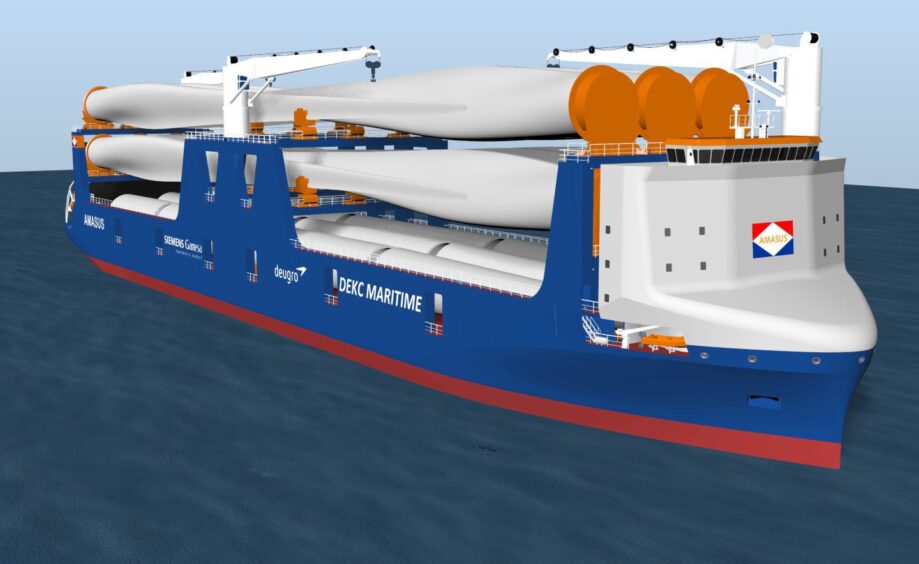
2024 ended on a high at Concordia Damen, with the Dutch shipbuilding group reaching the roughly halfway stage in the design, build and delivery of two 550ft (167.5m) roll–on–roll–off wind turbine systems carriers for fellow Dutch company Amasus, with delivery of the first sister expected later this year (2025).
The Rotra Futura and Rotra Horizon are being built at the Jiangsu Zhenjiang Shipyard in China, with the Futura launched late November.
The design of the Rotra Futura and Rotra Horizon builds on the previous vessels in the Rotra concept, the Rotra Mare and Rotra Vente, which were also developed by Concordia Damen, and have been successfully operating since 2016.
The two further members of the class are being equipped with the latest generation of larger, heavier turbines.
Ro/Ro vessels are commonplace, but few are this sophisticated. Their cargo ramp system coupled with a trio of Liebherr cranes will enable turbine blades to be stowed in three tiers, providing greater flexibility in loading methods and cargo configurations.
The aerodynamic and hydro-optimised hull design, combined with a low-resistance coating system is expected to help reduce fuel consumption.
The main propulsion will be Wartsila-based and optimised to consume 15% less fuel and deliver a smaller CO2 emissions footprint than current standards demand.
Meanwhile, Ulstein of Norway has delivered the windfarm construction service operation vessel (CSOV) Olympic Notos to Olympic Subsea, which is a well-known Norwegian brand in the North Sea oil and gas industry.
There are high expectations from this vessel in terms of economy/environmental performance based on experience with in-service sister.
Olympic Boreas, which Ulstein reports has been operating with a “close to a 50% reduction in fuel consumption compared to other CSOVs”.
According to Olympic’s chief commercial officer Glenn Erik Valø, this is important from both a sustainability and commercial perspective, given that the scheduled implementation of the EU Emissions Trading System (EU ETS) for offshore vessels from 2027 will lead to higher fuel-related costs for vessels running on conventional fuels due to the need to compensate for emissions.
These are the first CSOVs to employ Ulstein’s proprietary TWIN X-STERN system, with four main thrusters fore and aft in a symmetrical dual-stern (double-ended) hull, allowing uber-flexible operability in dynamic positioning (DP2) mode.
As a result, the Boreas was recently dubbed “the four-wheel drive of the sea”.
This 4×4 arrangement is complemented by diesel-electric propulsion with variable speed, hybrid battery power, energy storage and smart energy management to maximise fuel efficiency.
The CSOVs are also equipped with a shore power connection for emission-free port operations and battery recharging, otherwise known as “cold ironing”.
They also have space for extra battery capacity, enabling future full-electric operation once the necessary infrastructure becomes available at sea.
Based on the workhorse Ulstein SX222 design, the 89.6m sisters are intended to serve both offshore wind and oil and gas clients. They offer accommodation for 126 people in 91 cabins.
Each is equipped with a heave motion-compensated gangway system for efficient transfer of personnel and cargo at variable landing heights.
Cable Layer
Elsewhere in Norway, Salt Ship Design has been selected as the designer for the world’s largest cable-laying vessel (CLV), which has been commissioned by Penta-Ocean, a Japanese company based out of Singapore.
The vessel, which will support the Japanese offshore wind market, is being built by the PaxOcean Group of Singapore.
The ship is due for delivery in early 2028 and has been designed to be ready to burn methanol fuel, backed by a battery energy storage system.
It will be fitted out to handle cable laying and burial for bottom-fixed and floating offshore wind farms, as well as submarine direct current transmission cables.
Key features of the design include:
- Two 5,000-ton cable carousels (10,000t total capacity) for large wind farms.
- Advanced trenching and cable burial systems utilising the latest ROV and trencher technology from SMD (UK).
- High-precision ClassNK DPS2 dynamic positioning system with seven thrusters (16,000kW output).
Conversion
Finally, and still in Norway, shipbuilder Vard has delivered the IT Infinity to International Telecom Marine SRL after conversion from a platform supply vessel to cable-layer for the telecommunications sector.
Built at Vard Brattvaag and delivered to Volstad Maritime in 2008 as the Volstad Princess, the ship was bought by SD Standard Drilling in 2017, before it was sold to IT in 2021 and renamed “IT Infinity”.
The transformation covered:
The addition of new accommodations for 32 people required approximately 550 tons of steel, plus the installation and integration of a suite of cable equipment and associated systems.
This included a 60-ton A-frame, 25-ton cable drum engine (CDE), 20-ton linear cable engine (LCE), MD3 cable plough system, remotely operated vehicle (ROV), Fiber optic cable testing and jointing equipment and upgrade of the ship’s station keeping system to a fully operational DP2 Class approved positioning system.
Recommended for you
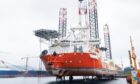