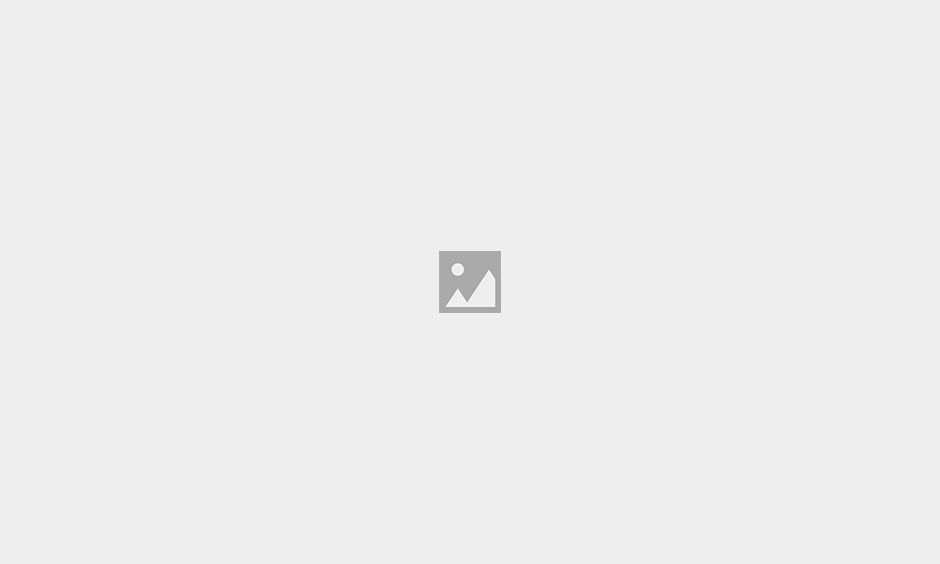
Researchers at Heriot-Watt University’s Centre for Gas Hydrate Research have kicked off phase three of a joint industry project that aims to develop a Hydrate Monitoring and Early Warning System (HMEWS).
The project secured support from five operating companies with help from the Industry Technology Facilitator (ITF), which is based in Aberdeen.
Gas hydrates are ice-like crystalline molecular complexes that can form from mixtures of water and gas molecules under the high pressure, low temperature conditions that commonly occur in offshore pipelines.
The formation of gas hydrates can cause major flow assurance problems and, as the industry continues to mature with more developments in deeper waters, longer subsea tiebacks and higher water cuts, formation of gas hydrates is likely to become more of a problem.
Prof Bahman Tohidi, director of the Centre for Gas Hydrate Research, told Energy that a number of approaches are used to control the formation of gas hydrates, including pipeline heating, insulation and chemical inhibitors.
Currently, hydrate inhibitors are injected at the upstream end of pipelines, but in general, no means have been available along the pipeline or downstream to assess the degree of inhibition.
Inhibitor dosages are based on the calculated or measured hydrate phase boundary, water cut, worst pressure and temperature conditions, and the amount of inhibitor lost to the non-aqueous phases.
“In many cases, high safety margins are used to account for the uncertainties in these parameters and minimise the gas hydrate risks.
“However, despite all these efforts, hydrates do still form and can have considerable economic and safety impacts,” said Prof Tohidi.
Earlier phases of the HMEWS project resulted in the development of a hydrate inhibition monitoring system called HydraCHEK, which is being commercialised through Heriot-Watt University’s spin-out company, Hydrafact.
To date, the system has been purchased by two operating companies, with field trials being undertaken by a further two companies, and it is reported to have shown very promising results.
The HydraCHEK system uses electrical conductivity and acoustic velocity measurements, along with neural network-based software, to determine hydrate inhibitor concentration within the pipeline, calculate hydrate phase safety margins and, ultimately, determine the possible risk of gas hydrate formation.
This information can then be used to adjust the amount of hydrate inhibitor added to the pipeline.
Phase three of the project is aiming to develop the system further to make it more robust and also to develop a system for early detection of hydrate formation.
Prof Tohidi: “Electrical conductivity is an intrusive measurement – in other words, a sensor needs to be in the aqueous phase where it can easily become clogged. What we want to do now is replace the electrical conductivity measurements with a non-intrusive technique.
“This should reduce the need for maintenance and make the system more reliable and therefore more attractive to the operator.
“Previous phases of the project included some work on detecting the early signs of hydrate formation, which we now hope to progress towards a field trial.
“Detecting early signs of hydrate formation will allow action to be taken before a blockage occurs.
“Additionally, it can provide a back-up to the HydraCHEK system and allow greater confidence in working close to the zone of hydrate formation, thus minimising inhibitor dosing.”
Phase three will also allow some promising techniques for hydrate early warning and monitoring that were identified in earlier phases to be explored further.
Keith Mackie, ITF’s technology manager, indicated that this technology could have a number of benefits and has good potential for further development. It could reduce the incidence of hydrate blockage, and more precise dosage of hydrate inhibitors will have cost and environmental benefits.
The system could be used to automate the adjustment of inhibitor injection rates in response to the risk of hydrate formation. The technology could also see application in carbon dioxide capture and storage, as well as gas storage, where hydrate formation can be an issue.