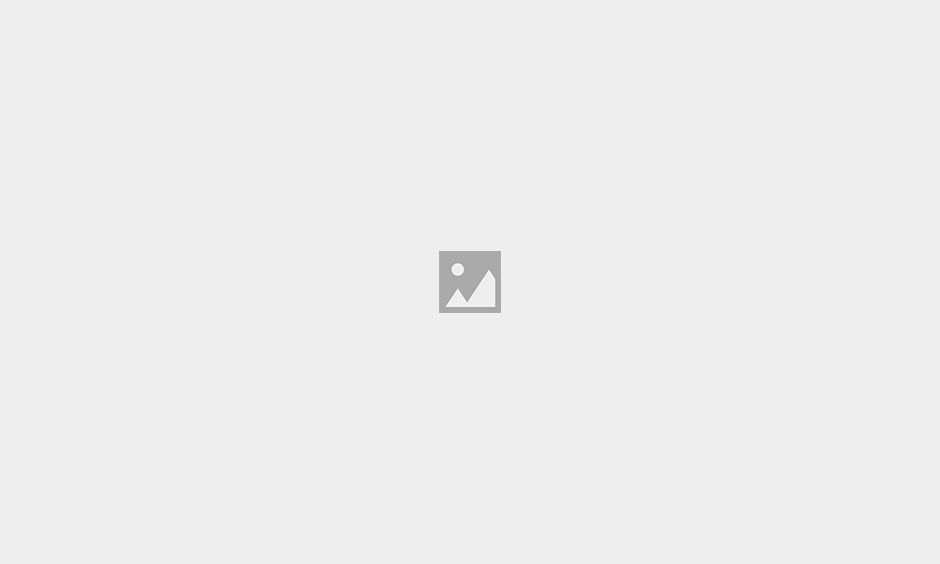
Running a safe business should be a given, but it’s also a tough call, according to Mike Mann, health, safety, environment and quality (HSEQ) director at Aberdeen-headquartered RBG, a mid-sized, upstream oil & gas contractor.
As for attempting to raise the HSEQ, he describes this as a “massive task” for any company, let alone one like RBG that employs hundreds of people.
Mann insists that good HSEQ management is based on common sense.
“We could be awarded all the contracts that are going, but if we don’t operate safely, then the damage that would do to our reputation would have a massive impact and reach clients rather rapidly,” he said.
“It’s even more of a challenge across a business as diverse as RBG, which is national and international with all the cultural issues associated with that. You’re only fooling yourself if you set yourself a minimum standard and then make it suit you.
“The UK industry likes the minimum standard approach, that’s what the industry wants.
“It’s a standard that they will accept in another part of the world.
“But I can’t accept that because, at the end of the day, we won’t be seen as credible to our workforce if we do that, never mind to our client base.
“We need to be true to ourselves and deliver on what we say we’ll deliver. That will be the measure of success to me.”
Mann claims RBG has a very robust business management system, of which HSEQ is part.
It gets audited to ensure compliance against the action management says it is going to take.
“That’s key because all too often people say they have the systems on the shelf or documents in place, but by itself that’s not enough.
“You have to walk the talk.”
According to Mann, a classic example is interface documents.
The UK industry gave itself a pat on the back years ago when it said it had cracked this beast. “The reality is that sometimes they have a very good and robust document, but sometimes they struggle to get that document together as it’s not a true interface.
“It’s what one company wants, and even though they get a good document and the primacy is correct, do they then ensure that they comply with it? The answer on most occasions is almost certainly no, because they don’t properly audit it.
“It’s a document that gets agreed between two companies, but quite often the workforce don’t know the details, nor is it rolled out to a wider audience. Management ticked the box, they think they’ve done it and they don’t do a compliance check against it.
“That’s where you’re not being true to yourself. I think we’ve moved to a place where RBG has a very strong management team who are very focused on and understand the issues attached to being responsible for safety.
“We’re now further enhancing what we have in our business management system and asking: does this best fit our business?
“Too often procedures are thick documents that most people aren’t going to read. They need to be short, sharp, straight, to the point and relevant.
“We need to make sure that, in preparing these, we first engage with the workforce. If I think I’m going to get away with just telling them what they should do, that’s not going to work. You need to engage your people.”
RBG is privately-owned and not listed on the stock market. Does that make a difference?
According to Mann it does.
“I’ve seen in other companies how the stock price is much more important to them than safety itself.
“It’s not that they don’t talk a good safety game, it’s not that they don’t employ people to make sure that they do, but is their heart in it?
“RBG’s heart is squarely in it. We are going to deliver on what we say.”
Recommended for you
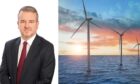