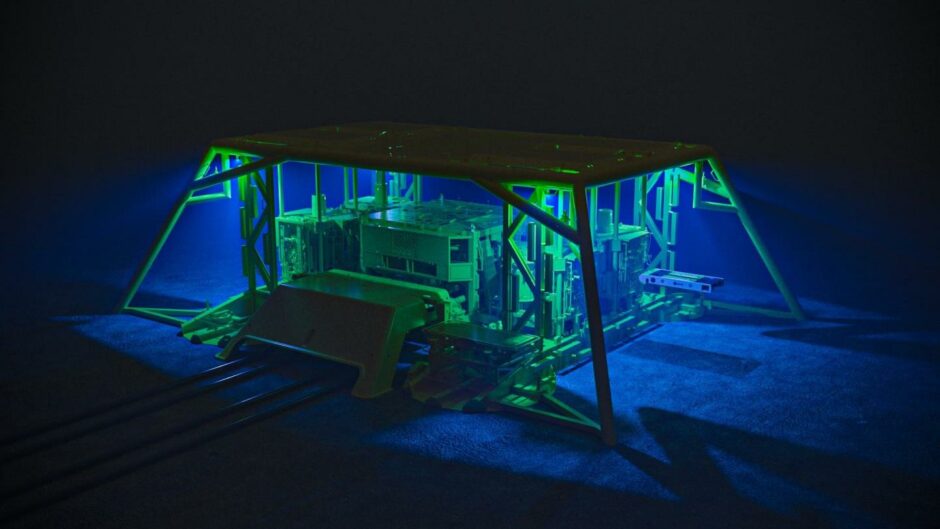
Six years ago, Equinor began a journey towards the creation of standardised docking infrastructure for subsea drones, a new class of vehicle with the potential to revolutionise robotic support in the oil & gas and maritime renewables sectors worldwide.
The Underwater Intervention Drone (UID) is a new breed of hybrid vehicle capable of handling tasks traditionally regarded as ROV territory and those of AUVs.
UID’s are capable of tetherless intervention; either through teleoperation/piloting through wireless communication, fully autonomous intervention or any combination in between.
The UID is regarded as having excellent potential for permanent stabling subsea, returning to the surface only when there is a problem or for servicing, tooling change-outs and upgrades.
But what Equinor is anxious to avoid is the mess of power connectors and standards that characterise mobile phones.
It wants the offshore energy industry to co-operate and settle on a common docking station standard; in effect the USB of the subsea world.
Which is why this energy major – still one of the largest oil & gas operators in the North Sea and a leading investor in offshore Big Wind – has so far been prepared to dig into its pocket and foster the development of a free issue technology.
It is fostering co-operation through the SWiG standard interface initiative with brands like Chevron, Total, AkerBP; also drone developers/manufacturers like Kawasaki, Oceaneering, Saab, Saipem, Sonsub and Subsea 7.
Equinor engaged Blue Logic of Stavanger to set the development ball rolling. The objective was not to create a niche product, but an industrial standard for everyone.
Two linchpin figures in the project at Equinor are principal engineer Jan Christian Torvestad and Stine Vemmestad Vatneberg, process technology manager. At Blue Logic it’s the firm’s founder Helge Sverre Eide.
The impact of their work on the UID docking station has already been so great that, in the autumn of 2019, for example, Equinor entered into the world’s first contract for an advanced underwater drone. The contract was with Saipem covering drone work in Njord field.
Equinor said in October 2019: “This is a historic contract in the oil and gas industry. It is the first contract signed for the use of advanced wireless drone services.
“Equinor aims to help shape the development of this type of technology, which this contract underscores.”
The following year, Blue Logic won Norway’s ONS 2020 Innovation Award for its pioneering open-standard subsea docking station for underwater vehicles.
Late last year, there was a major breakthrough when Equinor qualified the docking station and awarded Blue Logic a frame agreement for the delivery of drone stations together with subsea equipment, and services. This basically opens the door to service drones living infield, not just in oil & gas fields but offshore windfarms too.
And further pioneering tasks on the Norwegian Continental Shelf for Equinor are on the books, including trials at Johan Sverdrup for which preparations including extensive drone testing are well advanced.
Stine Vemmestad Vatneberg told Energy Voice: “We’re proud of our technology history, especially in underwater robotics and automation.
“This is an important focus area within Equinor. We’re really accelerating our efforts to ensure broad implementation of a range of technologies.
“As regards the underwater intervention drones, they offer an opportunity for us to radically change how we do subsea operations.
“It offers opportunities for improved safety through efficient remote operations rather than personnel offshore.
“It will deliver more inspection data which, in turn, will enhance our understanding with regard to technical integrity and allow us to make better decisions.
“These underwater intervention drones will reside on the seabed, reducing the need for the kind of surface vessel support that is required for more traditional (ROV) operations. This in turn offers the potential to reduce the carbon footprint of future subsea operations.”
OK, so Equinor is several years into offering the offshore energy world a standardised, open access docking stations for UIDs.
But in the uber-cautious offshore oil & gas industry, the tendency with new technologies is for operators to hang back. They want someone else to take first risk and it is something the Norwegians are very good at. There is also respect for Equinor’s leadership.
Vatneberg said the company is concentrating on working with three or so prototypes such as Oceaneering’s Freedom.
Reality is that the various service company actors have been working on next generation subsea vehicles of various configurations for quite a while.
For example, i-Tech Services (a Subsea 7 company) has for the past 25 years or so been actively developing an autonomous subsea inspection vehicle capability to support and maintain the integrity of subsea production assets. But it travels to and from its mothership in a recovery basket that resembles a nest.
The challenges are immense; they always have been in subsea.
Jan Christian Torvestad: “It was around 2017 when we decided to try and design a generic docking station that was independent of the vehicles.
“It wasn’t straightforward because the traditional (ROV/AUV) docking station is a mechanical cage which mechanically steers the vehicle into place.
“We ended up with a flat surface concept … a parking lot that could cope with different sizes and types of drone.
“And then we started to develop the means of transferring energy through inductive power, alliancing with Blue Logic, which had already made a lot of input to API 17H.”
To explain, the American Petroleum Institute’s Recommended Practice 17H provides recommendations for development and design of remotely operated subsea tools and interfaces on subsea production systems to maximise the potential of standardising equipment and design principles.
“After extensive discussions we agreed to creating an open standard that can be utilised by all involved with the subsea drone market,” continued Torvestad.
“We also decided to make it free to the industry … including to oil and gas companies.
“As Equinor is quite a large subsea supplier (player) and ahead in developing the use of subsea drones, we can shape the market to a large degree, though this depends on securing the co-operation of others.
“To a certain degree we are defining a standard and it seems like many other suppliers are gradually agreeing and rapidly adopting it.”
In developmental terms, Torvestad said that the breakthrough at Equinor was in November 2021 “when we finally qualified the docking station internally, having successfully completed several repeated, automated dockings.”
Vatneberg said: “This year will see us implement the docking station at Njord and Johan Sverdrup and we will trial different tasks; initially easy ones; for example inspection during the commissioning of wells. We will test a leak detection capabilities, also autonomous pipeline survey.
“Next year we aim to advance the capabilities of the solutions … with robotic arms for example, to carry out light intervention work; evolving from remote control to pre-programming tasks to be performed autonomously.
“We have quite large ambitions when it comes to implementation across our assets; and so we’re now working to define what that potential might be. I think we currently see only the top of the iceberg of possibilities.
“This is relevant not just to oil & gas but also the growing renewables marketplace where Equinor is a leading player in offshore wind.
“The longer term vision here will be to have a common infrastructure of subsea docking stations across the continental shelf. Also, we’ll work with different UIDs on a range of tasks across different fields and with various operators.”
Given that Equinor is among the leaders in the development of offshore windfarms in European waters, this suggests that the company is in a strong position to influence subsea working practices … assert itself given its subsea pedigree.
Vatneberg agreed: “We see it as a competitive advantage operationally.”
But she warned that dealing with Big Wind is different to the long-established North Sea oil and gas industry. There isn’t the same level of regular contact with the various associations and government departments supporting windfarm development and operation in this regard, or for that matter, experience.
The vision is to have drones stationed in-farm permanently, as with oil and gas fields. The 3.6GW Dogger Bank project (Equinor 40%, Eni 20%, SSE 40%) is seen as being an early testing ground for the UID stations.
Meanwhile, the accent is on oil and gas; getting UIDs and their docking stations working efficiently at Johan Sverdrup and Njord first, while also looking to the wider oil and gas production portfolio.
“We’re already working to secure this broad implementation,” said Vatneberg. “In parallel to the first user projects like Johan Sverdrup, we’re mapping our assets to work out where we should go next.
“It is also important to ensure the technology becomes available on the market and that we invite tendering for systems. We’ve set up a project to specifically focus on implementation across the Norwegian Continental Shelf. We’re accelerating our efforts to capture the value of the achievements so far.”
This won’t be straightforward. You can’t simply bolt on and plug-in UID stations into existing fields and expect them to work immediately at the flick of a switch.
Torvestad again: “The communications side could be more difficult. If you’re gathering a lot of data with a drone and you want to upload that data and you still have copper (connectors) on board an installation, that could limit what can be handled.
“Bear in mind there are two classes of data. Real-time, in order to be able to control a drone in a safe manner, and the other one is collected Big Data which we intend to store in a cloud in a systematic way, ready to be looked through in the future, perhaps with algorithm tools.”
To quote Blue Logic’s founder Helge Sverre: “It would be very cost-efficient if we can have an industry standard that only needs a few adjustments for every field. It makes it a lot easier for everyone.”