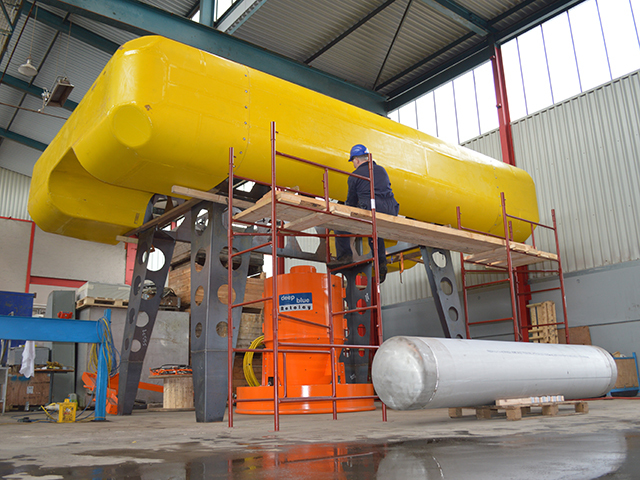
A novel subsea load carrying and deployment system based on a large payload-carrying, remotely operated vehicle has been developed by UK company Deep Blue Engineering of Hereford.
Developed for companies involved in subsea operations, the company says its Shuttle Sub offers an “efficient and cost-effective” way to deploy heavy payloads – such as cables and umbilicals – to and from the seabed.
It is designed to install and retrieve equipment, lay cable and conduct salvage operations.
Even when laden with a payload of 100 tonnes, the buoyant-controlled Shuttle Sub can float, dive, surface and maintain neutral buoyancy. Deep Blue says this means it is “ideally suited” for work being carried out in deepwater environments on or near the seabed.
The firm is to subject a reduced scale prototype Shuttle Sub to rigorous testing during Q4 this year. However, even it will rank among the largest ROVs ever built and will have a four-tonne lifting capacity.
Deep Blue is keen to form a joint venture with an umbilical manufacturer in order to fast track development through to commercialisation of the technology for cable and umbilical deployment.
“An umbilical manufacturer with exclusive access to this technology will be capable of offering lighter weight umbilicals for deepwater applications, and steel tube flying leads that are tens of kilometres in length, with the potential for simultaneous deployment and trenching,” said managing director David Webster.
“This will provide them with a major differentiator and massive advantage within the global market.”
According to Webster, the system is the first lift and deployment system of its kind. Moreover, it is said not to need an additional ROV to conduct visual monitoring or connector installation activities subsea.
Instead, technicians on a support vessel carry out these tasks remotely. As with a conventional ROV, they monitor and control subsea activities via an umbilical between the Shuttle Sub and the vessel at the surface. Where the Shuttle Sub is unique is that it is also the payload carrier, transferring deployment and retrieval tasks to the ROV.
This approach also removes the need for lift line-based operations and eliminates the loads from cables and umbilicals during deployment when they are suspended between the mother vessel at the surface and the seabed.
The Shuttle Sub is designed to perform all of the functions of a work class ROV, but is large enough to accommodate a payload that would normally be deployed or retrieved from a ship.
In addition, deployment should be very accurate because equipment or cable can be placed into position as opposed to working with the lift line, which makes accurate positioning difficult.
Webster reckons that, for those involved in subsea cable and umbilical laying, the Shuttle Sub offers considerable cost-savings.
Traditionally, when deploying cables and umbilicals from the surface, they must be capable of supporting their own weight, as well as any end termination, which dictates major aspects of their specifications, significantly increasing production costs.
But because they would not be deployed at surface when using the Deep Blue system, Webster claims that this is not a factor.
“By using lightweight, low-cost hardware and smaller support vessels for umbilical and cable deployment, costs are dramatically reduced,” he said.
“This advantage also extends to maintaining installed equipment. For example, when a cable within an umbilical is suffering IR issues, it is relatively straightforward to install a single, new cable and create a bypass arrangement.
“In addition, periodic maintenance operations of, for example, subsea processing equipment is easier, with the Shuttle Sub providing a platform to work from, transporting replacement consumables, and retrieving the parts to be changed out. This is completed in a single operation.”
Finally, in the event of a catastrophic subsea blowout or pipeline breach, he says that heavy cutting and capping equipment can be swiftly deployed into deepwater for intervention purposes using the Deep Blue approach.
“This is especially important because it is currently not possible to ‘fly’ this special equipment from a remotely positioned rig or vessel.
“The central environmental benefit lies in the system’s ability to facilitate intervention in deepwater remotely, allowing complex operations, such as sealing pipelines or damaged, uncontrolled subsea wells.”
Shuttle Sub is initially to be made available in two sizes, has a payload capacity of 50 tonnes and 100 tonnes.
The vehicle itself weighs slightly less than its payload capacity, and uses a “cartridge-based” carrying system similar to the container method used in the shipping industry.
During deployment from a suitable ship, the empty Shuttle Sub would be craned into the sea, followed by the payload cartridge.
A range of different cartridges have been developed for different applications. For example, cartridge variants currently include a reel for laying cable, a drum for deploying long steel tube flying leads, and lifting equipment for salvage operations.
Future plans include the intervention and capping capability, and a cartridge with a subsea drilling capability.
The current design can be deployed in water depths to 1,500m. However, a 3,000m capability machine is on the drawing board, with even greater depths contemplated in the future.
Recommended for you
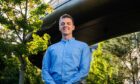