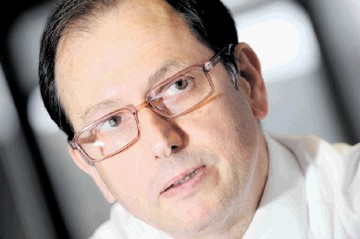
On March 25 last year, a North Sea catastrophe was narrowly avoided when a serious gas leak forced the shutdown of the Elgin/Franklin fields complex for the best part of 12 months.
The huge gas/condensate escape at the Elgin wellhead platform stemmed from retired production well 22/30c-G4, which was being permanently plugged and decommissioned.
Fortunately for operator Total, there were no injuries and 219 non-essential personnel were evacuated from the neighbouring bridge-linked PUQ (process, utilities, quarters) platform and the nearby Rowan Viking jack up rig, which was in-field to decommission the well in question.
This left only the most essential personnel behind who, soon after, were also evacuated, leaving the Elgin/Franklin infrastructure smothered in a cloud of gas and with condensate spewing into the sea, resulting in a fine sheen of hydrocarbons gradually spreading. The flare-stack was still burning though it self-extinguished six days later.
Such was the gravity of the situation that Shell’s nearby Shearwater field . . . also a high pressure/high temperature asset . . . was also evacuated as a precaution and exclusion zones were set up.
The gas/condensate leak had the potential to trigger a Piper Alpha style disaster, but Lady Luck was on Total’s side. The evacuation is widely acknowledged as being of copybook standard as is the remedial work that followed.
But it could so easily have been otherwise had the gas ignited or had the weather been less benign than it was at the time and the wind been in a different direction.
As for the origin of the leak, Total E&P UK’s managing director, Philippe Guys, explained to Energy shortly after the incident that this lay in a tight chalk layer known as the Hod formation, which lies at a depth of 4,500m, above the primary HP/HT reservoir.
The Hod was penetrated during the original exploration and appraisal work during the 1990s and, while it was found to be gas-bearing, it was too tight to allow flow and therefore of zero commercial value.
As part of the original design and in a measure considered prudent, the Hod was isolated using solid steel casing during well construction.
Let’s get back to the well abandonment operations that were being conducted during the early weeks of 2012; a relatively routine process though always demanding great care and caution as elderly wells are hardly pristine. Indeed many suffer considerable integrity problems.
It was on February 25 that an increase in pressure was observed in the C annulus within the 22/30c-G4. This tripped a decision to conduct remedial operations, which began on March 4.
The belief was that the C annulus had failed as gas was observed leaking from the well’s 30-inch conductor. All seemed to be going according to plan, but control was eventually lost on March 25 whereupon evacuation was rapidly ordered.
Quite clearly, Total had to move fast; it had a crisis in more ways than one as Elgin/Franklin accounts for about 9% of UK domestic gas production. However, it was also essential to proceed with the utmost caution and with the minutest of attention to safety. Within days it became apparent that whatever fix was applied, it would take time and the authorities would rightly be rigorous in their attention.
The Elgin platform was rapidly rendered untenable not just because of gas but due to of the spewing volatile condensate and associated paraffinic wax that adhered to everything within reach, making every surface dangerously slippery.
Total brought in a top crisis team from US specialist Wild Well Control and a small team boarded the Elgin platform for a few hours on April 5 to gather information about the state of the platform.
“The fact that gas was still being expelled, one of the first things that we had to do to make the place a bit more accessible was to build a special tool to wrap the (G4) wellhead and divert the flow,” Guys told Energy in an interview that took place last month, just as production from Elgin/Franklin was restored.
“Once that was achieved and the gas and condensate was escaping overboard, we then started on a clean-up and restoration of the systems needed to enable us to tackle the well.”
It was estimated at the time that G4 was flowing 7million cu.ft of gas per day, plus fluids during the first few days, reducing somewhat thereafter.
The number one priority was to kill the well and to do it using every means possible in the hope that one approach succeeded. There were two basic options . . . try a “top kill” by pumping heavy mud into the well and drill one or more relief wells.
The decision was made to deploy two rigs and to attempt a top kill in parallel to drilling a relief well.
“Using these two means is a classic approach . . . one trying from the top and the other by placing a rig at a safe distance and drilling directionally until the relief well intersects the source of the problem, in this case the origin of the gas getting into the (22/30c-G4) well,” said Guys.
In our case we accomplished the top kill before the relief well reached its target.”
Fortunately for Total, the company already had the advanced semi-submersible West Phoenix on contract working West of Shetland. The decision was made to bring it in to handle the top kill by pumping some 2,000cu.m of heavy mud into the wellbore.
The West Phoenix was brought alongside the PUQ platform and flexibles were used to connect the mud pump and tanks on the rig to the well in question. Indeed it was the West Phoenix that killed the well and this was achieved within 12 hours of the at weighted drilling mud pumping operation starting (on May 15).
The relief well, designated G4-K1, was drilled using the semi-submersible Sedco 714. In the event, this well was terminated just 100m from target, as it reached the top of the Hod formation . . . source of the gas/condensate.
“We were that close,” said Guys.
“It took us exactly 52 days to get rid of the leak and get our hands back on the well,” he explained. “These were extremely difficult days but I would say that I had tremendous satisfaction to see how efficient and motivated everybody was, including the wider industry, in terms of helping us.”
So what was the diagnosis for what went wrong with 22/30c-G4 and what was the fix?
Clearly a key part of the fix was to restore life to the two platforms and get them ready for restored production, whenever that might be; abandon G4 in a way that was both safe and effective long-term, and to assess all the other wells to discover whether there were other carbon-copy problems developing.
“It took us quite a long time just to clean and it took us several months before we were ultimately able to fully secure the (G4) well, which had been held using the kill mud pending fitting cement plugs,” said Guys.
“It was in November that we finally completed work on the well, using five cement plugs.
“An important aspect was that we knew that not only the choke (of the well) was filling with gas, we had at a certain point, a failure in the well’s casing. It is because of that failure that the gas was able to migrate via well’s annuli. We put in a lot of thought into trying to understand the nature of the failure and what its origin was. Unusually, it was important to recover the (damaged) section 10-3/4inch production casing so we could begin to understand why we had the failure.
“Eventually we were able to cut the 10-3/4inch casing about 2,300m below the seabed and when it had been recovered we found the place where it had failed. That was of major importance not just to us but also the HSE (Health & Safety Executive).”
It would appear that stress corrosion cracking is the most likely reason for the failure . . . a cocktail of pressure-induced stress, a chemical reaction between different elements and time..
“The well was drilled in 1997 and completed in 1999. During the completion process when production casing was being run, there was exposure to “brine” (in this case calcium bromide to lend weight for well control purposes),” said Guys.
“That calcium bromide reacted with some of the components within the grease that we were using for the joining threads of the casing sections.
“There was nothing wrong with the quality of the casing. There is nothing wrong with the metallurgy. It’s a problem specific to that well. We’ve never experienced the same set of conditions on any other (Elgin/Franklin) well.
“The casing failed at 30% of its nominal value; but then it’s not actually the casing where the problem occurred but at the coupling (threaded joints).
“The failure mode of the casing has nothing to with the geology. At 2,200m the casing failure was way above the chalk formation,” said Guys, adding that the total depth of the well is 5,500m.
In a nutshell, all the wells drilled pre first production at Elgin/Franklin were built the same way, used the same steel casing and jointing system, the same grease.
“The only difference with all the other wells is that the casing was run in mud and not in brine,” he added.
“Of course, we need to wait until the HSE delivers its full report. What I’m saying is that what happened appears to have been because of a unique set of conditions peculiar to that well.”
As for restoring production to Elgin/Frankin after such a long shutdown, there is no precedent for an HP/HT field such as this.
However, Total did successfully restart production on March 11 and, as far as is known, recovery of Elgin/Franklin production has been a success.
As for Philippe Guys and his team, there has doubtless been a collective sigh of relief.
Yes, the forensics continue but the way in which he has been prepared to share his thoughts with Energy is surely a sign of the openness of dialogue that has grown out of 52 days of hell.