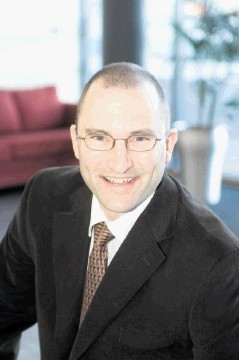
All being well, Total’s Islay satellite development should be brought onstream in just a few weeks as a “daisy-chain” satellite to its Alwyn asset in the Northern North Sea.
While it is a small field, linked to the mother platform via the Forvie North manifold, it is not run-of-the-mill as Islay breaks new technology frontiers with regard to transportation of hydrocarbons to the host platform.
It was in June 2008 that Total said it had made a fresh gas and condensate discovery in the Alwyn/Dunbar area of the Northern North Sea, close to the Jura field.
The find was originally given the name Jura East and made on block 3/15, some 440km (275 miles) northeast of Aberdeen and 5km from the UK-Norway median line, at a water depth of 120m (394ft).
The discovery well was drilled to a depth of more than 4,000m (13,123ft) into hydrocarbons-charged Brent sands. During testing, the well flowed 8,800 barrels oil equivalent per day, including condensates.
While Total was quick to advise that this was a potentially commercial subsea tie-back candidate to existing Alwyn-Dunbar infrastructure, it was also apparent that Jura East, later renamed Islay, presented challenges that had to be overcome if the 17million boe mini-field was to be exploited successfully.
Total’s Islay project manager, Jean-Francois Cam told Energy that there were two key challenges that had to be overcome . . . hydrates and CO2.
Prior to going out to tender for the project in 2009, various studies were conducted by Total in a bid to come up with solutions to both. In the event, it was Technip that secured the engineering, procurement, construction and installation (EPCI) contract.
The £60million (70million euros) contract would involve the world’s first subsea implementation of Technip’s reelable, electrically trace heated pipe-in-pipe (ETH-PIP) technology designed to prevent blockages by hydrates and wax deposition.
Total said at the time that successful application of this technology would reduce capital and operating costs, not just for Islay but for other fields characterised by challenging flow assurance conditions.
And the French oil company said that Islay would act as a pilot project for the use of this innovative pipeline technology, which is designed for both shallow and deepwater environments.
Technip’s full workscope would cover installation of a 6km ETH-PIP, control umbilical, subsea structures and seabed preparation, including detailed design, engineering and project management.
The work would be carried out at Technip’s operating centre in Aberdeen, supported by the company’s Evanton, spoolbase, plus engineering subsidiary Genesis Oil and Gas Consultants and specialist pipeline manufacturer Duco.
Offshore installation would be carried out around mid-2011, using vessels drawn from the Technip fleet, including the new pipelay vessel, Apache II, and diving support vessels Skandi Arctic and Skandi Achiever.
Rob Fisher, Technip’s Islay project manager told Energy: “Hydrates mitigation was one of the main challenges during the pre-project studies. Total with its FEED (front-end engineering and design) partners had developed a concept that they called seabed conditioning.
“That was a world first . . . where they identified that the natural topography of the seabed lent itself to having natural free-draining sumps for which (hydrates inhibitor) methanol can be injected.
“But there were a few too many bumps on the seafloor. You would have needed five injection points. So, the plan was to try and minimise that to one at either end, also a mid-line point.
“Total sought in its specification the contracting community had to achieve a 1:1,000 tolerance in all areas and basically make the ends of the pipeline drain towards where the manifolds would be so that methanol could be injected.
“We proposed a novel solution to solve that problem and, in tandem with that, being a relatively small tie-back, though its small size belies its complexity, Total was also keen to pursue as a pilot project, the deployment of electrically trace-heated pipe-in-pipe for the first time.
“Whilst the heated pipe-in-pipe is the secondary hydrates mitigation measure and is not tied into the permanent infrastructure, though we have developed and built a dedicated power system to be able to plug and play on the heating system, the two went together quite well.”
The primary mitigation challenge was dealing with the hydrates issue, however, a decade’s worth of research had gone into the trace-headed pipe-in-pipe concept that Technip had developed.
But what exactly is trace heating?
“The beauty is that it is a low-power system compared with alternative direct heating technologies – either the direct heating cables that run as a piggy-back such as Statoil has developed in Norway, or direct pipe-in-pipe heating where they heat the carrier and then use the flowline as a return circuit.
“Both are high-powered solutions. However, by layering on trace heating cables against the flowline itself and then surrounding those with passive insulation, you can get a very low-powered solution to the heating problem.”
In a sense, the trace heating system can be compared with the low energy background heating systems that are used to protect greenhouse plants from frost.
“With trace-heating, it’s really about keeping the temperature of reservoir fluids above the wax / hydrates appearance temperatures during shut-downs. In this instance the critical temperatures are 35C and 20-25C.
In Islay’s case the power requirement is 30 watts (equivalent a small light bulb) per metre. Overall, this means 180kW (kilowatts) over 6kW. Research shows that one could go to 20-25km before needing another plug-in point for some more power.
“One can heat the whole pipeline quite happily with an Aggreko (diesel generator) in a 20ft container. It’s that neat. We’ve developed such a container with all the power distribution systems.
“We have four cables around the pipeline. Normal operating mode will be to power two at 15 watts, but our research shows us that, by having thermal passive insulation around the cable, one can still achieve enough heat-spread around the flowline using one cable without getting cold spots.
“We therefore have 300% redundancy, plus we’ve wound two fibre-optic cables on to the flowline, which we can use for temperature monitoring.”
As for the passive insulation system, the contract for this was awarded to the Cabot Corp. Indeed, the Islay requirement was packaged with three other projects that would also require the US company’s same technology.
Known as the Aerogel Compression Pack, it would be applied to a total of 64km of subsea pipe-in-pipe (PiP) flowlines to be installed in the UK and Norwegian sectors for not just Total, but BP, BG Group and Statoil too.
Statoil: Smorbukk NE – a 6 km, 10 inch x 15 inch PiP system.
BP: Devenick – a 34 km, 10 inch x 16 inch and a 3 km 8 inch x 14 inch PiP system.
Total: Islay
BG: Gaupe (formerly known as Pi) – a 14.5 km, 8 inch x 14 inch PiP system.
The use of aerogel insulation on the Islay project is a first for EHT-PiP. While the trace-heating cables run in physical contact along the length of the pipe between the outer wall of the flowline and the insulation, Cabot’s compression pack allows the aerogel insulation to expand around the heat tracing cables, filling any gaps in a single layer, in contrast with traditional multi-layered insulation systems. Originally, it was anticipated that Islay would be developed as a tie-back to Alwyn’s Jura satellite manifold. However, a 2009 study showed that this was not feasible due to the need for a hydrates mitigation strategy that would avoid full depressurisation of all linked fields, as this would result in large quantities of hydrocarbons being flared/vented.
As already mentioned, the pipeline design has to include strategic points where free liquid can accumulate for treatment with methanol.
As a result, four routes were considered for tie-back to the Forvie satellite manifold. A detailed assessment concluded that the preferred route was the direct route running in a straight line and approximately 5.77m in length.
This route minimised the amount of seabed conditioning required in the form of dredging and rock dumping, though it did involve an overlap with the drilling rig anchor pattern associated with the Jura well, a compromise that would be managed.
The Dunbar installation will provide the Islay well with chemicals, subsea hydraulics and electrical power while ultimate control of the Islay well will come from the Alwyn North platform 17km distant via the existing fibre optic cable to Dunbar.
Basically, Islay adds to the growing number of satellites to the Alwyn and Dunbar core infrastructure, but there are issues, in particular the ability of the Alwyn and Dunbar platforms to handle the methanol needs of further Islay lookalikes.
“One of the issues we have with the existing hub close to Alwyn is the limit of capabilities from Alwyn-Dunbar to inject methanol as this would require additional storage and pumps,” said Jean-Francois Cam.
“We might be able to handle further tie-backs to our existing subsea hubs in the near future with existing infrastructure, which we are currently upgrading.
“But now it will largely be a question of economics. Is it better to inject methanol or is it better to have trace heat? Everything will depend on the timing of the maturity of the infrastructure,” he said, adding that, basically, Islay was a kind of laboratory for Total, albeit one with 17million boe available as a prize.