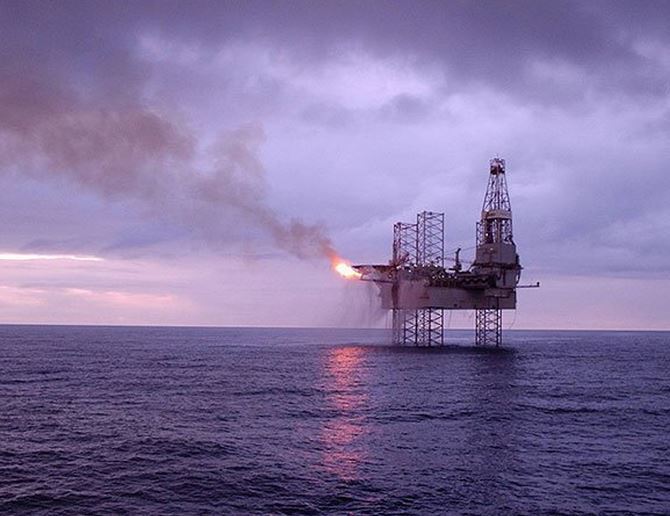
A new North Sea task force has been launched to make the UK sector more competitive and maximise economic recovery.
The Efficiency Task Force (ETF), led by industry trade body Oil and Gas UK, aims to drive pan-industry initiatives to secure improvements that will drive greater efficiency.
The ETF is led by John Pearson, of AMEC Foster Wheeler, and Oil and Gas UK co-chairman.
Pearson said: “The ETF will encourage cooperation and focus on initiatives that add real value for our sector – helping the UK to compete globally.
“Tackling efficiency has been at the forefront of industry minds for some time – but has become more acute and urgent as the value of our end product has more than halved in the last year.
“We now need to step up, increase the effort and resource we’re putting in, and get the job done as a united industry.”
The ETF is taking a three pronged approach under the themes: Business Process; Standardisation; and Cooperation, Culture and Behaviours.
Pearson added: “We are focusing on two or three projects in each. What’s essential here is that we don’t try to boil the ocean. We’ve put a lot of thought into where we can have most impact – and will be working with the industry to see these projects through.
“Only if industry works together can we achieve the major transformation in efficiency we need to see.”
The ETF will focus on three themes including cooperation, culture and behaviours, standardisation and business processes.
Oil and Gas UK said the task force is working to help companies rationalise their inventories, exploring opportunities for the pooling and sharing of items of high value kit and creating visibility of stock holdings across the industry.
The ETF currently holds a dataset of 10 operators’ stock listings, containing in excess of 165,000 items, and is working with those operators to rationalise and reduce their inventory holdings in order to reduce the cost associated with storage and maintenance of materials.
It is also aiming to tackle the efficiency of compression systems, which have been identified as being accountable for at least 20 million barrels of oil equivalent each year in production losses.
Oil & Gas UK’s chief executive, Deirdre Michie, said: “Oil and gas currently account for 70 per cent of the UK’s primary energy demand – a figure which will remain unchanged until at least 2030, according to the Department for Energy. A large proportion of that demand could still be met by oil and gas produced from our resources in the UK. The industry is undoubtedly facing an uphill struggle to maximise recovery.
“Companies have already started on the difficult road to reduce costs and become more efficient. Early signs show this concerted effort is paying off, as production from our sector has increased this year and the cost of operating on the UK Continental Shelf is expected to fall by the end of 2016.”
Business development director Stephen Marcos Jones, who is leading Oil & Gas UK’s support of the task force added:
“At our the meeting of our operator and contractor councils today (Wednesday 2nd September) we will be taking feedback from 100 Oil & Gas UK Council members on our initial projects, and will be inviting the wider industry to share their thoughts at our stand at Offshore Europe this year.”
Today’s announcement comes a week in advance of the launch of Oil & Gas UK’s Economic Report, on September 9 at an industry event Offshore Europe.
The report, based on data provided by Oil & Gas UK’s members, along with information from the Department of Energy and Climate Change (DECC) will provide the most accurate and up to date information about the health of the industry and will underline the need for continued action on efficiency.
In addition to pan-industry action, companies are addressing costs individually by working smarter and more efficiently.
Total has improved the completion of planned tasks by 12% over three months by encouraging offshore teams to use visualisation techniques to help improve the process of planning operations and maintenance activities.
BP has reviewed its inventory management process, halving the number of storage locations, halving the number of inventory items and generating around $32million by disposing of scrap and materials identified as surplus to the company’s needs.
Recommended for you
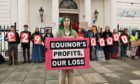