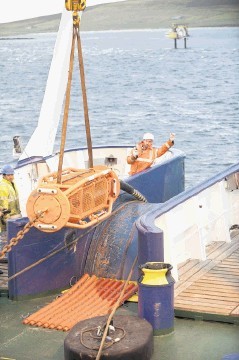
Offshore power cables may not often be seen but they are certainly being heard about.
A crucial subsea link in the wind power chain, these cables are causing headaches for developers, creating delays, insurance claims and increasing uncertainty over project costs.
According to Mike Wilson, managing director at Ecosse Subsea Systems, nine out of 10 insurance claims in renewables were for cables that have been broken during installation and trenching.
He said issues with cable laying is holding up finance – because cost overruns and project delays are making the industry nervous because they are struggling to quantify the risks involved.
Problems include specifications being inaccurate, contractors not burying cables to correct depths and shifting sands in some areas.
Within installation, sledge hammers appear to be being used to crack a nut.
“You have got high-powered equipment trying to handle something that is quite fragile,” said Wilson. “As soon as they get anywhere near the water or get a bashing they break and fail. What is currently being offered is a machine to install the cable and trench at the same time.
“If a high-tow force in the case of a plough is being used if something is wrong and it trips out it will break the cable.
“Or with spinning gnashing teeth on a trencher which carries the cable if something goes wrong it cuts the cable. They are also slow and tend to expose the cable too much.
“More time trenching means more time for the cable hanging off the boat and the more likely it will be damaged.”
The problem is that the priority for an installation contractor or a cable production contractor is not the same and neither were aligned to the client’s needs, said Wilson.
He said that at the moment what trenching equipment is used is decided by what a contractor has, which is dictated by what equipment manufacturers think they need and what they think they can sell.
The vessels used for trenching on the market were for oil and gas which made them larger than needed for renewables work – often even struggling with shallower water depths – and too expensive.
He said the obvious solution was to pre-trench before cable laying with the right-size vessels.
He said Ecosse has developed a plough which pre-cuts trenches and then equipment that can fill back in the trench without touching the cable – and can fit on most size of vessel.
“We have now got all the main cable manufacturers coming to us asking about the equipment and how it can be used to reduce risk of damaging the cables,” he said.
Their system has also been successfully trialled on E.ON’s Humber Gateway project.
The issue is not just in wind, with an increasing number of cables between oil and gas facilities for power and onshore from offshore, also for power.
Recommended for you
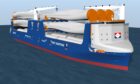