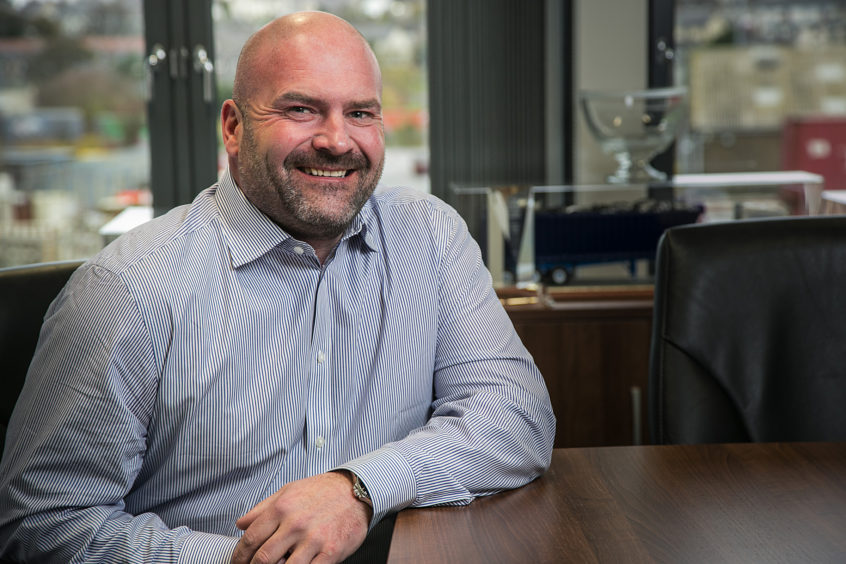
John Lawrie Tubulars UK, one of the largest purchasers of steel tubular products in the UK and across the USA, has further outlined its commitment to supporting the reduction of carbon emissions by undertaking a completely bespoke life cycle assessment (LCA) based on its own unique steel tubular management processes.
The findings detail that for every tonne of repurposed steel tubulars used there is a carbon dioxide equivalent (CO2e) saving of 97.21% over new manufactured prime steel products.
With the energy industry focused on coming together to review ways in which to reduce emissions and support the UK in bringing all greenhouse gas emissions to net zero by 2050, this report details one way to help drive the changes required.
John Lawrie Tubulars repurposes redundant steel tubulars from the North Sea oil and gas industry as a high-quality alternative to new manufactured prime steel products for the construction piling industry. Extending the life of materials through reuse, repurpose and recycling is at the core of the John Lawrie business with the aim of minimising waste, pollution, water and the consumption of finite resources, improving sustainability, reducing environmental impacts and cutting greenhouse gas emissions.
Iain Laing, MD John Lawrie Tubulars UK, commented: “As further commitment to our drive towards a circular economy, we have invested in this life cycle assessment so we can present to our suppliers the environmental impact and benefits of working with us. By repurposing these products in a manner suitable for the construction piling industry, we are helping to reduce the need to produce prime steel piling products, which in turn helps preserve the Earth’s natural resources.”
The report presents the environmental impact and benefits of the repurposing and onward delivery of John Lawrie Tubulars products. It compares the impact of repurposed tubulars to that made by new manufactured prime steel throughout their lifecycle.
He continues: “The results are completely exclusive to our own unique management and operating processes and show that for every tonne of repurposed steel used there is a CO2e saving of 2163.95kg compared to using new steel. That’s the equivalent of driving over 15,000 miles in an average car. And better still, these savings can be achieved in partnership with both our suppliers in the oil and gas industry and our clients in the construction sector enabling them to include these savings in their own environmental reporting.”
Since being founded in the 1930s, delivering significant circular economy, environmental and financial benefits through repurpose and recycling is central to John Lawrie’s business model.