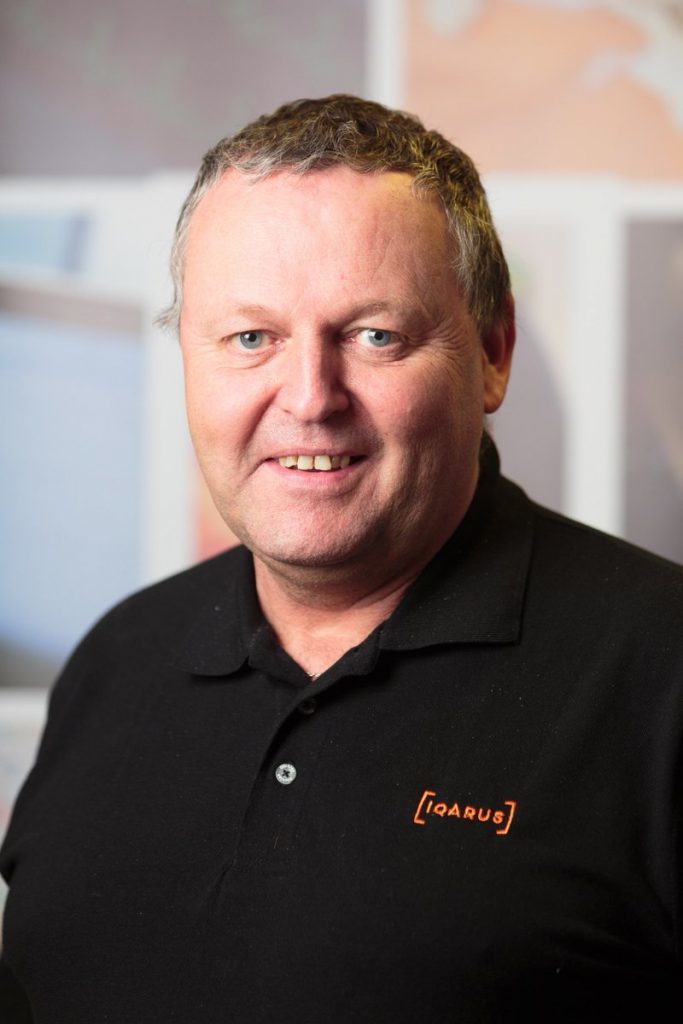
According to the HSE, there are more than 20,000 or so noise induced work related diagnosis reported in the UK each year.
This is a significant number which requires significant focus, however, there are far too many examples of companies adopting a poor noise management strategy, ultimately impacting their business performance and affecting the wellbeing of their employees.
Risk managers at oil and gas organisations are responsible for evaluating everything from hazards as diverse as global infectious disease outbreaks, to the impact of sickness absence due to chronic illness.
A UK report put the cost to employers, who pay sick pay and associated expense, at about £9billion a year (Health at Work – an independent review of sickness absence by Dame Carol Black and David Frost, CBE’s UK report from 2011).
The aim of a noise risk assessment, as required by law, is to help you decide what you need to do to ensure the health and safety of your employees who are exposed to noise.
It is more than just using equipment which takes measurements of noise, but this is usually the first step.
The use of such equipment is not simply reading the instructions, pointing and writing down numbers. It needs to be far more coherent than that and form part of an integrated approach which audits, monitors, assesses, acts and measures.
Any element of measuring and monitoring requires a person to be competent to do so. The ‘Control of Noise at Work Regulations 2005’ require those responsible for noise measurement and monitoring to have the appropriate training and qualifications to be able to develop information, instruction and supporting guidance for their companies.
Understanding the benefits of measuring equipment is important; however, also understanding its limitations is even more significant.
Knowing what it does not deliver is a fundamental element of what happens when the need to risk assess is recognised. How accurate the readings need to be, is the first consideration.
The law requires that noise sources are identified, however, in a busy worksite; this is difficult to do without the use of octave band analysis. This is a fundamental element which needs to be considered as it is also used to calculate the efficiency and suitability of hearing protection.
This is where companies will face some significant challenges. Not being able to achieve the level of accuracy by having inferior equipment can hinder the efficacy of a noise management strategy.
The statutory assessment and limit values within the Regulations can be determined by noise dosimeters as the primary choice, or by fractional exposure calculation built up through a combination of noise mapping and details of work patterns as additional data.
However, a combination of lack of competency and the wrong type of instrument can be disastrous and can cause noise induced hearing loss from noise at work.
Businesses do have options.
Progressive companies are now introducing a noise meter on site for monitoring purposes only, and are utilising expertise such as an occupational hygienist to provide the detail needed for compliance of all elements needed to keep the regulator happy.
An occupational hygienist or a member of the Institute of Acoustic have recognised competency frameworks acceptable to the HSE and therefore ensure the best chance of managing the risks associated with noise at work.
Having a noise meter to measure noise doesn’t ensure compliance if it is operated by someone who is unsure of how to use the data, or has no understanding of the calculations needed and the statutory duties associated with a noise risk assessment.
This, as we know, this can have a direct impact on the bottom line through lost days through absentee-
ism as well as lower productivity of staff.
Organisations are wise to implement robust health systems to ensure long-term success, productivity and profitability.
A good noise management strategy isn’t just about ‘doing the right thing’ for staff, it’s a fundamental part of business growth.
Dougie Collin is executive director, occupational hygiene, Iqarus.
Recommended for you
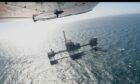