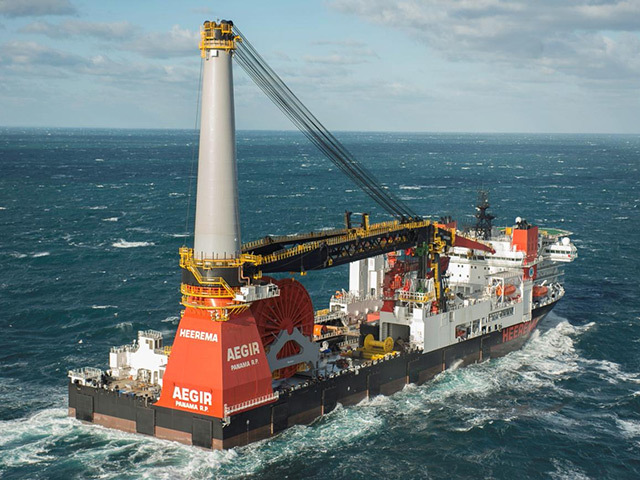
Heerema Marine Contractor has christened a spectacular new offshore construction vessel in Rotterdam.
The Aegir has been designed and built to execute complex infrastructure and pipeline projects in ultra-deep water, while offering sufficient lifting capacity to install platforms in relatively shallow water.
Aside from its signature 4,000 tonnes capacity “mast” crane, what particularly differentiates Aegir according to HMC is that it is the first vessel in the world to make use of a portable reel system.
This is expected to offer huge time and therefore cost savings to both HMC and clients as the vessel no longer needs to sail back and forth to shore.
Aegir was designed by Ulstein Sea of Solutions and is essentially a stretched version of the Seven Borealis, which was commissioned last year and which also carries a massive mast crane.
Construction of the Aegir started in July 2010 at Daewoo’s Okpo yard complex in South Korea.
The basic vessel arrived in Rotterdam in March this year for fitting out with heavy-lift and pipelay equipment at the Huisman yard in Schiedam.
Aegir measures 211m length overall by 46m breadth. According to HMC, some 55.000 tonnes of steel, 1,500km of welding and 1,300km of electric wiring went into creating the Aegir.
Its first project will be the installation of risers in the US Gulf of Mexico Lucius field for operator Anadarko. The water depth at Lucius is 2,000m.
However, Lucius is just a starter snack when compared with the Ichthys project offshore Western Australia where Aegir will really be put to the test.
It was last year that main contract McDermott awarded HMC a contract to transport and install infield flowlines, subsea structures and moorings for the Inpex-operated Ichthys LNG project.
HMC’s scope of work includes the transportation and installation of flowlines, production flowlines, integrated pipeline structures, large subsea structures, a subsea riser support structure, and moorings for future FPSO and CPF facilities.
All pipeline production welding, both onshore and offshore, will be carried out by HMC’s subsidiary Pipeline Technique Ltd.
Project logistics are of an unprecedented scale for HMC in subsea terms.
Aegir will be in charge of lowering over 100,000 tonnes of project materials to the seabed in water depths to 275m. The vessel will make use of its heavy lift, J-lay and reel-lay capabilities all in one project.”
AEGIR FACTFILE
Pipelay Equipment
- Type: pipelay tower for J-lay and Reeling.
- J-lay: Quad joints, 32-inch outside diameter, 2000 tonnes top tension
- R-lay: 2 x 2,000t reels capacity, 16-in OD, 800t top tension.
- A&R system: 2,000t capacity.
- Deep water lowering: 3,500m water-depth, active and passive system heave compensation up to 750t.
Heavy Lift Crane
- Type: Revolving mast type crane.
- Boom length: 125m.
- Capacity revolving: 4,000t between 17m and 40m radius; 1,500t at 78m radius.
- Lifting height: 96m above main deck.
- Maximum radius: 79m.
- Auxiliary hoist: 750t at 23-92m radius.
- Whip hoist: 110t at 31-123m radius.
Auxiliary Cranes
- Pair of knuckle boom cranes, each 40t SWL at 20m radius and 5t at 40m radius
ROVs and LARS
- ROV: pair of work-class systems, launchable from ROV hangars located port and starboard
- LARS: Two (launch and recovery systems) inside the ROV hangars suitable for 3,500m water depth.
Main machinery
- Main power: 48 megawatts total main power plant consisting of six diesel generators each rated 8MW
- Emergency power: One emergency diesel generator set rated 1,600 kW.
Station keeping/propulsion
Thrusters:
- Two 6.5MW fixed pitch, variable speed, underwater de-mountable thrusters for main propulsion and DP.
- Four 3MW fixed pitch, variable speed, retractable thrusters for DP.
- One 2.5MW fixed pitch, variable speed tunnel thruster for DP and manoeuvring.
Recommended for you
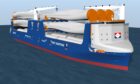