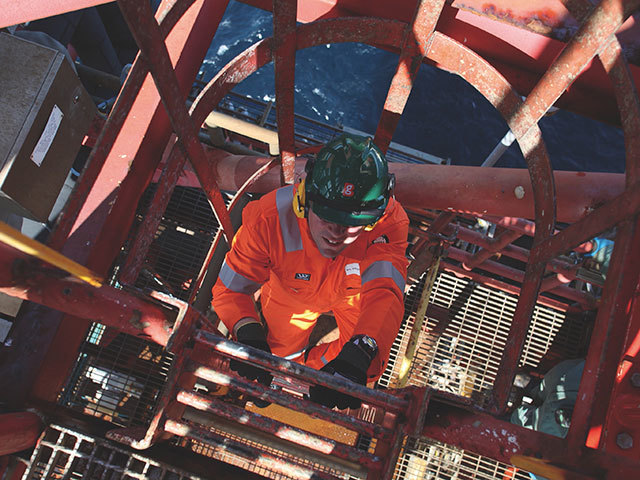
Troubles with ageing oil platforms and their associated infrastructure are just some of the causes of North Sea costs spiralling in recent years – a problem for operators even before the oil price crash started making some of the clunking old kit uneconomic to run.
BG Group had a number of options to consider when it came to its Everest and Lomond platforms in the central North Sea.
One of the plans hatched last year was to sell the fields along with BG’s Armada platform, although as the oil market started on the downturn this idea was shelved.
So BG has pressed ahead with its existing plan to maintain them – requiring a £300million investment which will extend their useful lives to 2025. The Armada platform which BG also operates is still on track to be decomissioned in 2018.
But since the price of Brent Crude has fallen from $115 a barrel last year to settling around $65 now, the operator aims to use the programme to cut the cost of its North Sea operations by 30%, bringing the production cost of an average barrel down to $30.
As part of this, 20 contractors based at its Aberdeen offices will leave this month and it is expected that more office-based contractor roles will come to their natural end as the project does this year.
But the company has also pledged not to take the controversial step of changing its offshore rotas to three weeks on/three weeks off as other North Sea operators have – at least for the medium-term.
In sunshine and calm conditions, standing on Everest’s top level provides a resplendent view of the sparkling North Sea.
The 23-year-old platform is connected to the Central Area Transmission System (Cats) riser, which BG operates but is now owned by Antin Infrastructure Partners. The private equity infrastructure specialist first acquired BG’s stake then that of BP’s in the Teesside gas pipeline for £886million in two transactions this year and the last.
It is just one of the many changes facing cash-strapped operators in the North Sea, as the oil price crisis heightens the need to take action or face collapse.
BG’s decision to press ahead with its initial plan to extend the life of the two platforms comes despite facing its own massive changes – not least the proposed £47billion buyout by Royal Dutch Shell. Earlier this week, the proposed “mega-merger” cleared its first anti-trust hurdle after the United States Federal Trade Commission gave it an early blessing.
Steve Cox, BG’s vice president of operated assets, said the work needs to be done no matter whose name is on the rig: “It doesn’t matter who owns it. Regardless you have to make it a viable business.”
BG initially acquired the assets from rival BP in a swap deal just six years ago. When Everest was commissioned by Amoco, Everest was intended to last for 20 years.
Chris Marshall, the offshore installation manager (OIM) on duty on Everest the day I visit points out the giant mid-life compressor that is due to be replaced, at an estimated cost of £5million. The new kit will adjust for the depletion of pressure from the Everest East gas reservoir it has been exploiting since 2012.
Two weeks ago, the Safe Bristolia flotel arrived in order to accommodate 270 staff from contractors Stork and Wood Group PSN who will be undertaking the wider refurbishment works which will also see the replacement of about 1km of steel pipe and the rig’s caissons.
It was a second coming for the flotel, which had been battered by a North Sea storm two weeks after it had arrived last autumn, only for it to have to be returned to a shipyard in Norway for repairs days later.
But the cloud of having its lifeboats washed out in the storm last year turned out to have a silver lining for BG, in the form of an £18million cost savings and a reduction in the amount of time it will be required to be on site.
Already BG saws it has saved £150million from its North Sea spending this year although it has just fired the starting gun on its wider 30% cost reduction ambition.
More will come from what BG describes as a new operating model. On Lomond and Everest, this means the FTSE 100 oil and gas major will tailor the processes to the requirements of its older North Sea assets – which are different than those required to develop newer schemes such as its £13billion LNG field in Australia which is just starting its 25-40 year life span.”
Mr Cox said:
“One of the key things with this new operating model is tailoring the standards to what late life assets require. Currently we use group-wide standards for all assets in BG.
“That doesn’t mean reducing standards it just means making them fit for purpose.”
SIDE: The trouble with Cats.
As winter 2014 hit the North Sea the important Central Area Transmission System serving the important Armada, Lomond, Huntington and Everest fields was shut down for four months.
As duty holder, BG’s task was to fix the problem which rested on a giant “Borsig” valve on the riser which feeds the main North Sea gas pipeline which extends to Teesside gas processing facility.
The riser is a key piece of the infrastructure. It is the only place the pipeline can be depressurised and BG had to isolate the riser in order to fix the problem.
“The fact we managed to get an isolation at all was impressive.”
See video of BG’s implementation manager Lee Grice discuss the troublesome Cats pipeline riser “Borsig valve” on www.energyvoice.com
Recommended for you
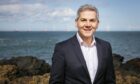