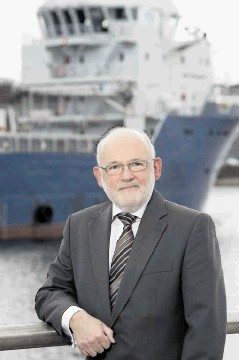
Over 470 platforms, many thousands of kilometres of pipelines and thousands of wells and other subsea infrastructure will be wholly or partially removed from the North Sea in next 30 years at a cost in excess of £47.5billion, with more than half being spent in the UK sector.
It presents huge technical challenges to the operators of the many fields, also tax and supply chain issues, particularly in the UK where Decom North Sea led by its CEO, Brian Nixon, is playing a vital role in bringing focus to the many challenges, teasing through them and proffering potential collective solutions.
In a prior life with Scottish Enterprise as head of oil and gas, Nixon commissioned various reports on decommissioning for the very reason that it has been known about for so long and presents a supply chain opportunity.
That opportunity is assuming much greater importance than even two or three years ago when it represented a stop-start dribble of business.
A massive rump of UK North Sea fields is due to reach the end of the economic road from 2015 through into the 2020s and both operators and their supply chain really must gear up for this as it becomes harder and harder to raise hydrocarbons recovery rates and push back decommissioning.
“It has continually slipped to the right for lots of good reasons,” Nixon told Energy.
“The industry’s been very good at extending the life of asset, and of course it’s a regular question from companies as to when the large-scale decommissioning of fields is going to start. They don’t want to invest and prepare for the future unless there is greater certainty.”
Nixon said the best current information is derived from Oil & Gas UK, petroleum economist Professor Alex Kemp of Aberdeen University, plus DECC (Department of Energy & Climate Change).
“All three corroborate the fact that things have stopped slipping to the right. There is a major lump of work to be done from mid-decade.
“According to OGUK, not only has the slippage to the right stopped for many members, some decommissionings have been brought forward.”
We are getting to the point where installations are at or well past their design lives. The irony is that first generation platforms appear to be the ones best able to cope with major re-engineering for fresh third-party business because they are so robustly built and modular in nature, whereas integrated, cost-pared CRINE generation structures may in fact be the least adaptable and could hit the scrapyard ahead of some old-timers.
Ultimately, there’s a finite limit as to how long one can go on extending the life of infrastructure . . . structurally, process-wise and so-forth . . . until it eventually becomes uneconomic and potentially unsafe too.
o Preparing the supply chain
The challenge is to have a supply chain that is ready, competitive and with the capacity and innovation ability that will be required. Nixon believes too that operators should collaborate, even package several decommissionings together to gain economies of scale from a supply chain so far stymied by stop-start opportunities because only 10% or so UK North Sea fields have so far been decommissioned.
Nixon: “When you look at the size of the programme and rate of increase, there is a going to be a large call on available capacity.
“We’re totally focused on supply chain development, working with the operators, contractors and rest of the supply chain to try and make sure that everybody has as much information as we can possibly give them, as much opportunity to share and to network and learn from the lessons of early decommissioning projects.
“We’re trying to encourage our operator members to try and be a bit more open about their plans and likely contracting strategies so the supply chain can be aware of the issues, technologies and innovations that will be needed, so they can respond.”
But all this is happening at a time when operators are engaged in an Indian summer of new UK offshore developments, not forgetting the high levels of global activity fuelled by regions such as West Africa and Brazil.
Plus there is offshore wind, which is proving attractive to a growing list of oil and gas supply chain firms.
There is another issue . . . people attitudes. Decommissioning boils down to scrapping and recycling. Surely the brightest minds will be tempted away by the shiny new?
So, where’s the talented engineering capability going to come from?
Nixon is optimistic. “The strong message we’re getting is that there is significant interest among engineers. We have a piece of work going on at the moment with the oil and gas MBA students at Aberdeen Business School – RGU.
“At conferences and exhibitions, we’re pleasantly surprised by the number of people coming up to us . . . students and other youngsters because they clearly recognise that this is a 30-40 years programme just in the North Sea, leaving aside international decommissioning.
“It is clear that there are very significant career opportunities.”
What about conversations with engineering departments of universities? Not yet, but Nixon says it is on his radar.
“However, we are working with the ECITB (Engineering& Construction Industry Training Board) and Opito (Offshore Petroleum Industry Training Organisation) to chart out the likely numbers of people needed, from skilled trades through to engineers and business graduates, plus we are looking at the additional skill-sets that will be required.
We don’t yet have a detailed handle on what is required; that work is ongoing and the emphasis is on the supply chain.
o Building a competitive supply chain
“Many companies also see the market potential, transfer opportunities for their skills and technologies,” said Nixon. “Just because it’s decommissioning old oil and gas infrastructure, that could be seen as unattractive. But from a business perspective it’s a potentially good long-term opportunity.”
But how should companies go about carving out a position?
“What we’re doing with RGU, and this will feed into one of the half-day sessions at our October conference, is looking at different forms of contracting strategy.
“The reason for doing that is that we believe operators will obviously retain a very significant responsibility for how work is done, where it’s done and when it’s done.
“The point is that operators will engage with one of a number of different types of management contractor in order to access procurement, planning, engineering skills, etc. We think that each type of project manager will approach the use of the UK supply chain in a different way.
“The work with RGU is to attempt some scenario planning and to try and articulate strategies that favour the use of the UK supply chain; not just onshore disposal yards but, very importantly, the offshore side . . . preparation, engineering and removal aspects.”
“The onshore side is a relatively modest portion of the overall pie. The large majority of the value and business opportunity lies in offshore planning, engineering, preparation and so-on.”
But isn’t the tool kit largely foreign owned?
At the moment yes, but Nixon reckons there is a way of getting around that issue by approaching the dismantling of some infrastructure using smaller crane vessels and jack-ups and taking it ashore in smaller pieces. This is in sharp contrast to Dutch firm Heerema, which is building a vessel capable of removing and transporting the entire topsides of platforms ashore for dismantling.
“Remember, there are different ways of decommissioning and dismantling these things,” he added.
Decom North Sea is also engaged in a North Sea supply chain exercise which will be posted on its website shortly.
It has already become apparent that the various coastal facilities that could receive decommissioned infrastructure have aligned themselves with specific activities: oil and gas new-builds; offshore wind infrastructure assembly and construction; other marine renewable and only some appear interested in decommissioning and in investing accordingly.
“I think the UK will end up with four decom facilities. Able is already active and has a track record; Peterhead will be a strong player with some of the subsea developments, perhaps taking individual offshore modules, pipelines, bundles, that kind of thing; Shetland . .. not only is there Lerwick but there’s also talk of redevelopment of Dales Voe to handle decommissioning; and there could be Nigg which, being the size it is, could very easily handle offshore decommissioning.
“Is it enough? I don’t know. We’ll have to wait and see.”
oHealth, safety and environment
HSE is a huge issue, but the North Sea offshore industry has a lot of experience operationally and Nixon is convinced it is taken just as seriously during decommissioning.
“But the obvious issue is that the longer an operator leaves a platform after cessation of production the worse its condition is going to become and therefore when you start decommissioning, safety surveys to check integrity may be required.
“Another aspect is that, if you are in a deconstruction phase, the work programme, it’s execution, your tool-box talks are going to have to be stringent, frequent and up to the mark because of ongoing dismantling of the workplace.
“This is a totally different environment to that found on an operational platform. Attention to detail will be crucial.
“For me, one of the keys to the whole question about managing and mitigating the numerous HSE risks that personnel will face is the use of our core of engineering contractors.
“They have very refined management systems and they know and understand the facilities. Therefore the likes of Wood Group PSN’s recent (2010) award for the preparation for decommissioning of Brent Delta, that’s a really good sign and I hope we’ll see more of that.
“HSE really is number one on the list with contractors and operators and will continue to be so.”
Recommended for you
