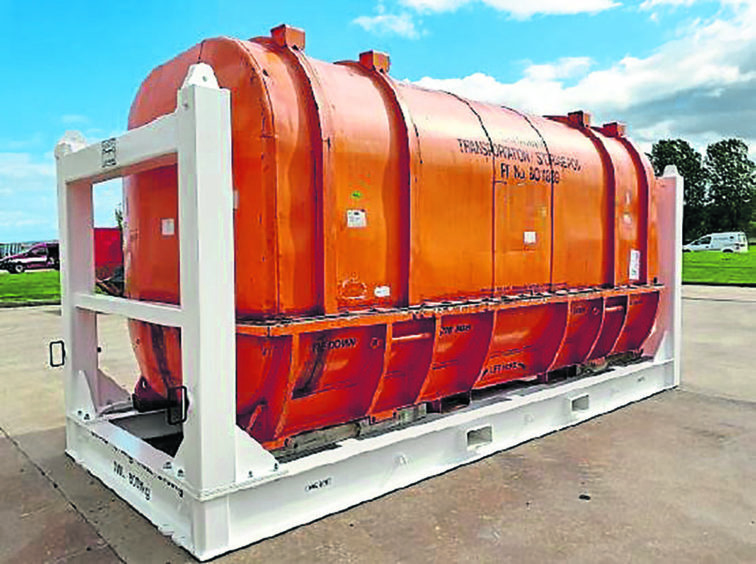
Safelift Offshore’s complete focus during its 25 years of service to the offshore energy industries has been on engineering products to enhance and improve occupational and task-specific safety – and this continues to be the case today.
More so than ever, perhaps, reduced manning levels and the increased use of multi-skilled personnel means having the best item of equipment to hand for a particular operation is essential and having a business partner with a collaborative, fresh and innovative approach to solving often long-standing
industry safety challenges is paramount.
Consistency across different assets belonging to the same operator in terms of the equipment being utilised makes a significant contribution to safety as well because the risk of dissimilarity adversely influencing maintenance or operation is avoided.
This is where Safelift Offshore excels, whether through active participation in numerous industry forums focused on achieving ever-higher levels of workplace safety, or dialogue with a specific customer about their challenge or their safety ambitions in terms of project procurement. Safelift has the specialism and experience to help achieve these aims.
Various items from Safelift’s extensive standard product range have gained wide-ranging industry acceptance over the years, being utilised daily to provide safety for multiple tasks. Typical examples include the Safelift access/egress ladders plus IBC lifting frames.
Increasingly, however, because of an ongoing investment in developing the company’s design and engineering resources, Safelift has been supporting its customers with more bespoke solutions for a particular application where overcoming an inherent safety challenge was of importance.
One recent case study highlights this approach, where the requirement arose to transport a replacement gas turbine from a logistics base to an offshore platform and install it.
It was noticed the turbine’s protective cocoon or pod made no provision for lifting.
Various methods for slinging the load were considered but dismissed. Safelift co-operated with the customer’s team to develop a combined lifting/transportation frame that ensured the safety of all personnel involved in the mobilisation of the unit.
Safelift group sales manager Hugh Ramsay said: “The development of new products or the focus on project solutions utilising our in-house design and engineering resource has meant we’re consistently positioned at the forefront of the lifting and mechanical handling industry and engaged with multiple energy sectors.
“We believe Safelift offers products to the market which are intrinsically safer than other items which the operative may have at their disposal. Our extensive capabilities for the inspection and refurbishment of customer-owned equipment, plus our in-house competency and training provision, add value to this core ethos.”
Further details can be found on the company’s website safelift.co.uk
Recommended for you
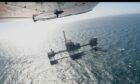