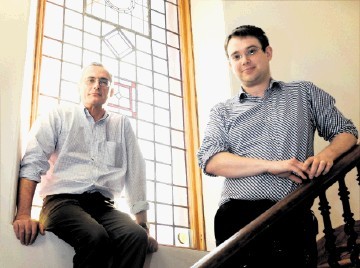
Aberdeen-based oil and gas engineering consultancy Optimus is poised for further significant growth following last year’s decision to strengthen its structural engineering division.
The division was set up in March 2009 as a key element of a plan to diversify and further build the company, which started out a decade earlier as a process and safety engineering specialist.
In just two years since the new unit was started, lead structural engineer Alan Smith has built an expertise in green- and brownfield structural projects, including platform jackets, risers/caissons and topsides, process decks and accommodation modules.
Today, Optimus has a ten-strong team dedicated to structural engineering and the plan is to double the size of this team over the coming 12 to 18 months as part of a major expansion that will push the overall corporate complement well past the 100 mark.
The most recent recruit to the division, Dr Alan Marson, joined Optimus as a principal structural engineer in March, so adding valuable experience in advanced analysis.
“To meet our overall growth plans we have to hire four people a month; we’ve hired 12 people already this year, which means we’re on course,” says founder/director Ian Bell.
“The bulk of the expansion of the business is going to be projects-related and that will mean bringing on engineers in the piping and facilities departments.
“If you look at the consultancy part of the business, I see structural being an equal partner to safety and process, which is what we’re known for.”
“I would say the consultancy arm of the business will be 60 people of which one third will be in the structural discipline. The projects business will hopefully swamp the consultancy part of the business and we expect that to grow to about 100 by the end of 2013/early 2014.”
“We are known for our process, safety business and projects; however, structural is becoming a major stream for us as well. Optimus is becoming an increasingly rounded engineering consultancy.”
Smith joined the company with 15 years of experience in offshore accommodation, especially upgrades/rebuilds for older platforms being put through life-extension facelifts.
“A lack of space often meant there were no particularly simple solutions so it made for interesting engineering,” said Smith.
“At Optimus we started having success, gaining work from fabricators that had major contracts with platform operators but who didn’t carry a full structural engineering capability, or not one at all.
“We add value inasmuch as we can identify and tackle the key structural issues and solve problems. Our structural team has been built around the premise that the people who join us have the relevant knowledge and experience and enjoy problem solving.”
And that is important. The structural team at Optimus see themselves as problem solvers. Moreover, the business is lean, fit and carries relatively low overheads. It is ISO 9001-compliant and has all the correct procedures in place.
A critical issue for the North Sea is how far mature fields and their infrastructure can be stretched . . . in other words life extension.
“How far can a structure be pushed?” Smith asks. “This is why we brought Dr Marson onboard. He brings an in-depth analysis capability to enable us to come up with ideas that make our (brownfield) solutions even leaner.
“We now have the capability to carry out advanced analysis, including non linear assessments of jackets and topsides, dynamic analysis and reliability analysis .”
Basically this is about offering operators of mature assets . . . clients such as Apache, Ensco, Talisman and Workfox . . . a service that could be highly beneficial by ensuring that the true state of their infrastructure is analysed to discover whether it can take life extension re-engineering and additional load.
One of the intriguing facts of the North Sea is that some of the oldest platforms are among the best able to cope with life extension because of the sheer strength of their heavy-launch jackets.
More than 25 accommodation projects have been tackled by the Optimus structural team in three years, generally working to fabricators such as Aiken Group, CPS and Rigfit.
A range of tailored solutions have been applied, from single lift modules of more than 50 tonnes (up to 2,000t); modular structures made up using multiple 10-50t sub-modules; and piece small structures where sections are less than two tonnes in weight can be assembled in seemingly inaccessible parts of a platform.
Smith: “We were asked to put a small accommodation module onto Apache’s Forties Charlie platform. It had a limited existing structure, there was no crane access.
“We devised a method for piece-small assembly so a team could assemble it on the platform. It was 35-40 tonnes in weight, measured 22m by 3.2m by 3.55m high and comprised 56 panel modules. This was almost an ‘IKEA’ solution . . . flat-pack. The job was sub-contracted through Global Energy.”
Looking ahead and given the long anticipated North Sea ‘Indian Summer’, just reinforced by 2012 UK budget concessions, the Optimus team sees a lively market, both for brown- and increasingly, greenfield business.