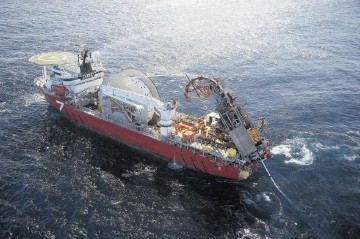
DNV has developed a radical new concept, called X-Stream, that could dramatically reduce the cost of deep and ultra-deepwater gas pipelines while still complying with the strictest safety and integrity regime currently in force.
With the network of deepwater gas trunk-lines set to grow hugely over the coming decade it has become necessary to find new ways of building pipelines.
DNV’s concept is known as X-Stream and is based on established, proven technologies.
The radical bit is how this globally renowned classification society has put the main elements together.
It offers the potential to slice hundreds of millions of dollars off the capital cost of deepwater export lines costing billions to construct and which might otherwise also require a new generation of pipelay ships and semi-submersibles.
Further, due to quality and safety requirements, the number of pipe mills capable of producing the pipe is limited; and for the largest diameters currently available there may only be one competent supplier.
The concept has been peer-reviewed and the Oslo-headquartered classification society is now offering it to the marketplace, essentially free of charge. It could be a game changer.
According to DNV, application of this new approach could swing a deepwater gas development in favour of using a pipeline for export, rather than installing gas liquefaction plant offshore and exporting using LNG shuttle tankers.
X-Stream can reduce both pipeline wall thickness and time spent on welding and installation compared to current deep-water gas pipelines.
The precise reduction in the wall thickness would depend on water depth, pipe diameter and actual pipeline profile. Typically, for a gas pipeline in water depths of 2,500m, the wall thickness reduction could be 25-30%, according to DNV.
It has been instrumental in developing and upgrading the safety and integrity regime and standards for offshore pipelines over the past decades. Today, more than 65% of the world’s offshore pipelines are designed and installed to its standard.
Asle Venas, DNV’s global pipeline director, told industry leaders at a London briefing that controlling the pressure differential between the pipeline’s external and internal pressures at all times is the key to being able to reduce wall thickness. This can be achieved by using high pressure protection valve systems already used in tough environments like the North Sea. The system is known as HIPPS.
“HIPPS has been used for many years offshore and companies are also starting to use it onshore,” said Venas, adding that it had so far not been applied in the US Gulf of Mexico but that DNV developed guidelines last year for application in this important energy province.
“We have 20 or more HIPPS systems installed around the world to control over-pressure of pipelines so they can reduce wall thickness.
“But by utilising an inverted High Integrity Pressure Protection System – i-HIPPS – and inverted double block and bleed valves – i-DBB – the system immediately and effectively isolates the deepwater pipe if pressure starts to fall.
“In this way, the internal pipeline pressure is maintained above a critical level for any length of time.
“The concept is simple and reliable. During installation, it is necessary to fully or partially flood the pipeline to control its differential pressure.
“During operation, the i-HIPPS and i-DBB systems ensure that the pipeline’s internal pressure can never drop below the collapse pressure – plus a safety margin. In sum – a certain minimum pressure will be maintained in the pipeline at all times.
“It will also be important to maintain the minimum pressure in the pipeline during pre-commissioning. This can be done using produced gas separated from the water in the pipe by a set of separation pigs and gel. This technology is not new to the industry. This method has already been initiated as standard practice by several oil companies.”