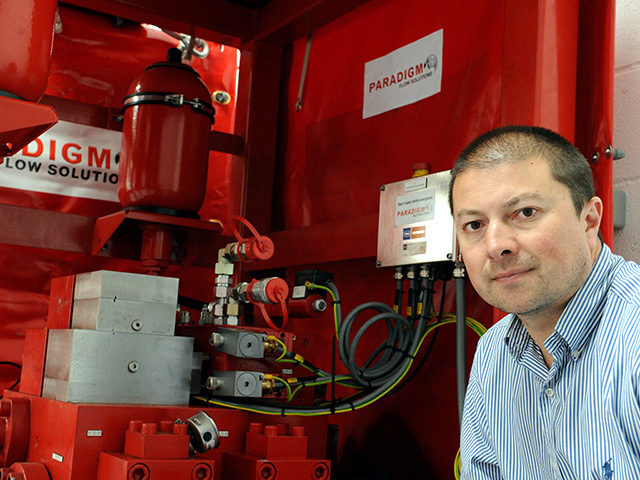
Paradigm Flow Services has logged another record breaking year with turnover rocketing to at least £10million versus £5.6million for 2012; while the Inverurie firm’s EBITDA has leapt from £750,000 to around £2million over the same period.
The forecast for 2014 is £14-15million.
“2013 was a phenomenal year across all fronts of the business,” co-founder and managing director Bob Bain told Energy. “And we shifted from being just UK to doing 55-60% of our business overseas last year, with £3million of revenue coming from West Africa and £2.5million from the US Gulf of Mexico.”
It was a good year on the jobs front too.
“There were just two of us three-and-a-half years ago; we now have 62 and expect to reach the mid-70s and maybe 80 this year. We expect to create another 15-20 annually and we’re forecasting 30-40% compound growth of the business over the next five years.”
Bain said he was especially pleased with progress in the US where the post-Macondo environment is tough and prescriptive.
However, Paradigm had managed to demonstrate that its so-called Pipe-Pulse technology can reduce risk and add value offshore, particularly when applied to the removal of blockages in subsea systems . . . waxes for example.
“We can do it remotely from host platforms,” said Bain. “Flow assurance is a major issue, especially dealing with deposition in flowlines.”
Paradigm has a conveyor of technologies in development and refinement. This month will see the launch of a mini-coiled tubing system designed to serve, for example, production risers and which has been dubbed Flexi-Coil.
It is lightweight, compact and modular, and can be deployed off production ships and other units with limited cranage. Its purpose is to remove debris and blockages.
“Its first task is to remove a ‘sand bridge’ in a production riser for a company operating offshore Nigeria,” said Bain, adding that, conventionally, something like sand removal could cost tens of millions.
Turning to platform deluge technology, he said this had been hugely successful for the company and that a “game-changer” was being developed that would eliminate the wet testing of systems aboard installations. It should be ready for action in a few months.
Bain highlighted two further systems . . . an innovative approach to safely and efficiently flush the contents within subsea umbilical cores (chemical or hydraulic) to a subsea umbilical flushing unit (SUFU); and an innovation designed to monitor production chemicals . . . both composition and checking for contamination.
The SUFU comprises a containerised, bespoke twin-skinned bladder, designed to withstand most solvents and methanol. It is ship transportable and can be lowered to the seafloor and operated autonomously.
“Once connected and tested, the SUFU can be left in position on the seabed unattended by divers or an ROV, while the umbilical flushing operations continue,” said Bain.
“Discharges to the environment can be completely eliminated with this approach, enabling clients to meet regulatory environmental consents. The contents are safety taken back onshore and disposed in compliance with environmental regulations.”
It has been successfully deployed offshore including in Taqa’s Kestrel and Talisman’s Orion fields.
Finally to Chemical Sentinel, a device being developed for monitoring production chemicals before they are pumped into a subsea umbilical. It monitors the “compositional analysis of production chemicals to determine if there are any contaminants that may lead to a blockage”. It is being developed via a joint industry project involving Maersk, Shell and Taqa.
Recommended for you
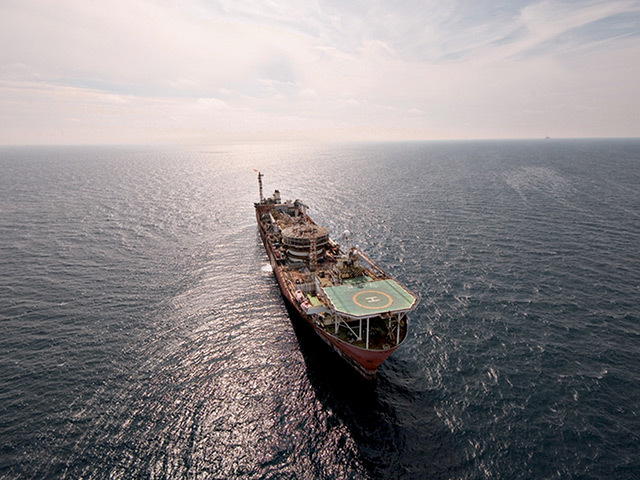