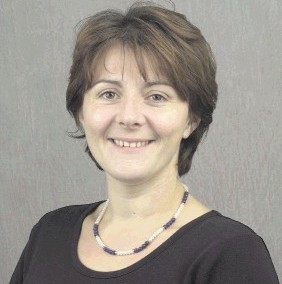
Oil at $50 a barrel or less is having a huge impact on the North Sea industry. Thousands of jobs have been shed already or are vulnerable.
Cutbacks are to the fore . . . capex and opex and while it is claimed that safety will never be compromised, offshore workers are worried and, as should be clear from this exclusive Q&A with Susan Mackenzie, director of the Hazardous Installations Directorate, the HSE will be uncompromising.
Mackenzie: Our basic approach won’t change. The key objectives in our strategy including asset integrity, competence, workforce engagement and leadership are as important now as they have ever been.
Operators and contractors must still control risks to their workers, especially those risks that could give rise to a major accident. Failure to do so threatens workers, production and profitability.
My inspectors will continue to focus on major accident risk control and take action if they find standards are inadequate. I want to see safe production maintained, and I believe my inspectors have a key role in stimulating the industry to achieve this.
Is this idea of maintaining safe production a new approach?
No, this is not a new approach. Managing risk is central to any major hazard business. Accidents and incidents can injure or kill people. They interrupt production, damage plant and introduce costs. They also undermine confidence in the industry. With reduced profitability, making sure assets are capable of maintaining safe production must remain core to sustaining operations on the UKCS.
Industry has been clear; MER (maximising economic recovery) has to be a priority. Economic recovery requires that all assets, from the well to the beach, are available and maintained. It is not my role to dictate to industry where and at what rate they produce, but I am fully supportive of efforts to maintain safe production. I expect my inspectors to act to enable this. I see safe operations and efficient, sustainable production as the same thing.
However, my inspectors will also call duty holders to account if they don’t operate safely.
What do you think industry should be doing now?
Our industry works in a mature basin in one of the most challenging environments in the world. Many assets are now being operated past their original expected design life, so sustaining production is bound to require significant asset maintenance.
We are exploiting deeper, hotter, higher pressure reserves which bring new challenges. This has driven innovation and learning and the rest of the world benefits from this. I don’t want to see the benefit of this investment lost to the UK.
I want to see the skills, knowledge and expertise that created this innovation and excellence applied to the challenge of ensuring cost-effective maintenance that will maximise safe, production across the UKCS now and in the future.
So HSE’s approach isn’t going to change?
No, not in the fundamental standards we expect to see. However, you will have heard me before expressing concern about the maintenance backlog on many installations. I want to make it clear that now is not the time for operators to look to make cuts in safety-related maintenance standards, or to think they can take a more relaxed attitude to asset integrity. Inspectors will be specifically looking to see if this is happening and taking action if they find it.
Operators should continue to identify the key issues for safe operation of their installations and take action to deal with outstanding maintenance. And, I mean deal with the issue. I don’t mean simply reclassifying or deferring the problem and putting it to one side.
Deferments and other delaying tactics are not an acceptable way to manage risk in the long or short term. Inspectors will be looking not only at the safety critical maintenance backlog, but at the overall standard of maintenance to ensure that issues, possibly small individually, aren’t adding up to cause a significant risk.
The offshore environment is highly dynamic. Risks change. Operators and contractors generate the risks. It is their responsibility to manage them.
No one must rely on my inspectors to do their job for them.
You paint a very bleak picture, is there nothing HSE can do to help the industry?
There are good health and safety reasons why we must not repeat the mistakes of the CRINE era, as well as for the long term health and sustainability of the industry.
I want to see a sustainable, efficient, profitable and safe industry. The current price drop may challenge the profit margin this year and next, but we are all in this for the long haul.
I want to help the industry to see that there are opportunities to work together to improve standards and minimise costs at the same time. I’m currently working with the Step Change in Safety Leadership Team to develop a work plan that will help the industry towards these ends, especially through a process of simplification.
I have opened a dialogue with Andy Samuel at the Oil & Gas Authority. I want to make sure that HSE supports him in exploring how industry maximises economic recovery. Maintaining the infrastructure is crucial to this. It is a challenge for all regulators to make sure we support the industry where we can and take a consistent approach.
So how are sustainability and efficiency linked to health and safety?
To me sustainability means that installations, the supporting infrastructure and the workforce are all capable of functioning effectively and are available to allow the safe extraction of reserves now and into the future. Managing asset integrity is at the heart of this.
Both the sustainability of the industry and worker safety are currently being threatened by previous failures to invest in asset integrity. Industry must not make the same mistakes again.
What I have been saying may have seemed to focus largely on hardware, plant and equipment, but this is only part of the picture. It is equally critical that the workforce is sustained.
Workers need to be trained, developed and managed to enable them to be able to operate and maintain the plant effectively and efficiently. The industry needs a strategy to ensure that people with the necessary skills remain available and willing to work in the industry. Maintaining workforce competence so that workers can continue to work safely is as important as maintaining the plant.
A Piper Alpha or Macondo type incident, or the structural failure of an installation on the UKCS would not only be a disaster in health and safety terms; the repercussions would undermine the likelihood of sustaining production in the North Sea.
And efficiency?
Safe production requires effectively managed and supervised, trained and competent people working with the right, well maintained equipment doing properly planned activities. These requirements are also fundamentally important to production efficiency – economic recovery. We need to make sure that we keep this link uppermost in people’s minds. Health and safety is not an add-on. It is fundamental.
And simplification, how can that help?
Simplification can be seen as a subset of efficiency. Unnecessary complexity makes plant more difficult to operate and operators are more likely to make mistakes – bad for health and safety; bad for efficiency and sustainability.
Simplification is not about dumbing down. It is about identifying and focusing in on the essential elements and making sure they are dealt with. This is even more important at times like these, when resources are stretched.
We also need to simplify our standards and guidance and get consistency across the industry. I see this as an essential role for Step Change.
The guidance on what to wear when flying by helicopter has simplified the requirements. Now everyone understands what is required. Things are simplified and standardised, they are more efficient.
We can do the same for a whole range of other matters – contractor competence, basic operating standards, etc. Step Change can drive this and do it efficiently by bringing together and sharing the whole of the industry’s expertise. It can’t be efficient or sustainable for operators to keep re-inventing the wheel and for others to be constantly updating their practices to comply with a myriad of changes.
I recognise that many of the players on the UKCS operate internationally. Nonetheless, there is an opportunity for the industry to work together here. I challenge them to take the drop in oil price as a stimulus to rationalise what they do. All of us must cooperate to share best practice and not simply to invent new approaches to safety just because the standard approach “wasn’t invented here”. This is wasteful. It costs the operator to invent new approaches and it imposes costs on contractors and others who have to handle different processes and procedures all designed to achieve the same outcome.
Simplification also means being clear on what the priorities are and focusing on them. I have made the point before and I will make it again, I think the industry is too initiative driven. We need to focus on addressing the priorities and making the improvements we achieve stick. Nobody can any longer afford to waste effort on making progress and then not seeing that the improvements are embedded for the long term.
Can all this be pulled together, it all sounds very complex?
HSE’s recent Key Programmes KP3 and KP4, looked at maintenance and asset ageing and life extension respectively. KP3 asked if the maintenance was adequately targeted and resourced in terms of people, time and finance. The standards required have not changed. In particular, operators must be able to demonstrate they:
Understand what maintenance is required and the impact of failure to maintain
Have clear plans to deliver necessary maintenance
Can ensure the quality of the maintenance as it is completed and that adequate performance has been delivered
Have the necessary supervisory and engineering support (both off and onshore) to support these operations
Have inspection and audit personnel to ensure competent delivery of all these functions.
It also means that whenever any degradation of plant or a system has an impact on safe production, the operator must assess the consequence.
If the degradation affects a safety critical element, they must stop affected operations or introduce other safeguards – a procedure usually know as Operational Risk Assessment (ORA).
In themselves ORAs can help maintain safe production. However, introducing an ORA is not a substitute for maintenance, it is not a reason to defer essential maintenance.
If ORAs are likely to be in place for the longer term, or they impact on multiple safety critical elements, it might be necessary for operators to submit their safety cases for re-assessment.
So what will make this happen?
You will not be surprised at this; it is a consistent theme of mine. I hear a lot about leadership and about a long term commitment to oil and gas production on the UKCS.
Now is the time for industry leaders to demonstrate they mean what they say: show strong leadership!
The future of this industry relies upon all senior people to scrutinise their business and make it clear how they will manage their operations to ensure long term safe production.
In addition to leading their own businesses, it is important they work together to provide consistent leadership to the whole industry. In particular, they should work with Step Change.
Difficult times give real leaders an opportunity to shine and demonstrate their true strength; I hope the key players will now step up to the plate.
So does the current “correction” present opportunities?
Yes, everyone in industry needs to play their part in Step Change.
Getting health and safety right is a key contribution to sustainability, efficiency and economic recovery.
HSE wants to stimulate and support the necessary changes to enable this, but we will not hesitate to take enforcement action if standards slide.
The price of oil and gas may vary, but workers’ lives do not lose value in a downturn and neither I nor my inspectors will allow the industry to forget that.