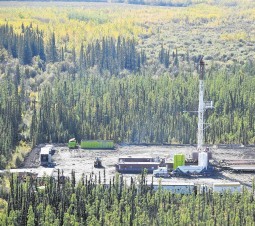
Energy giants Statoil and GE have announced winners of a competition to find new ways of dealing with sand in shale gas production.
The Sand Challenge looked a ways to reduce the environmental impact of transporting sand and water used in the production of onshore hydraulic fracturing operations.
Sand plays a critical role in shale development and the hydraulic fracturing process. Known as “proppant” sand is mixed with water and injected into a formation to “stimulate” or “prop open” the tiny fractures, enabling oil and natural gas to flow freely.
Well stimulation requires hundreds of truck trips to transport materials, which increases road wear and traffic as well as noise, dust and emissions.
The competition looked for solutions that have the potential to reduce the environmental impacts on local communities, lessen emissions and make energy production more efficient.
“Proppant and water are the most trucked materials in hydraulic fracturing,” said Lars Høier, senior vice president for research and development at Statoil.
“We were seeking both a lighter or more compact replacement for currently used proppants and/or new types of fluid or fluid additives that better suspend the proppant and are more efficient.
The judging panel, consisting of both technical experts and management from both companies, evaluated more than 100 submissions from applicants from over 30 countries.
“It is exciting and gratifying to note the quality and quantity of responses, and that many were from industries not related to energy,” stated Eric Gebhardt, chief technology officer, GE Oil and Gas. We are eager to explore these collaborative solutions more as we move toward future testing, development and potential commercialization.”
The winners will each be awarded an initial cash prize of $25,000, and will be eligible to receive additional funding from an available discretionary prize pool of $375,000 for potential development or commercialization upon meeting certain additional conditions.
The winners:
Bioastra Technologies has developed lightweight, high strength composite particles that swell up to 10 times their initial size in liquid. Much smaller in size than other proppants, they can fit into smaller fissures. The particles are also more buoyant, facilitating better suspension in fluid. This material is essentially similar to something first developed for artificial cartilage and occlusion agents for surgery.
Biopolynet has a product that makes fluid more viscous, thus increasing its ability to support a solid. This would counteract the tendency for proppants to settle,making the proppant potentially more effective. It also makes the proppants slightly ‘sticky’ helping the particles to adhere to the surface of fissures in the formation.
Hoowaki’s ceramic proppant has a different “x” shape – differing from traditional spherical particles – shape ‘flutters’ as it moves through liquid, creating drag and reducing settling by up to 50% compared to sand. It also wedges better into fractures, which helps keep the fractures open and prevents the proppant from flowing back with the hydrocarbons and produced water.
Semplastics uses a liquid polymer that is cured to a solid state and then fired to make small spherical particles. These particles have half the density of sand;
however, they are still able to withstand extreme heat and have high corrosion and crush resistance.
The University of North Dakota has developed a proppant that uses local and widely available, non- premium ore, source rock as the base material. This product is
approximately 40% less dense than current ceramic proppants. Because it is lighter it is more buoyant and distributes better through the fractures, meaning
less proppant should be required per completion.